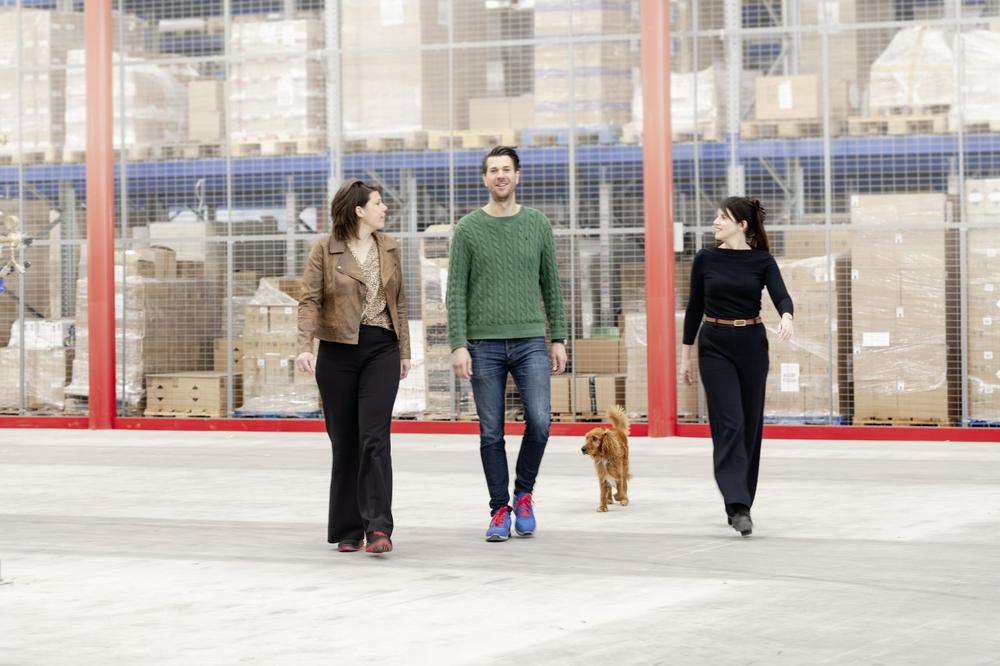
From greeting cards to gifts: Greetz unveils new storage technology from SSI Schaefer
In 2004, Greetz launched a service that was new to the Netherlands: the ability to create and send greeting cards online to people celebrating a birthday, wedding, birth, anniversary or other joyous occasion. Today, tens of thousands of cards are printed on demand every day and land in mailboxes the very next day. "People know us mainly for the cards, but now we do much more than that. On a normal day, we send out thousands of gifts. At peak times, it can be four or five times as many," says Sander Jelgerhuis Swildens, Operations Manager at Greetz.
Customers can choose from a variety of gifts. "We started with wine, flowers, soft toys and chocolates. Over the years, the product portfolio has continued to expand and we now also offer beauty products and home accessories, for example. The warehouse now contains 1,200 products," explains Sander Jelgerhuis Swildens. He is supported by Innovation Manager Sabine Huijskes: "In practice, the variety is even greater because we offer the possibility of personalizing products. Think of a bottle of wine or a bar of chocolate with your own text, or a balloon with the birthday girl‘ or boy’s photo."
Rising sales curve
During the Corona pandemic, it became apparent how valuable it can be to send a card and gift with a personalized message. In 2021, Greetz experienced an all-time peak year with sales of 72 million euros, almost five times as much as in 2008. "It’s logical that sales have dropped slightly now that the pandemic is over and people can get together again on birthdays," argues Sander Jelgerhuis Swildens. "But when we filter out the Corona spike, sales continue to show an upward trend. We expect to continue to grow steadily in the future."
The previous warehouse in Amsterdam did not offer enough space for this growth. "We were forced to move out of the building. It consisted of several adjacent small rooms connected by a corridor. As we expanded the product portfolio over the years, it was no longer possible to work efficiently. For example, some of the operations took place on the second floor. As a result, employees and products had to be taken up and down the elevator dozens of times a day," says Sander Jelgerhuis Swildens.
Drastically shorter running times
The search for a new warehouse ended in an existing 8,000-square-meter building in Almere, Netherlands. There, Greetz created a sophisticated and particularly efficient system with the help of SSI Schaefer. Sabine Huijskes: "We first mapped all processes. How do the employees and goods move through the operation? And what is the most logical layout? We wrote our ideas on Post-its and stuck them on a large sheet. Of these, 95 percent were put into practice, which above all drastically reduced the running times between the various departments and machines."
SSI Schäfer had also already supplied the racks for the Amsterdam warehouse and was therefore no stranger to Greetz. Nevertheless, Sander Jelgerhuis Swildens and Sabine Huijskes decided to launch a new tender for the new warehouse layout, after which SSI Schaefer was again awarded the contract. "Of course, this has to do with pricing, the quality of the storage systems and the way the bid was worked out. But the most important difference is SSI Schaefer’s ability to think along with us about the layout of the warehouse. This involved, for example, the arrangement of the shelving or the height and load capacity of the pallet racking systems. The fact that we already had good experience with products from SSI Schaefer products did the rest."
Shelves with storage compartments
Greetz now has a total of 2,000 pallet storage spaces. These are mainly for the packaging material of the best-selling products and bulk goods. The majority of the product portfolio is stored directly on arrival in the racks, which consist of 244 shelving bays. "The vast majority of the gift items are in blue bins that we brought from Amsterdam and that were also supplied by SSI Schaefer. In these bins, we can store all the products neatly and securely, without any empty boxes getting in the way. The bins have an opening at the front so that the pickers can easily grab the products," says Sabine Huijskes.
Part of the shelving is in the cold room, where some chocolate products and the fruit for the fruit boxes are stored. Another portion is used for picking balloons, for which Greetz has set up a separate process. "We pick all gift items in batches, but with balloons it is more efficient to work according to the one-piece flow principle," Sabine Huijskes explains. "This means that each balloon is picked and processed in one step until it is inflated in a box. This way we can better control the process and guarantee that all balloons are ready for transport in time."
Professional organisation
SSI Schaefer not only supplied shelving, but also a handrail lock and a mezzanine. The railing sluice was installed to safely transport the goods to the mezzanine floor. The access stairs replaced an old, steep staircase that no longer met safety requirements. By creating a staircase with an extra large landing, the exit below the staircase can also be used without problems.
Greetz is satisfied with the progress of the project. The assembly of the racks went smoothly. "The cooperation with the employees of SSI Schäfer is simply very pleasant. We can always call if we have a question and get an answer quickly," says Sabine Huijskes. Sander Jelgerhuis Swildens adds: "It is good that SSI Schäfer is a large company with decades of experience. In today’s world, the availability of materials is sometimes a challenge, putting pressure on delivery times. In this case, it depends on how this is communicated and how any problems are solved. And we are very satisfied with that."
20% higher productivity
Thanks in part to the efficient warehouse layout, the productivity of the 50 employees in the order processing area has been increased by around 20%. The number of cartons that can be processed per person per hour is significantly higher in the new warehouse. "This is largely due to the new warehouse concept, but also to the improved overview of the processes," says Sander Jelgerhuis Swildens. "We used to finish our order processing for next-day delivery at half past midnight with a lot of effort. Today, we can extend the order entry of those for customers from 10 p.m. to 10:30 p.m. and finish orders before midnight. That’s another 30 minutes of additional service we can offer our customers."
Meanwhile, Greetz is already thinking about new innovations. For example, the company has moved to a new platform that offers more options for data analysis and consumer advice. In addition, Sabine Huijskes continues to focus on optimizing processes. Sabine Huijskes: "We never get up without ideas. We are constantly working on improving efficiency, quality and the product portfolio. Together with the sales team, we want to develop a new strategy based on all these ideas. In doing so, we constantly ask ourselves how we can remain individual and attractive to our customers."
The SSI Schaefer Group is a leading global solution provider for all areas of intralogistics. With innovative technologies and software, the company empowers customers to increase the efficiency and sustainability of their storage, picking, and transport processes. SSI Schaefer offers small and medium-sized enterprises, as well as large companies, cost-effective material handling solutions with industry expertise from a single source. From fully automated warehouses with tailored service and maintenance packages, to robotics and automated guided vehicles, to manual and semi-automatic systems such as workstations, racks, and containers, the company offers a complete solution. SSI Schaefer has also become one of the largest vendors of software for internal material flow. Its comprehensive software portfolio handles everything from warehouse management to material flow control. With state-of-the-art real-time analysis, intelligent data processing and optimization algorithms, it offers every possible option for integrated, sustainable resource management.
SSI Schaefer employs around 10,000 people at its international headquarters in Neunkirchen (Germany) and globally in more than 70 operating companies and seven production facilities on six continents.
For years, the SSI Schaefer Group has relied on trusted partners, including the robotics specialists at RO-BER and the SAP specialists at SWAN, as well as DS Automotion, a company with expertise in robotics and AGVs that has been a full member of the SSI Schaefer Group since March 1, 2023.
SSI SCHÄFER
Fritz-Schäfer-Strasse 20
57290 Neunkirchen / Siegerland
Telefon: +49 (2735) 70-1
Telefax: +49 (2735) 70-396
http://www.ssi-schaefer.de
Junior Project Manager CR & PR | Global Marketing
Telefon: +49 (2735) 70-9683
Fax: +49 (2735) 70-382
E-Mail: Annika.Nolte@ssi-schaefer.com
