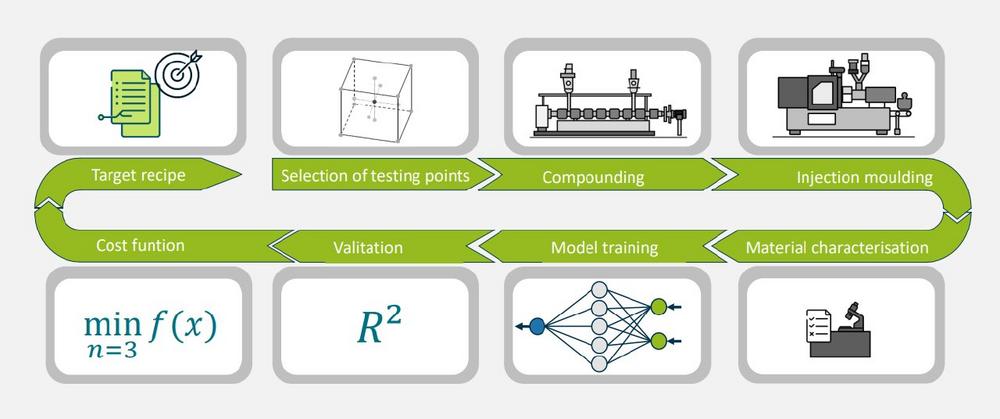
Sustainability – Put in extra shifts for the circular economy?
Through the consistent use of recyclate as a component of plastic products, it is possible to drastically reduce emissions (such as CO2 or the discharge of macroplastic and microplastic into waterways) and also to cut back on crude oil requirements. However, this sustainable multiple use of valuable raw materials is not yet achieved in all areas. In the packaging sector, for example, only around 11 % of the recyclate is currently being used for the renewed production of packaging. Various factors are making this difficult, for example:
- limited availability of material with high enough purity
- fluctuating properties
- limited acceptance of plastics recyclate
- inadequate economic attractiveness of using recyclate
Without strong partners and without innovative approaches, e.g. for material and process development, players in the plastics industry can only meet these challenges with a great deal of effort and at great cost. In various research projects, IKV is examining possibilities for holistically optimising the value chain of plastics recyclate.
Holistic AI-based optimisation of plastic packaging containing recyclate
One such project is the "AI application hub, plastic packaging", within which IKV is pursuing several objectives in a sub-project entitled "KIOptiPack: Holistic AI-based optimisation of plastic packaging containing recyclate". The primary target is the provision, validation and application transfer of practically tested, AI-supported moulding tools for successful product design and the production of plastic packaging with a high recyclate content and the required quality. This is supported by an AI-application and data room and the creation of a central network platform (which integrates, for example, the consumers and their attitude) for added value engineering.
A concrete example of an AI-supported tool is compound development (Figure 1). Instead of an "iterative approach" to the desired viscosity of the compound, use is made of existing data points and – where necessary – the characterisation of extreme points, while an AI model describes the space between the data points. This produces a much better imaging quality (R² = 0.97) than, for example, a regression analysis (R² = 0.60).
This illustrates how AI can, from easily documented (or already existing) data, create added value and save plastics converters a great deal of time and expense in finding the ideal viscosity of the compound, so that they do not have to work extra shifts.
Nevertheless, with recyclate material, not only processing properties such as the viscosity have to be taken into account, but also the performance properties. For example, suitable measures have to be taken to protect goods packed in plastic from contamination through undesirable substances potentially contained in the recyclate. This is where extra shifts of a different nature are deployed:
Plasma barriers protect packaged goods
A highly promising platform for barriers is a surface coating with plasma-based chemical gas phase deposition. The deposited barriers also serve to prevent migration of harmful materials from the recycled plastics to the packaged contents (Figure 2). However, the development of such plasma barriers has so far advanced relatively slowly because of the analytical work involved in determining the barrier performance. Through a newly developed process at IKV, which is based on innovative model contaminants and a new approach to incorporating them into the plastics, the barrier effect can in future be evaluated much faster. Accordingly, the optimisation of the plasma barriers will also take less time so that, thanks to this, product safety can be achieved with minimum emissions – and without having to fall back on poorly recyclable multi-layer plastic composite films.
Circular economy at the 32nd International Colloquium Plastics Technology
At the Colloquium, Session 2 (AI-based methods to boost PCR usage in plastics packagings), Session 8 (Plasma-based barrier coatings for sustainable packaging) and Session 13 (Challenges of PCR processing), will deal with the topic of the circular economy and the use of recyclate , each with a keynote paper from the industry, plus two scientific presentations from IKV.
At "IKV 360° – Research live”, the research assistants will demonstrate the topic at various stations.
IKV, the Institute of Plastics Processing at RWTH Aachen University, is Europe-wide the leading research and education institute engaged in the field of plastics processing enjoying outstanding reputation. More than 300 staff are employed in finding solutions to problems connected with processing, materials technology and part design in the plastics and rubber industries. IKV’s close contacts with industry and science, together with its outstanding facilities, enable cutting-edge research in plastics technology and ensure that students benefit from a comprehensive, practically oriented course of study. Plastics engineering graduates from IKV are thus sought-after experts in industry. In organisational terms, IKV is divided up into the four specialist departments of Injection Moulding, Extrusion and Rubber Technology, Part Design and Materials Technology, and Composites and Polyurethane Technology. The institute also takes in the Centre for Analysis and Testing of Plastics, and the Training and Further Education department. IKV is run by an Association of Sponsors, which currently has a membership of about 300 plastics companies from all over the world. Univ.-Prof. Dr.-Ing. Christian Hopmann is Head of the Institute and Managing Director of the Association of Sponsors. He also holds the Chair of Plastics Processing at the Faculty of Mechanical Engineering at RWTH Aachen University.
Institut für Kunststoffverarbeitung (IKV) in Industrie und Handwerk an der RWTH Aachen
Seffenter Weg 201
52074 Aachen
Telefon: +49 (241) 80-93806
Telefax: +49 (241) 80-92262
http://www.ikv-aachen.de
Leiterin Presse- und Öffentlichkeitsarbeit
Telefon: +49 241 80-93672
E-Mail: rebecca.hierlwimmer@ikv.rwth-aachen.de
Ansprechpartner für Fragen zum Thema Medizintechnik
Telefon: +49 241 80 98820
E-Mail: malte.schoen@ikv.rwth-aachen.de
