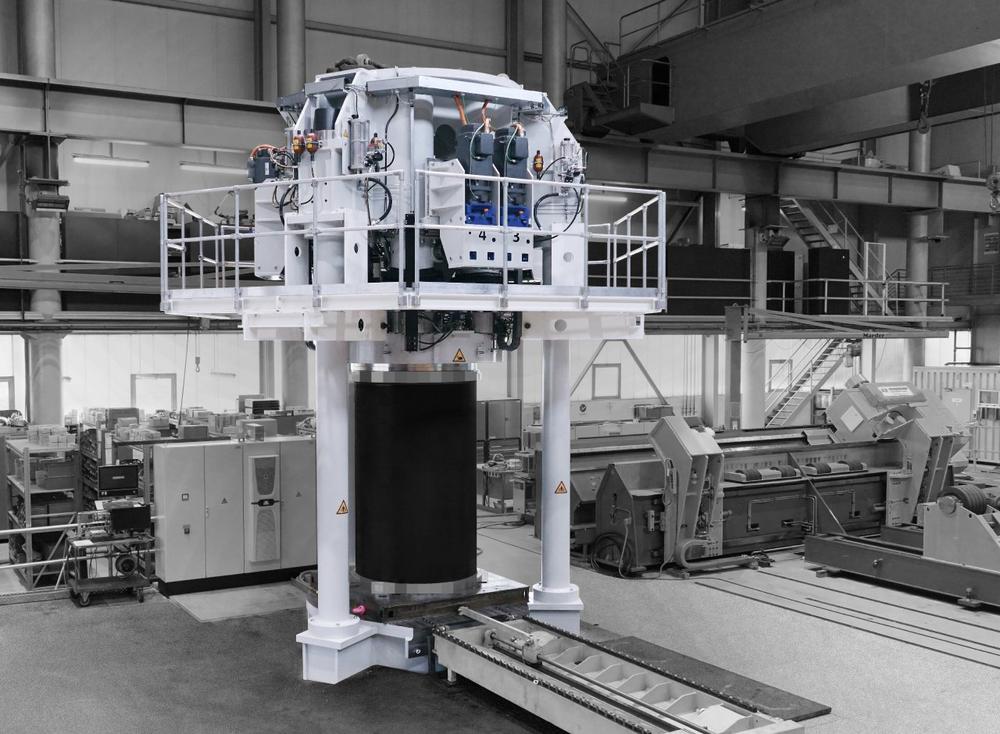
First Graebener stack press realized for world’s leading electrolyzer manufacturer
Graebener Bipolar Plate Technologies focuses on the development of technologies and machines for the production of fuel cell and electrolysis components, such as the metallic bipolar plate. The latest development is a press that is used in the manufacturing process of alkaline electrolyzers.
Electrolyzers make a significant contribution to the energy transition because they can be used to convert electricity, preferably from renewable sources, into hydrogen. This, in turn, can be used in a variety of ways as a green energy source, for example to decarbonize the industry. The heart of every electrolyzer is its stack, which consists of hundreds of stacked single or bipolar plates. The chemical conversion of electrical energy into hydrogen then takes place within these stacks.
As one of only a few companies worldwide, Graebener offers not only individual machines for forming, cutting, welding and straightening metallic single and bipolar plates, but also complete lines for series production: from coils to welded and leak-tested bipolar plates. Graebener has long been known for this. The recently developed system, however, is used in a later production step, namely in the manufacturing of the actual stack.
Technology to support stack testing
The Graebener stack press supports the technical testing of electrolysis stacks at the end of their production process: The pre-assembled stack, which consists of a large number of plates, is first moved into the machine and then compressed to a defined height until a certain pressure is reached within the stack. This pressure must then be maintained unchanged for several hours. At this time, the stack is subjected to all the necessary technical tests carried out by the customer and with the help of further procedures. These are necessary to confirm its full operability. As soon as the tests are completed, the stack is finally assembled with tie rods or tension straps and the finished stack is removed.
Precision with maximum safety
The stack press for electrolyzers has a force of 800 tons and can handle stacks with a maximum height of approx. 3.0 m, a maximum diameter of 1.60 m and a weight of up to 12 tons per stack.
In order to be able to guarantee assembly work during operation with maximum safety, a hydraulic drive was deliberately avoided. Instead, the stack is compressed inside the press by means of six servomotor-driven spindle units. These are operated synchronously and thus enable particularly homogeneous compression of the stack. The maximum pressing force per spindle unit is 150 tons.
The biggest challenge was to compensate for production-related stacking tolerances. Stacking tolerances are unavoidable, but when the stack is compressed, they cause transverse forces which can damage the stack. In order to eliminate these and to build up an even pressure distribution within the stack, these transverse forces must be continuously compensated for during compression of the stack. This is done with short-stroke cylinders that are located under the six spindle lifting elements and enable an even distribution of pressure.
As a custom machine builder, Graebener always develops its machines to meet specific applications and customer requirements. Graebener had already realized a similar press in the past, but at that time for fuel cell stacks. However, since plates for alkaline electrolyzers – and thus also their stacks – are usually many times larger, the design of the current system was much more complex.
Graebener® Bipolar Plate Technologies is part of Graebener® Maschinentechnik, a medium-sized, family owned machine building company with locations in Netphen (Germany) and Houston (USA) as well as various international representatives. For 20 years, Graebener® has been one of the first companies to focus on the research and development of manufacturing processes and machines for fuel cell and electrolyzer components.
The company has dedicated itself to setting the quality standard for manufacturing technologies by developing innovative processes and machines that help to manufacture fuel cell and electrolyzer components, such as the metallic bipolar plate, that are tailor-made, integrable, scalable and thus economically efficient.
For this purpose, Graebener® accompanies all strategically important steps towards the optimally designed production line: Starting from engineering with a view to plate design and line concept via prototyping and small series production in the in-house production laboratory up to the customized production machine or line. Experience from more than 100 years of metal processing and worldwide customer-specific special solutions are incorporated into the holistic development partnership with the customer.
www.graebener.com
Gräbener Maschinentechnik GmbH & Co. KG
Am Heller 1
57250 Netphen-Werthenbach (Bhf.)
Telefon: +49 (2737) 989-0
Telefax: +49 (2737) 989-110
https://www.graebener.com
Gräbener Maschinentechnik GmbH & Co. KG
Telefon: +49 (2737) 989-369
E-Mail: s.rohde@graebener.com

