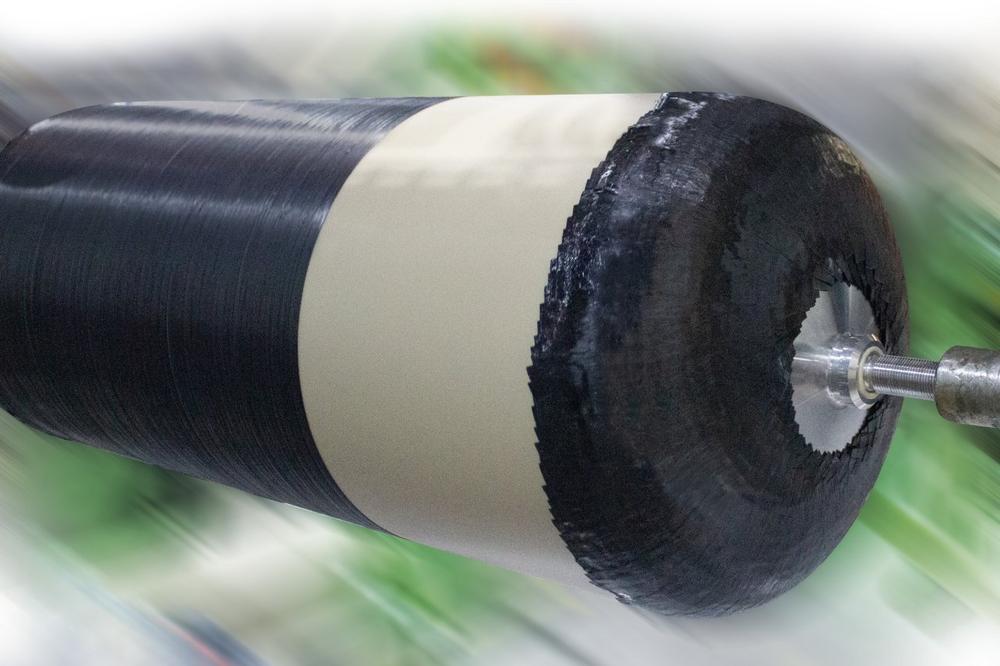
Pioneering a novel approach for H2 tank production: Cevotec, Roth and CIKONI achieve 15% mass reduction of composite vessel
Cevotec has developed an industrial solution to reduce the amount of carbon fiber needed for a composite tank by locally reinforcing the tank’s dome areas. Fiber Patch Placement (FPP) is the first technology to lay-up dome reinforcements directly onto the liner using a fully automated, industrial process which can be combined with any existing wet or towpreg winding equipment.
This approach reduces net fiber usage by approx. 15%, depending on the vessel characteristics, which translates into considerable weight and cost savings while maintaining equivalent mechanical properties. Due to the material reduction, the reinforced tanks can also feature more storage volume in the same build space and have an improved CO2 footprint.
To underpin Cevotec’s approach, an optimized full-scale demonstrator has been successfully developed in collaboration with the project partners. The primary goal was to optimize the fiber lay-up to reduce weight, cost and production time. The project comprised all aspects from laminate design, simulation and optimization driven by CIKONI, to the actual production and testing of the reinforced tanks. Additionally, the effectiveness of FPP dome reinforcements within an industrial production environment has been evaluated. With the successful completion of the third design iteration, the project partners have achieved the intended results.
“The 300 bar type IV tank has a thinner composite overwrap with a lower number of layers to be replaced by dome reinforcements, which is a challenging set-up compared to 700-bar-class vessels”, explains Dr. Florian Lenz, Technical Director of Cevotec. “To achieve the optimal material saving design, different laminate iterations were pursued. In a third iteration, we, together with the project partners, successfully achieved a burst safety factor of 108% and material savings of 15%.” Due to the material savings, the CO2 footprint is significantly reduced and the storage efficiency of the test vessel can be increased to 6.1%, which represents an improvement of 17% compared to the reference vessel.
Cevotec is currently assembling a dedicated FPP production system for dome reinforcements in their lab in Unterhaching near Munich. The SAMBA Pro PV Lab system will be available for commercial prototyping and development with customers in spring 2024. Thorsten Groene, CEO and Co-Founder at Cevotec, underlines the strategic relevance of industrial dome reinforcements: “The expected fiber demand for H2 tanks will outgrow available fiber supply in the next 5-10 years. Technologies like FPP that enable resource savings are strategically important for global competitiveness.” Interested parties can meet the teams of Cevotec, CIKONI and Roth at JEC World, the leading international composites show in Paris, March 5-7.
About Cevotec:
Munich-based automation specialist Cevotec offers one of the world’s most advanced production systems for complex fiber composites. At the intersection of composites, mechanical engineering and software, Cevotec develops production systems and software based on Fiber Patch Placement (FPP) technology: SAMBA and ARTIST STUDIO. The production systems enable the automated lay-up of carbon fiber, glass fibers, adhesive films and other technical fibers on complex 3D geometries. Manufacturers use FPP technology to produce e.g. multi-material aerostructures, composite pressure vessel reinforcements, and other high-performance components in a quality-controlled, fully automated process, which enables them to realize cost & cycle time savings of 20%-60% when switching from conventional processes to Fiber Patch Placement.
Contact:
Cevotec GmbH
Biberger Str. 93
82008 Unterhaching
Phone: +49 89 2314 1650
Email: advantages@cevotec.com
www.cevotec.com
About CIKONI:
CIKONI is one of Germany’s leading providers of engineering services related to composite materials. Having both internal product and process development capacities, CIKONI bridges the domains of structural performance and automation to develop new classes of composite material products and manufacturing technologies for customers. With many years of development experience in the field of CNG and H2 composite pressure vessels, CIKONI provides solutions for advanced simulation, innovative design and quality inspection.
Contact:
CIKONI GmbH
Zettachring 12A
70567 Stuttgart
Phone: +49 711 26375600
Email: info@cikoni.com
www.cikoni.com
About Roth:
Roth Composite Machinery (Roth) designs and manufactures specialized machinery for various industries, including Brushes & Brooms, Pleating & Coating, and Filament Winding & Prepreg. Roth is known for their high-performance mechanical engineering and tailor-made customer-specific machine designs, perfectly matching application and end-product needs. In the world market leading business unit Filament Winding & Prepreg, Roth serves customers by suppling competitiveness increasing automation solutions by optimizing production processes with enhanced productivity, precision, and reliability. Their machines are used e.g. in the aerospace industry but especially by manufacturers of high-pressure tanks for compressed hydrogen and natural gas, supporting sustainable mobility concepts.
Contact:
Roth Composite Machinery GmbH
Bauhofstr. 2
35239 Steffenberg
Phone: +49 (6464) 9150-0
Email: info@roth-composite-machinery.com
www.roth-composite-machinery.com
Munich-based automation specialist Cevotec offers one of the world’s most advanced production systems for complex fiber composites. At the intersection of composites, mechanical engineering and software, Cevotec develops production systems and software based on Fiber Patch Placement (FPP) technology: SAMBA and ARTIST STUDIO. The production systems enable the automated lay-up of carbon fiber, glass fibers, adhesive films and other technical fibers on complex 3D geometries. Manufacturers use FPP technology to produce e.g. multi-material aerostructures, composite pressure vessel reinforcements, and other high-performance components in a quality-controlled, fully automated process, which enables them to realize cost & cycle time savings of 20%-60% when switching from conventional processes to Fiber Patch Placement.
Further Information: www.cevotec.com
Cevotec GmbH
Biberger Str. 93
82008 Unterhaching bei München
Telefon: +49 (89) 2314165-0
Telefax: +49 (89) 2314165-99
http://www.cevotec.com/
Managing Director
Telefon: +49 (89) 23141650
Fax: +49 (89) 231416599
E-Mail: communication@cevotec.com

