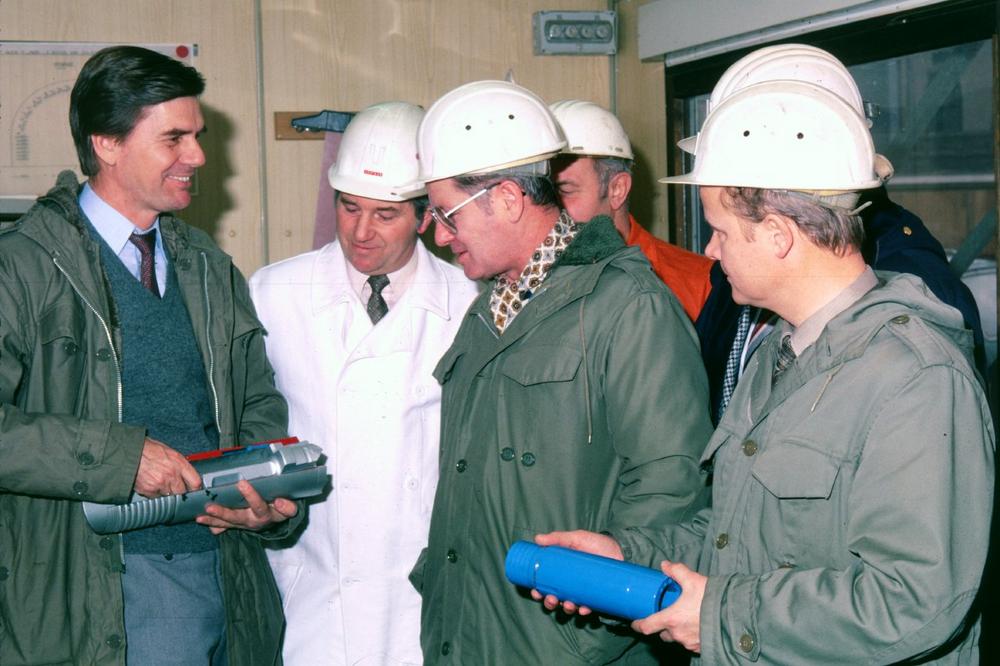
KLEMM Bohrtechnik GmbH celebrates double anniversary
How it all started
In order to carry out drilling and blasting work to extract stone material for dam construction, Guenter Klemm founded KLEMM Bohrtechnik GmbH in 1963. During the early years, the company focused on blast hole drilling in quarries and road construction as well as injection drilling for sealing dams. Soon the company began to manufacture individual pieces of drilling equipment, such as drill bits and drill strings, for its own use.
Later on, the company became a specialist in overburden drilling. This method is frequently used in specialist foundation engineering to tie back excavation pits. To successfully manage the considerable order volume even better and faster, employees worked continually on improving the drilling equipment. The focus shifted increasingly toward the development of drilling rigs and drilling accessories.
In 1967, a milestone was achieved: Guenter Klemm invented a device for overburden drilling. He combined a deep hole hammer with a rotary percussive overburden drilling system, while also bringing together the flushing head with an excavating head. This principle considerably improved the discharge of drilling debris and remains the state of the art to this day.
From drilling company to drilling equipment manufacturer
Construction drawings from 1970 demonstrate how far Klemm had already progressed in its transition from drilling company to equipment manufacturer at the time. In 1972, Klemm entirely ceased its drilling operations. This is when the company presented the first hydraulic drilling hammer – a ground-breaking innovation. The hydraulic drilling hammer significantly enhanced performance and improved energy efficiency considerably compared with conventional compressed air methods. Guenter Klemm was informed about the details of the new anchor drilling technology by Dr. Karlheinz Bauer. Even back then, Dr. Bauer showed his first signs of interest in acquiring Klemm.
The main business was now the sale of drill strings, drilling accessories and enhanced flushing heads, particularly for overburden drilling. Klemm continuously enhanced the method of overburden drilling – all the way to double-head systems, which combined a hydraulic hammer for the drill string with a rotary drive for the external casing. Thanks to this technology, overburden drilling established itself as the standard drilling method in specialist foundation engineering worldwide.
During the 70s, Klemm developed its first hydraulic hammer with a rotary drive, the S30. The KB 40-B and KB 40-O systems came to replace the deep hole hammers powered by compressed air that had previously dominated the market. In 1974, KL Klemm EMM presented a drilling rig with a diesel-hydraulic drive, crawler and movable drilling carriage: the drilling rig type KR 800 was born.
KLEMM also registered a number of important patents in the 70s, for example frequency control of the impact piston and a protective circuit for the pressure tank. In this way, the company secured its position as a pioneer in the market. What began as a small company for blast hole drilling had become a globally positioned specialist in the development and manufacture of innovative drilling systems for specialist foundation engineering.
The 1980s
In 1980, Klemm sold the first rock crusher KB 5000. This was followed by an entire series of models. The drilling rigs had reached type KR 501 by this time. For blast hole drilling in quarry operation, Klemm developed the KR 901 series with hydraulic hammer and KR 1001 with operator’s cab, compressor, drill string magazine, down-the-hole hammer and dust extraction. One highlight in 1981 was a diving bell equipped with a rotary drive for coring work. Using this system, exploration and blast hole drilling work was carried out off the coast of Newfoundland at a water depth of 160 m in order to install a telephone cable.
The first double-head systems with hydraulic hammer marked the launch of the KR 806 drilling rig. A new boom kinematics system now also allowed for low initial drilling points. By this time, hydraulic drilling rigs and the hydraulic hammer had taken on a dominating role in specialist foundation engineering and definitively replaced drilling rigs powered by compressed air. The manufacture of Kelly drilling rigs and accompanying drilling equipment with Kelly bars, auger and bucket tools also began in the early 80s. The first pile drilling rig GH 80 was delivered in 1983.
In 1980, Klemm sold the first rock crusher KB 5000. This was followed by an entire series of models. The drilling rigs had reached type KR 501 by this time. For blast hole drilling in quarry operation, Klemm developed the KR 901 series with hydraulic hammer and KR 1001 with operator’s cab, compressor, drill string magazine, down-the-hole hammer and dust extraction. One highlight in 1981 was a diving bell equipped with a rotary drive for coring work. Using this system, exploration and blast hole drilling work was carried out off the coast of Newfoundland at a water depth of 160 m in order to install a telephone cable.
The first double-head systems with hydraulic hammer marked the launch of the KR 806 drilling rig. A new boom kinematics system now also allowed for low initial drilling points. By this time, hydraulic drilling rigs and the hydraulic hammer had taken on a dominating role in specialist foundation engineering and definitively replaced drilling rigs powered by compressed air. The manufacture of Kelly drilling rigs and accompanying drilling equipment with Kelly bars, auger and bucket tools also began in the early 80s. The first pile drilling rig GH 80 was delivered in 1983.
Reunification – Construction boom and economic slump
In 1989, Klemm was acquired by the American Ingersoll-Rand Group. During the construction boom after Germany’s reunification, construction projects in Berlin above all lead to a high demand for Klemm’s technology and equipment. In 1990, Klemm began developing equipment for thermal probe drilling. The business in directional drilling systems and directional drill strings also gained steam. The successor to the GH pile drilling rigs was the lightweight universal pile drilling rig KB 3010. The undercarriage of this rig featured telescopic circular guides, the mast had a gear rack feed and the hoists were accommodated in the upper carriage. With this development, Klemm broke free from its dependence on excavator manufacturers. A difficult phase started in the mid-90s when the exceptional boom after reunification began to slow down. Klemm had to reduce its personnel, and international subsidiaries were closed down.
Klemm and Bauer
In the midst of this crisis, Bauer acquired Klemm in 1998 and restructured its business. Since then, Klemm has been the specialist within the BAUER Group for anchor drilling rigs and accessories. Part of this restructuring meant that Klemm stopped selling pile drilling rigs, and anchor drilling rigs were no longer sold in Schrobenhausen. This allowed the former competitors to pool their synergies.
One highlight: In 2004, Klemm received an order to deliver four large automated blast hole rigs to expand the Panama Canal. They were assembled and commissioned in Panama on a floating drilling platform. Later on, a Klemm drilling rig was also used at Ground Zero in New York.
In 2005, Klemm started developing a vibratory drive. The first linear vibratory drive was tested in site conditions in 2007. With the advent of even more powerful, heavy rotation-vibration drives, new drilling technologies and carrier devices have subsequently been developed. In 2007, Klemm delivered a KR 709-1C to a site in China where coal fires near the surface had to be extinguished. The equipment proved itself under extreme operation conditions at high temperatures. China ordered three additional machines.
Alternative drives
Nowadays, electric drive concepts and smart equipment functions are paving the way to the future. The battery-powered electric KR 806-3E is Klemm’s contribution to decarbonization. This equipment features proven technology from the KR 806-3GS – the same kinematics and an adapted form of the same powerful double-head drilling systems and hydraulic hammers, but as an electrohydraulic, emission-free variant. Compared to the diesel-hydraulic variant, there are no restrictions when it comes to power and application. Thanks to sophisticated technology and robust design, Klemm systems are used under nearly all conditions worldwide, for example in foundation and safeguarding work, when constructing traffic routes above and below ground, for dam sealing and to generate renewable energy.
KLEMM Bohrtechnik is a world-leading specialist for the development of exceptionally high-quality and powerful drilling rigs with total weights of up to 32 tonnes. The special feature: world-leading technologies which make KLEMM drills unrelenting.
As a market pioneer, KLEMM has had a decisive influence on the development of anchor drilling technology over the last five decades. This has lead to a technological advantage from which customers around the world benefit. This is because KLEMM offers a broad range of products and services (drilling devices, hydraulic hammers, rotary drives and drilling equipment) as well as individual solutions so that customers can carry out drilling tasks as best as possible with regard to time required, efficiency, reliability and safety.
KLEMM Bohrtechnik GmbH
Wintersohler Str. 5
57489 Drolshagen
Telefon: +49 (2761) 705-0
https://www.klemm.de
Marketing / PR
Telefon: +49 (2761) 705-101
E-Mail: jutta.clemens@klemm.de

