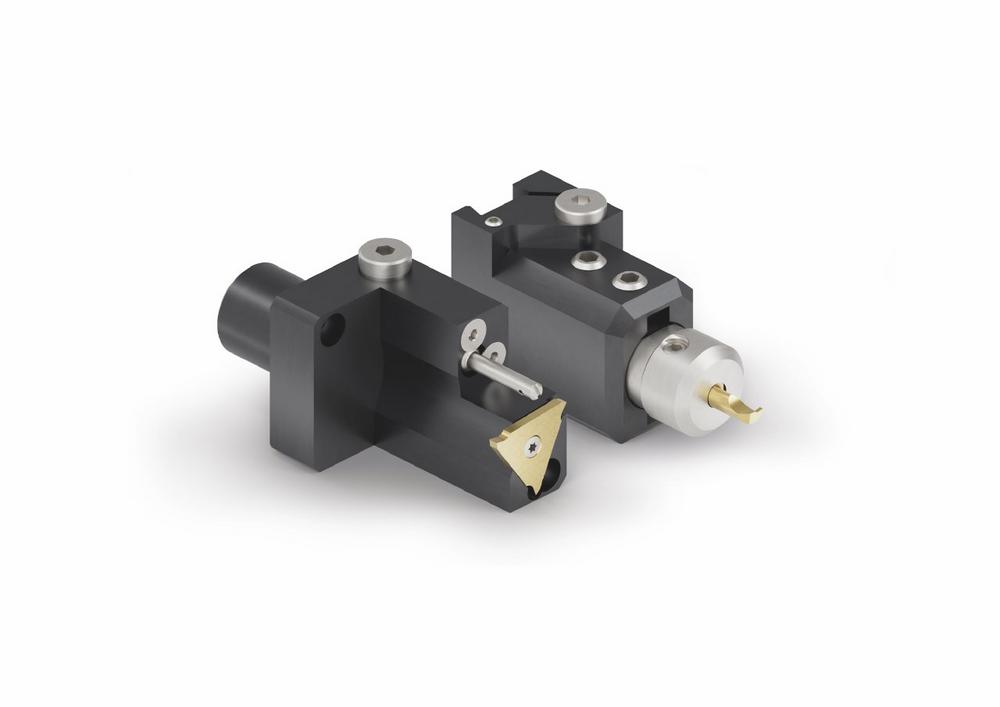
Complete machining alleviates shortage of skilled labour
The pressure in metal-cutting production is gradually intensifying as there are fewer or less qualified people on the labour market. At the same time, the challenges facing labour-intensive machining processes in manufacturing companies due to the increasing shortage of skilled workers have not yet fully materialised. The labour situation will really start to get worse when the current skilled workforce retire in the next five years. And the workers who are still willing to work hard may not have the skills to do many of the things that are required. So it’s high time for companies to start preparing for this.
Current skilled workforce leave enormous gaps
One good approach for turning shops could be to involve their own tool partner. The fact is that, if tool manufacturers think from the customer’s and user’s perspective, they also have tools and solutions in their portfolio to take this very situation into account and permit machining operations requiring less staff. This is particularly interesting in machining situations where fully automated processes are not possible.
One of these forward-thinking tool manufacturers is Arno Werkzeuge from Ostfildern near Stuttgart. The family-run company has a wealth of expertise drawn from its many application consultations resulting from its proximity to customers. This is also reflected by a range of tools that focuses on complete machining wherever possible. Users can therefore rely on fast and easy-to-use tool changing systems for both fixed headstock and Swiss-type auto lathes. Brand new holders for back working also facilitate metal-cutting processes, making it easier even for semi-skilled workers.
Easy-to-operate systems are very frequently the key to higher productivity
The Swabian company has recently added height-adjustable holders for back working to their product range. These holders have a number of impressive features that are not found in other conventional systems. In particular, the new recently introduced height-adjustable holders for machines without a Y2 axis can be finely pre-adjusted off-machine using an adjustment device. They not only increase production and machine running times but the process is also easy to learn.
The easy-to-install system consists of a basic holder, spacer plate, top holder and coolant supply attachment. The basic holder is precision clamped and fixed by a simple dovetail guide. In addition to greater stability, this clamping device has smooth surfaces to prevent chip build-up. Operators can also adjust the tool length using a spacer plate which is simply pushed over the shaft of the basic holder – it couldn’t be easier. The top holder and coolant supply attachment can be firmly connected by a simple clamp. They are each fixed by just one screw.
Tool changing scenarios must be made simpler to handle
Tool changing scenarios always present a challenge that can cost time and create sources of error. However, for trained lathe operators who have mastered the complexity and principles behind the processes, these are everyday tasks that do not pose any problems. Semi-skilled workers presumably may not have the skills required to cover all the dimensions of today’s highly developed turning processes. They are also unlikely to be able to utilise the possibilities of powerful machines creatively. Tool manufacturers who take these scenarios into account now will have a competitive edge on the market.
For example, the new holders from Arno Werkzeuge retain the centre height setting when the tool holder is changed. This ensures repeat accuracy and saves a great deal of time. All in all, the system with its height-adjustable basic holders is very well thought out. It saves space, it is flexible and can be fitted to various different machines. This is also an important factor since it reduces confusion. The optional coolant supply attachment with adjustable high-pressure jets supplies the coolant directly to the tool’s cutting edge. Holders are designed with carbide insert shims to ensure a long-life insert seat and longer change cycles.
Complete range supplies coolant to the flute
When tool changing situations can be completely eliminated, things naturally become even easier. For example, Arno Werkzeuge has developed fixed holders with tools for machines with a Y2 axis. The adjustable axis of these holders for Star and Citizen machines sets the centre height. The holders are designed in collaboration with the machine manufacturers for optimum dimensions and are therefore very compact. Combined with the fastening by two screws on the front and on the shaft diameter, these holders promise high stability. The through tool coolant supply can be connected from either side and coolant jet adjustment is intuitive.
It is also easy to fit a high-pressure coolant supply to the tools because users have access to a wide range of accessories. The accessories include coolant distributors, hoses, connectors, quick-release couplings, swivel fittings, jets and coolant supply attachments. This allows the full range of cooling benefits to be used on Swiss-type auto lathes. Here, too, Arno Werkzeuge provides simple solutions and demonstrates its extensive experience by analysing the situations of many users – especially when skilled labour is becoming increasingly difficult to find for production.
Avoiding tool changing situations is much better than making them easier
If a tool manufacturer can offer systems that make it easier to change tools, it is already a positive step forward in times of skilled labour shortages. But it is even better if tool changes can be dispensed with altogether. One solution in this direction is tool changing systems as offered by Arno Werkzeuge. The patented AWL tool holder system can accommodate two to eight tools depending on the machine and design. This allows a whole range of turning operations to be carried out without the need for human intervention.
The AWL direct mount also has an integrated coolant supply. Two separate cooling channels in the tool holder system supply coolant to the cut point at high pressures of up to 150 bar. Each chamber has an integrated coolant supply that can be opened or closed with just one simple operation depending on the machining situation to allow the simultaneous use of tools with or without through-tool coolant supply. The high pressure causes the chips to break differently so they can be reliably flushed out. There is no need for external hoses or interfering contours inside the machine. It also means that there are no surfaces to which chips can adhere and build up to become interference factors. It also means that semi-skilled labour can be used. This is because it requires an experienced worker who knows when to intervene if there is chip adhesion and build-up.
Tool changes when required should be as simple as possible
If tool changes are required, the AWL direct mount is backed by the AFC quick-change tooling system. It takes only a few simple operations to remove or fit two-part tools comprising holder and fixed stop. Interchangeable tool holders bearing the tool can be fitted and removed from the fixed stop in no time at all. Only the front part needs to be removed to fit the other holder and the new insert. When they are fitted together, they are tightly connected so that the tool does not accidentally fall into the machine. Since the tools are fixed very securely in the tool changing system, there is less vibration. As a result, the surface quality of the machined workpiece is often enhanced and downstream machining steps can sometimes be omitted. This also saves skilled labour.
Conclusion:
Tool manufacturers must reduce complexity
In view of the skilled labour shortage now and in the future, tool manufacturers need to rethink their approach. Arno Werkzeuge, whose products are easy to use, adjust, change and handle, is a good example of how this can be achieved.
Customer proximity and development power
Emil Arnold set up ARNO Werkzeuge Karl-Heinz Arnold GmbH in 1941 as an innovative tool manufacturer and the company is now in the third and fourth generations of owner management. The company has a high manufacturing depth, in-house development competence and a global sales organisation. It produces highly modern, high-performance tools which are used world-wide in production with fixed headstock machining, Swiss type machining, parting, grooving, turning, drilling and milling. One of the company specialities is ground high-positive indexable inserts for complex manufacturing operations. Here, ARNO offers the largest portfolio in the world.
Customised tool solutions, which later become highly coveted standards, are developed in close collaboration with our customers, taking their requirements into consideration. The tradition-based company ensures customer proximity by a work force of over 200 employees at its head offices in Ostfildern and its numerous sales offices all over the world. Last year, ARNO achieved a turnover of almost €58 million, a record in the company’s history.
ARNO Werkzeuge
Karlsbader Straße 4
73760 Ostfildern
Telefon: +49 (711) 34802-0
Telefax: +49 (711) 34802-130
http://www.arno.de
Unternehmungskommunikation
Telefon: +49 (0)711 34802 0
E-Mail: kknapp@arno.de

