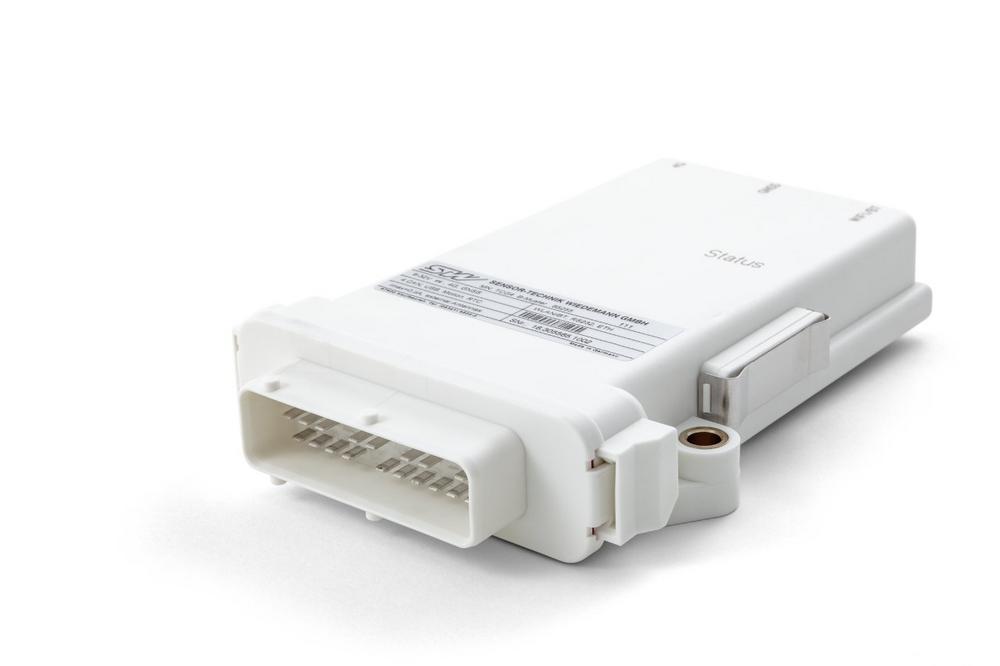
Greater efficiency in the cultivation of large agricultural fields
Maximizing crop yields is a goal of every farming enterprise. The development departments of agricultural machinery manufacturers recognize this and introduce larger and more complex machines to the market that promise more efficiency and higher yields. The goal of harvesting as much grain, fruit, vegetables or other agricultural produce as possible goes hand in hand with the need for precision. In recent years, precision farming has become a defining term for the industry. Precision farming requires high-performance control technology that collects and analyses the values recorded by the sensors, calculates corrections and passes these on to the implement’s actuators to ensure optimal processing of the cultivated area. This maximizes the efficient use of resources.
ISOBUS as a tool for perfect tractor-implement harmonization
Many agricultural applications require a close interaction between the tractor and the implement. This makes the exchange of sensor and control data both important and challenging, especially in view of the fact that tractor and implement often come from different manufacturers. This is where the ISOBUS comes into play as a neutral standard for communication between agricultural vehicles and implements.
The ISOBUS standard offers many advantages, including improved efficiency and productivity and increased ease of use as it facilitates control of the implement directly from the tractor cab. The AEF (Agricultural Industry Electronics Foundation), the organization behind the ISOBUS standard, is currently working on the introduction of high-speed ISOBUS. This extension of the standard interface will enable much faster data communication and allow much larger data streams to pass between vehicles and implements than was previously possible.
This brings enormous potential for innovative technologies including Tractor Implement Management (TIM). TIM enables bidirectional communication between tractor and implement. Until now, the tractor had the leading role in the agricultural process. The machine operator’s commands were passed on to the trailed implement via the on-board electronics and the ISOBUS interface, and the actuators acted in accordance with these inputs.
With the help of TIM, the implement’s sensor and control architecture can take over control of the process. The intelligence of the towed implement tells the tractor, for example, how much power is required or the optimum speed of travel over the area being cultivated. Again, this makes the process more efficient and helps to maximize yields.
Further, TIM reduces the load on the machine operator, who can now concentrate fully on controlling and monitoring the overall process, as otherwise repetitive and monotonous tasks are carried out automatically. The variance in the results, which typically depend on the expertise and experience of the operator, is minimized. Typical applications that particularly benefit from Tractor Implement Management include the automated adjustment of the width and depth during ploughing work. With the BCX.4cs-ag, STW offers a powerful on-board control unit that acts as a controller and central electrical system. It supports Tractor Implement Management via ISOBUS, as well as being able to switch and control larger electrical loads such as lights and motors. The ESX.4cl-ag mobile controller also supports high-speed ISOBUS.
High-performance computing for autonomous processes
Highly automated machines with autonomous work processes go even further in terms of maximizing efficiency. Humans are largely taken out of the equation as a factor in the success of the process. Self-driving harvesting vehicles that drive across fields based on GPS routes have been on the market for many years. They are now improved with AI supported assistance systems that promise that further increase the harvest yield. For example, STW is working on a development project for a 360-degree bird’s eye view camera system with integrated person and object recognition. This will provide greater safety for people and animals in the field, and greater safety for the machines, as collisions and costly repairs can be avoided. Especially during the time-critical harvesting process, downtimes associated with damaged machinery can have far-reaching economic consequences.
The high-performance computer HPX, which STW has developed for such highly demanding AI applications, provides the hardware basis for this system. The HPX utilizes the latest innovations from chip manufacturers to offer maximum performance.
Cloud connection and digitalization for greater data transparency
However, computing power on the machines remains finite, even with the most powerful control units. One approach to overcoming this limit is the use of edge and cloud computing. Leading agricultural machinery manufacturers are already using services such as Amazon Web Services to improve production processes and outsource big data processing. They offer the advantage of being able to collect gigabytes of data continuously from a large number of sources and be scaled flexibly as more sources become available.
STW has demonstrated in a proof of concept study how the interaction of powerful computer architectures on mobile machines and stationary surveillance cameras, with the help of 5G edge computing infrastructure, can realize assistance functions. In this scenario, STW uses the HPX as a high-performance computer on the machines, which pre-processes video data and sends it to the cloud via the STW TCG-4 communication module. The system takes into account additional data from the surrounding infrastructure, for example from surveillance cameras. By using 5G transmission technology, very high data rates with low latency times, real-time capability can be ensured. The study partners were able to combine and channel a large amount of heterogeneous data from mixed fleets of machines and devices, and external data suppliers, and use it to make decisions for automated and autonomous processes.
In agricultural engineering, this approach offers the potential to network machine fleets made up of a wide variety of models and manufacturers. As such a system has no inherent restrictions on locality, cross-regional solutions for field logistics can be implemented that optimize the complex processes of farm management.
STW sees itself as a cooperative partner to agricultural machinery manufacturers and provides support both in the development of customized solutions and in the implementation of the systems. Thanks to STW’s participation in a large number of cross-manufacturer research projects, machine manufacturers can benefit from the latest scientific findings and work with STW to develop new and innovative systems that lead to a competitive advantage.
STW will be showcasing its innovations for agricultural machinery manufacturers at the Agrishow in Ribeirão Preto, the largest trade fair for agricultural technology in Brazil. Experts from STW will be at the Agrishow in Brazil to meet visitors at the German Pavilion, G8d booth 3, from April 29 to May 3, 2024.
STW is an internationally active company headquartered in Kaufbeuren, Germany. We have produced outstanding solutions for the automation and digitalization of mobile machines for more than 35 years. With our modular system of generic and customer-specific products, systems and software solutions, we support our customers with our innovative technology in making their machines the best in the world.
For our customers, we represent a partner to accompany them in the engineering and integration of new technology. With our modular system of interoperable components, compatible products and systems from our global partner network and our extensive software toolchain openSYDE, we help OEMs increase the performance and efficiency of their machines, enhance safety, and meet the emerging technology challenges. Our ready to use connectivity solutions enable machine-to-X communication, making networking with cloud platforms and the integration of the mobile machine into business processes possible.
(STW) Sensor-Technik Wiedemann GmbH
Am Bärenwald 6
87600 Kaufbeuren
Telefon: +49 (8341) 9505-0
Telefax: +49 (8341) 9505-55
http://www.stw-mm.com
Specialist Marketing Communication
Telefon: +49 8341 9505 3450
E-Mail: laura.mitlewski@wiedemann-group.com

