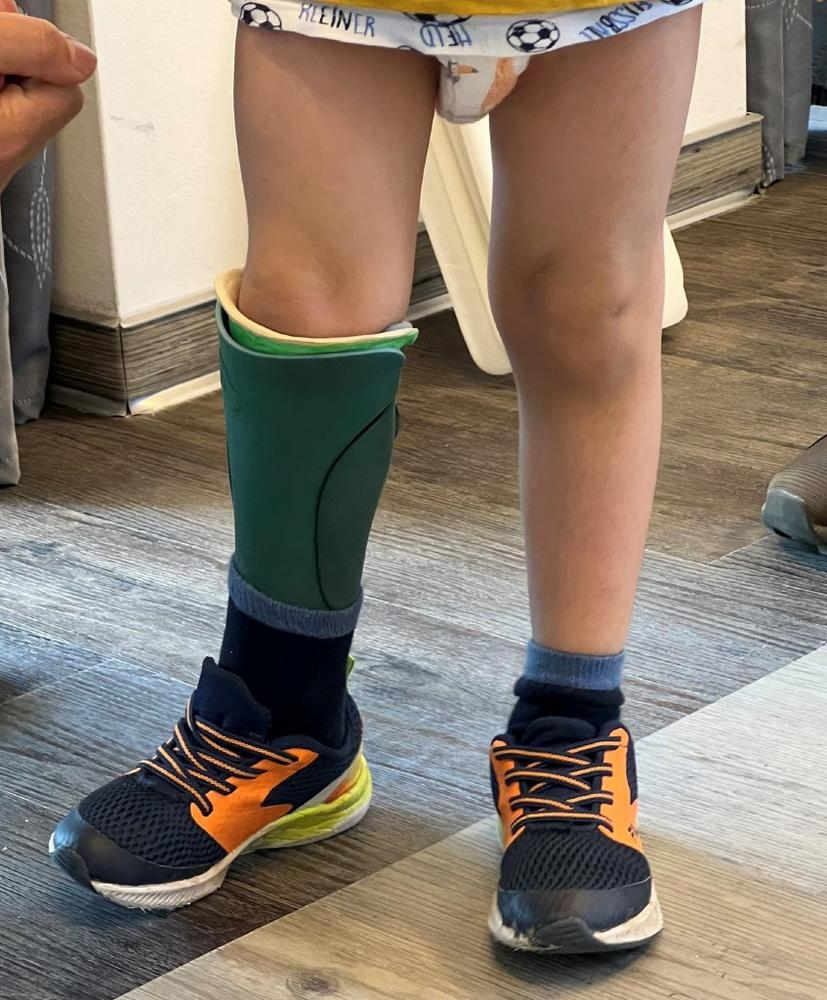
Prosthetist from Rostock
The specialists at LiEBAU orthopädietechnik GmbH commissioned priomold GmbH to produce an innovative 3D prosthesis for a brave young boy. Weighing only 90 grams, the prosthesis is the lightest of its kind that LiEBAU has ever produced.
This small 3D printed prosthesis replaces the boy’s foot, which unfortunately had to be removed. We are proud to have enabled the first steps with our prosthesis. It fills us with joy and satisfaction to see him start his new life. We wish him all the best and promise to accompany and support him on his way through life and above all to always give him ‚legs‘," says Karl Lippert from LiEBAU orthopädietechnik GmbH.
The 3D prosthesis for toddlers was created using state-of-the-art technology and skilled craftsmanship. The combination of advanced scanning technology, selective laser sintering (SLS 3D printing), HTV silicones, and a BOA closure allows the little boy to be mobile and actively participate in social life. Of particular note is the environmentally friendly manufacturing process that produces zero waste. The PA11 material used is also based on renewable resources, making the prosthesis a sustainable and environmentally friendly solution. PA11 is also very suitable for prosthetic manufacturing because it does not splinter when the material breaks.
SLS 3D printing can also be used to quickly and cost-effectively produce replacements if the prosthesis is damaged or if a larger prosthesis is required.
"The progress and participation in life made possible by such innovations is inspiring to all of us. We hope the little patient has a lot of fun with it," says Felix Parsch, Head of Additive Manufacturing at priomold GmbH.
The successful collaboration between LiEBAU orthopädietechnik GmbH and priomold GmbH shows how innovative 3D printing technology can improve people’s quality of life. This step marks a milestone in the development of prostheses for children and promises a promising future for the cooperation between medical care and state-of-the-art technology.
The fairly young company, founded by Thomas Schönbucher and Moritz Zumdick in 2015, specializes in the rapid delivery of plastic injection molded parts, offers mold construction (over 500 new molds per year) for prototypes and small series, as well as engineering support in the field of plastics. In the meantime, the company has grown to over 75 employees and is continuing to expand. What essentially sets priomold apart is its short delivery times for molds, injection molded parts, and additively manufactured components. The fastest project was completed in two working days; on average, a new mold is ready within two to three weeks. Multiple awards as Growth Champion and TOP100 for Innovation 2022 are the confirmation of priomold’s development.
priomold GmbH
Gewerbestraße 6
75328 Schömberg
Telefon: +49 (7084) 9769690
http://www.priomold.de
Marketingmanagerin
Telefon: 07084976969250
E-Mail: e.wilhelm@priomold.de

