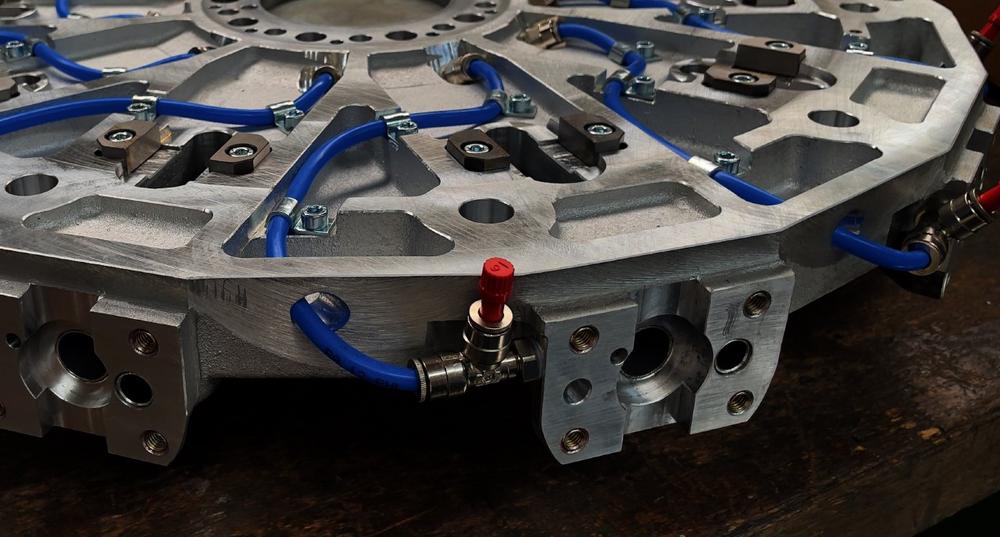
Tools for cocktails and coffee to go
"If we change workpieces on a machine several times a day and machine up to six different materials, we don’t want to change a new tool every time as well," states Marco Kneer, Managing Director of Kneer-Mechanik UG & Co. KG in Westerheim on the Swabian Alb. The small but excellent family business has specialised in the reliable and in-time production of single parts and the assembly of subassemblies for its customers. They often include manufacturers of special machines in the packaging or medical engineering sectors who require key production components to boost the productivity of their machines and systems. Marco Kneer has many companies that have been loyal regular customers since his father founded the company in 1980. But today, customers increasingly look for turnkey solutions, regardless of what reusable materials or which processes they are based on. "More or less an all-round carefree package where we are flexible in finding the best solutions," says Kneer.
One tool holder for many different milling processes
With batch sizes ranging from one unit to 50 units, it is certainly not a question of getting the final hours, minutes or metres of tool life out of the milling tool. What is much more important are universal tools that cater for many processes and materials. For many years, Tobias Breitling from Arno Werkzeuge has been providing support with the right products, but above all with a lot of technical advice. For example, Kneer likes to use innovative and universal milling tools from Arno Werkzeuge in its machine pool that machines parts that have travel paths up to 3 m. They also help with the machining of various materials, from grey cast iron to steels of grade 42CrMo or 16MNCr5 and stainless steels such as X8CrNiS18-9 or X120Mn12 for medical engineering and aluminium EN AW-1050A. Thanks to the new, innovative coating technology, they also score points by machining Inconel.
The patented Duomill milling system has become a highlight in production. With only one basic body, the tools can be used for corner and HFC milling operations on steel, stainless steel and aluminium. "With corner radii staring at 0.2 mm, something that is virtually unique," assures Breitling. "I find that very rarely," confirms Kneer. The fact that corner and HFC inserts are mounted in one insert seat is indeed unique. The entire circumference of the indexable inserts are precision-ground and polished. In addition, the nickel-plated and therefore durable basic holders achieve a high feed rate since they are equipped with four effective cutting edges per insert. After extensive testing, which Breitling was happy to support, the tool is now in use at Kneer. "This is the kind of support I look for from a tool partner. Those whose only aim is to sell us their catalogued goods are of no help to us."
Flexible and patented tools save handling time
This kind of universal tool has a positive impact on tool holder costs since it makes handling, storage and stocking easier. To obtain great flexibility in several machining tasks, it is crucial to be able to mount two different sizes of insert on the same tool holder. The universal tool range includes end milling cutters and screw-in milling cutters with diameters ranging from 25 to 42 mm, as well as shell-type milling cutters with diameters from 40 to 160 mm. Precision-manufactured and ground inserts with special geometries make for cost-effective solutions for reliable milling operations.
The tool holders have a differential pitch and this reduces vibrations, resulting in smooth surfaces. The system is also easy to handle. "This gives us exactly the flexibility we need for many production tasks as, for example, we don’t have to change a tool for an extra solid carbide milling cutter for trimming," says Kneer enthusiastically. Breitling confirms this: "This is precisely the strength of the Duomill. If you don’t want to choose between "fast" and "fine", it’s best to go for our FD milling system." Four effective cutting edges at 90° offer maximum efficiency for corner and HFC milling operations.
Arno Werkzeuge accompanies tests and field trials
Since Kneer was not fully satisfied with competitor face milling products, Breitling was taken on board after a series of tests and a field trial at a time when the company was due for a replacement investment. The new face milling system takes account of Kneer’s requirements that, when he needs tools "that run well and cut gently, especially on machines that do not require as many spindles." This is exactly the capabilities of the new, stable FT face milling system 09. It is basically very stable and features a smooth cut and very quiet running. This provides the spindle with maximum protection and is the result of a large flat face on the holders, a positive rake angle despite the negative mounting position and the differential pitch of the flutes. Marco Kneer also likes the fact that a higher feed rate is possible, although it is not the decisive factor for him.
More teeth and smaller double-sided indexable inserts
The new FT 09 milling system consists of two variants of stable tool holders covering a diameter range of 20 to 125 millimetres. It is equipped with eight flutes and matching smaller indexable inserts. "Since we achieve a narrower pitch despite the small diameter, we can now place more teeth on the tool," Staiger explains. This means we can fit up to nine indexable inserts, where only six were possible in the past. "So we have a significant improvement in the production of certain parts on smaller machines," Kneer confirms.
The fact that Arno Werkzeuge always thinks in terms of the application is also demonstrated by an innovative, three-fluted drill with through-tool cooling and three-chamfer guide. This routes cooling lubricant through the channels directly to each cutting edge. It ensures stable guidance in the bore and at the bore exit. The drill aligns better, produces exact roundness and keeps tolerances better. The design also allows feed rates up to 33% higher and faster machining speeds. This results in good chip flow at reduced cutting pressure. Chips have controlled chip breakage and much less burr form in through-holes.
Important skills for paper cups and operating theatre tables
For example, Kneer Mechanik assemblies ensure that operating tables are adjustable without any play or jerk. Similarly, rotary indexing units are produced for packaging machines which produce millions of coffee cups for fast food chains. A unique feature is a special support unit with movable fingers. Without its help it would be impossible to produce a disposable cup base for ready-mixed cocktail drinks at the required speed and precision. But this tricky and clever solution from Kneer Mechanik provides enough subject matter for another article.
Customer proximity and development power: Emil Arnold set up ARNO Werkzeuge Karl-Heinz Arnold GmbH in 1941 as an innovative tool manufacturer and the company is now in the third and fourth generations of owner management. The company has a high manufacturing depth, in-house development competence and a global sales organisation. It produces highly modern, high-performance tools which are used world-wide in production with fixed headstock machining, Swiss type machining, parting, grooving, turning, drilling and milling. One of the company specialities is ground high-positive indexable inserts for complex manufacturing operations. Here, ARNO offers the largest portfolio in the world.
Customised tool solutions, which later become highly coveted standards, are developed in close collaboration with our customers, taking their requirements into consideration. The tradition-based company ensures customer proximity by a work force of over 200 employees at its head offices in Ostfildern and its numerous sales offices all over the world. Most recently, ARNO achieved a turnover of around 54 million euros, almost back to the pre-crisis level.
((Company info KNEER Mechanik))
Swabian family business with the skill to find the right solution competence: As a modern family business, Kneer-Mechanik UG & Co KG, founded in 1980 by Hermann Kneer, specialises in the machining of single and small batches. To provide customers with the best possible support in implementing individual products, the experts provide advice on developing and implementing prototypes and small batches. With many years of experience in all areas of production in a wide variety of materials and finishing processes, the company always creates functional solutions for individual tasks.
Kneer-Mechanik has been a skilled partner for special machine manufacturers for many years when it comes to implementing complete solutions, starting with production and assembly right through to the finished product. The aim is to fulfil the individual requirements of demanding customers in the shortest possible time and with the best possible quality. A modern machine pool with a wide range of machines is available for this purpose. Highly motivated employees with many years of experience are an essential factor ensuring success in the implementation of the highest requirements.
ARNO Werkzeuge
Karlsbader Straße 4
73760 Ostfildern
Telefon: +49 (711) 34802-0
Telefax: +49 (711) 34802-130
http://www.arno.de
Unternehmungskommunikation
Telefon: +49 (711) 34802-0
E-Mail: kknapp@arno.de