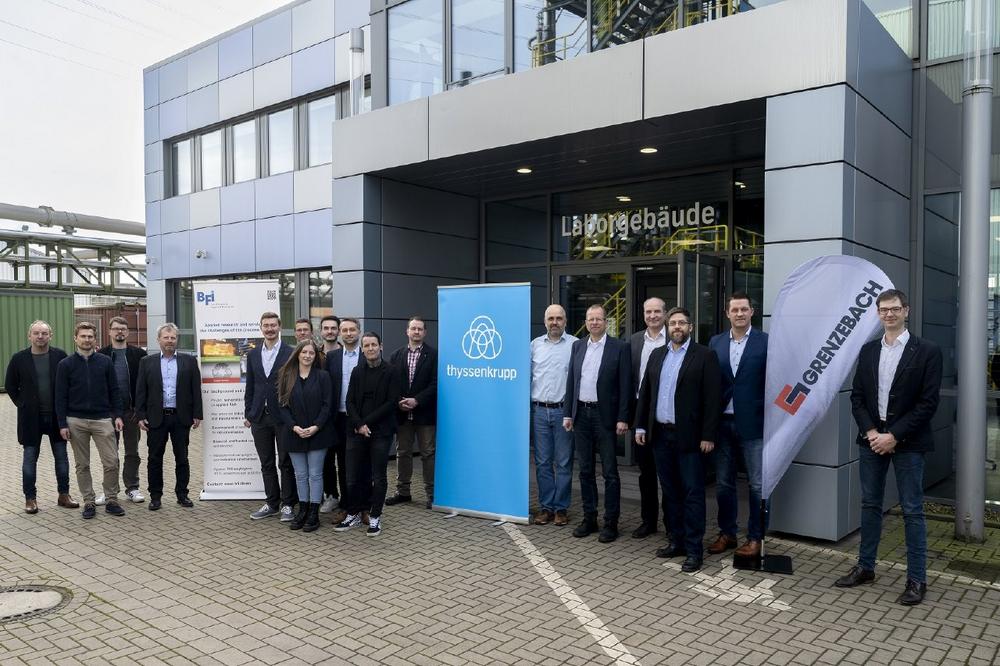
Research module for the electric hot metal of the future: thyssenkrupp Steel awards contract for melter test facility
- thyssenkrupp Steel commissions Grenzebach Maschinenbau to build the plant in Duisburg
- The project will take its place in thyssenkrupp Steel’s carbon-neutral transformation strategy
- Research into electric hot metal from hydrogen-based direct reduction
- The VDEh Institute for Applied Research (BFI) is responsible for the scientific management
thyssenkrupp Steel has commissioned Grenzebach Maschinenbau GmbH with the engineering, construction, and commissioning of a DRI melter test facility, including the associated auxiliary units, at the Duisburg site. The melter, funded by the Ministry of Economic Affairs, Industry, Climate Action and Energy of the State of North Rhine-Westphalia (MWIKE), is part of the research focus on the carbon-neutral transformation strategy at the thyssenkrupp Steel site in Duisburg.
The project, led by the VDEh Institute for Applied Research (BFI), aims to show how sponge iron from direct reduction plants can be liquefied in an innovative melter and then processed further into hot metal. The contract is worth around 7.5 million euros, with MWIKE covering 65% and thyssenkrupp Steel 35% of the total cost of the project.
Research focus on CO2 reduction in hot metal production and cement manufacturing
The first trial campaigns to test different feedstocks such as direct reduced iron (DRI), alternative carbonaceous products and recycled materials for hot metal production are scheduled to start at the beginning of 2026. The demonstration-scale melter with a capacity of 100 kg/h of directly reduced iron is adapted to the DRI test facility. At Europe’s largest steel location, the two units will collaborate to focus research on hydrogen-based direct reduction technology. In addition to investigations into CO2 reduction and the quality of the hot metal produced, a further objective of the project is to condition the slag from the melter so that it can be used as a basic material for cement production, comparable to the current use of blast furnace slag in conventional hot metal production. The cement industry is a difficult one to decarbonize, but this concept will also enable the CO2 emissions from the industry to be sustainably reduced.
"Hydrogen-based direct reduction in combination with melters is an innovative approach that thyssenkrupp Steel is implementing on a large industrial scale for the first time. That’s why it is essential to apply and learn about the new technologies in practice on the way there," comments Chief Technology Officer Dr. Arnd Köfler. "The experimental melter and the direct reduction test facility are the heart of our research into carbon-neutral steel production of the future. They will enable us to use different charge materials flexibly, and to find precise answers to the fundamental technological questions surrounding the transformation of steelmaking."
thyssenkrupp Steel is strengthening its innovative potential with a new melter test facility
With the melter test facility, thyssenkrupp Steel is closing the gap in pilot trialing of the entire production process from raw material to rolled steel strip. The process steps from steel production, from rolling through to surface refinement are already being simulated on a reduced scale in pilot plants. With this approach, new technologies and concepts can thus be tested realistically, with a focus on customer needs. Pilot-plant-scale development not only conserves resources and reduces development costs, it also prevents disruptions in operational production facilities. The demonstration scale therefore also makes it possible to learn from mistakes, and adjust the parameters and operating points. It is also planned for new input materials to be trialed. This will make it possible to identify optimized solutions along the production route and then, once the large direct reduction plant being built in Duisburg is commissioned, integrate them seamlessly into the existing iron and steel plant.
As a pioneer in climate transformation, thyssenkrupp Steel has set itself the goal of reducing its CO2 emissions by more than 30% annually as early as 2030. By 2045 at the latest, the steel production is planned to be completely carbon-neutral. Thanks to funding from the national and regional governments for thyssenkrupp Steel’s tkH2Steel® project at the Duisburg site, the pioneering transformation is becoming reality: the production of premium steel with green electricity and hydrogen-based direct reduction technology. The starting point for the transformation will be a first direct reduction plant with innovative melting units. As a major consumer of green electricity and hydrogen, thyssenkrupp Steel is also a pioneer of the green energy infrastructure of the future.
VDEh-Betriebsforschungsinstitut, based in Düsseldorf, is one of Europe’s leading institutes for application-oriented research and development in the process industry. Increasing demands on product quality, production costs, CO2 emissions and plant utilization are posing new challenges for the steel industry. The BFI offers tailored innovations along the entire process chain of steel production, from the input materials down to the end product. Its research activities include CO2 reduction and energy efficiency, process and process chain optimization, circular economy, Industry 4.0 and measurement technology.
The scientists at the BFI are supporting the transformation of the steelmaking in close cooperation with the industry and policymakers. This includes not only activities to investigate the technologies through experimentation and simulation as part of publicly funded research projects, but also collaboration in initiatives such as IN4climate.NRW or scientific work within SCI4climate.NRW.
thyssenkrupp Steel is one of the leading suppliers of high-grade flat steel and stands for innovations in steel and high-quality products for innovative and demanding applications. Steel has a good 26,000 employees and produces about 11 million metric tons of crude steel per year – making it Germany’s largest flat steel manufacturer. Its capabilities range from custom material solutions to material-related services.
thyssenkrupp Steel Europe AG
Kaiser-Wilhelm-Str. 100
47166 Duisburg
Telefon: +49 (203) 52-0
Telefax: +49 (203) 52-25102
http://www.thyssenkrupp-steel-europe.com
Public-/Media Relations
Telefon: +49 (203) 52-44916
E-Mail: roswitha.becker@thyssenkrupp.com

