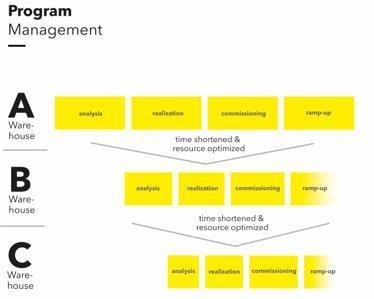
Uniform Warehouse Management System: Successful Global Implementation Through Program Management
Different locations with different warehouse technologies, assortments, and processes as well as the staggered implementation of a WMS in existing and new installations – these are all challenges that must be met in today’s volatile world.
Project management versus program management
While software projects are usually focused on one location or purpose with a predefined duration and the known essential project criteria (complex, novel, time-limited, measurable goals, limited resources, predefined budget, teamwork, and one-off), software program management is much more geared towards long-term support – often in relation to an international corporate customer. Work here involves coordinating the implementation and support of numerous sites, for which several projects are ongoing in parallel. This homogeneous approach across individual projects ensures that resources are used efficiently and costs are reduced over the course of time.
"The economies of scale from effective program management ensure a significant reduction in costs over time and enable optimum prioritization of individual projects," explains Gregor Girstmayr, Head of WAMAS Enterprise WMS at SSI Schaefer.
How it works
Within the framework of program management, strategic and operational goals are developed together with the respective customer by a dedicated program team and subsequently implemented through targeted individual projects. The program team assumes the overarching control function, which enables the identification of any conflicting targets of individual subprojects and the initiation of countermeasures.
Joint synergies can be realized through the formation of a program team both at SSI Schaefer and within the customer organization. The balance between individual expectations and the objectives at project level is controlled and maintained by the superordinate program level – centralization at the highest point. This enables customers to better estimate the lifecycle costs of their investment in WAMAS intralogistics software and to master the upcoming technological, legal, and organizational requirements together with SSI Schaefer.
The added value
Economies of scale become greater as the number of warehouse locations increases; an advantage that is realized even when intralogistics requirements differ between sites. Given that it is necessary to devise the core functionalities, customer-specific requirements, and processes for the first warehouse location, benefits can be drawn from this further down the line, thereby correspondingly reducing the development costs for customer-specific adaptations over time. Furthermore, repeated use of the same project teams on behalf of the software program management also means that cost-saving effects can be achieved in the software roll-out phases.
The software team at SSI Schaefer possesses broad implementation skills, which allow team members to support each partner in the intralogistics environment on a long term basis and face future technological challenges together. Renowned international groups already count among SSI Schaefer’s customers and – thanks also to efficient program management – are looking with confidence to a common future in the implementation of homogeneous warehouse management software systems at locations around the world.
About the author:
Georg Kowaschitz, team leader in the field of project management software at SSI Schaefer, is a business administration specialist and IPMA-certified project manager with over 10 years of professional experience in software project & program management, digital transformation, and organizational development. Since 2018, he has been working at SSI Schaefer in software project/program realization in various roles at the Friesach site. His team provides support to several international corporations in the implementation of WAMAS Enterprise WMS.
The SSI Schaefer Group is a leading global solution provider for all areas of intralogistics. With innovative technologies and software, the company empowers customers to increase the efficiency and sustainability of their storage, picking, and transport processes. SSI Schaefer offers small and medium-sized enterprises, as well as large companies, cost-effective material handling solutions with industry expertise from a single source. From fully automated warehouses with tailored service and maintenance packages, to robotics and automated guided vehicles, to manual and semi-automatic systems such as workstations, racks, and containers, the company offers a complete solution. SSI Schaefer has also become one of the largest vendors of software for internal material flow. Its comprehensive software portfolio handles everything from warehouse management to material flow control. With state-of-the-art real-time analysis, intelligent data processing and optimization algorithms, it offers every possible option for integrated, sustainable resource management.
SSI Schaefer employs around 10,000 people at its international headquarters in Neunkirchen (Germany) and globally in more than 70 operating companies and seven production facilities on six continents.
For years, the SSI Schaefer Group has relied on trusted partners, including the robotics specialists at RO-BER and the SAP specialists at SWAN, as well as DS Automotion, a company with expertise in robotics and AGVs that has been a full member of the SSI Schaefer Group since March 1, 2023.
SSI SCHÄFER
Fritz-Schäfer-Strasse 20
57290 Neunkirchen / Siegerland
Telefon: +49 (2735) 70-1
Telefax: +49 (2735) 70-396
http://www.ssi-schaefer.de
Junior Project Manager CR & PR | Global Marketing
Telefon: +49 (2735) 70-9683
Fax: +49 (2735) 70-382
E-Mail: Annika.Nolte@ssi-schaefer.com
Marketing & Kommunikation
Telefon: +49 (2735) 70-252
Fax: +49 (2735) 70-382
E-Mail: melanie.kaempf@ssi-schaefer.de
