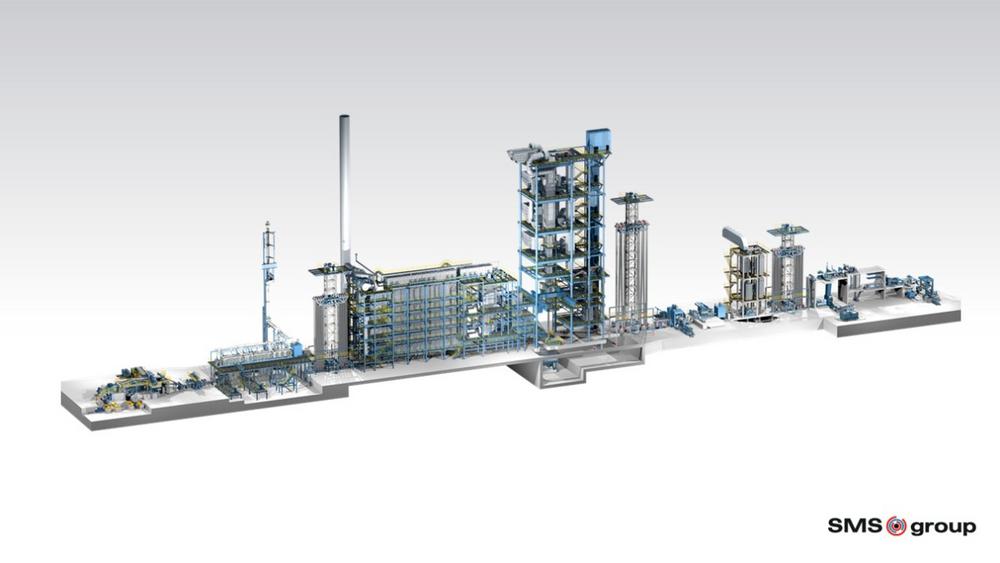
Angang Guangzhou Automotive Steel orders second hot-dip galvanizing line from SMS group
The new No. 2 hot dip galvanizing is intended to produce exposed automotive panels that demand optimal surface quality. All key technological components covering the mechanical, thermal, process and E&A equipment will be designed and supplied by entities operating within SMS.
The technological centerpiece of the new No. 2 hot dip galvanizing line is the all-radiant-tube annealing furnace from DREVER International together with the air knife system from DUMA-BANDZINK, both companies of the SMS group. These systems ensure the right material properties within tight tolerances as well as the flawless surface condition that automotive end-users require for exposed qualities. The terminal and process equipment delivered by SMS’s Center of Competence for Processing Lines guarantees stable production and efficient maintenance. A high degree of modularization is incorporated in the chosen design. The electrical and automation systems from SMS bring the individual units together to form one smart and homogeneous facility.
Benefits of this technology:
This technology ensures stable production and optimized surface quality. SMS’s cleaning section removes surface contaminations efficiently and thoroughly thanks to a combination of mechanical, hydrodynamic and chemical process steps. The cleanliness of the strip surface is decisive for the final achievable product quality. The all-radiant-tube furnace from DREVER International is designed to strictly separate the furnace atmosphere, the combustion process, and the ambient environment, in order to avoid any deterioration in the surface condition during heat treatment. DUMA-BANDZINK’s air knife systems have a long history in providing optimal quality for galvanized surfaces. SMS’s inline skin pass mill is designed to finish the galvanized surface with a controlled surface imprint. In addition, the unit improves the strip shape to allow for easy stamping at the end users’ facilities in the automotive industry.
The scope of delivery of SMS includes the engineering, procurement, and delivery of the complete range of equipment required for the new No. 2 hot dip galvanizing line. Moreover, technical assistance is included during the erection and commissioning phases.
Angang Iron & Steel Co. Ltd. and SMS share a long and prosperous history. In terms of processing lines, SMS put the first hot dip galvanizing line – No.1 – successfully into operation in 2013. Not only that, two continuous annealing lines were jointly put into service at Angang’s main site in Anshan.
The new order for hot dip galvanizing line No. 2 at Angang Guangzhou Automotive Steel Co., Ltd. showcases SMS’s capability, bolstered by its global presence, to deliver a high-class installation as a full-line EP project to the highly competitive Chinese market.
SMS group is renowned worldwide for its future-oriented technologies and outstanding service for the metals industry. The company applies its 150 years of experience and its digital know-how to provide the industry continuously with innovative products and processes – even beyond its core business – and generates worldwide sales of around 3.1 billion euros. SMS is the right partner for challenging projects, and supports its customers throughout the lifecycle of their plants, enabling profitable and resource-efficient value creation chains. Paving the way for a carbon-neutral and sustainable metals industry is the company’s stated goal. As a global player with German roots, SMS takes responsibility for its 14,400 employees.
SMS group GmbH
Eduard-Schloemann-Straße 4
40237 Düsseldorf
Telefon: +49 (211) 881-0
Telefax: +49 (211) 881-4902
http://www.sms-group.com
Fachpresse
Telefon: +49 (211) 881-4449
Fax: +49 (211) 881-774449
E-Mail: thilo.sagermann@sms-group.com

