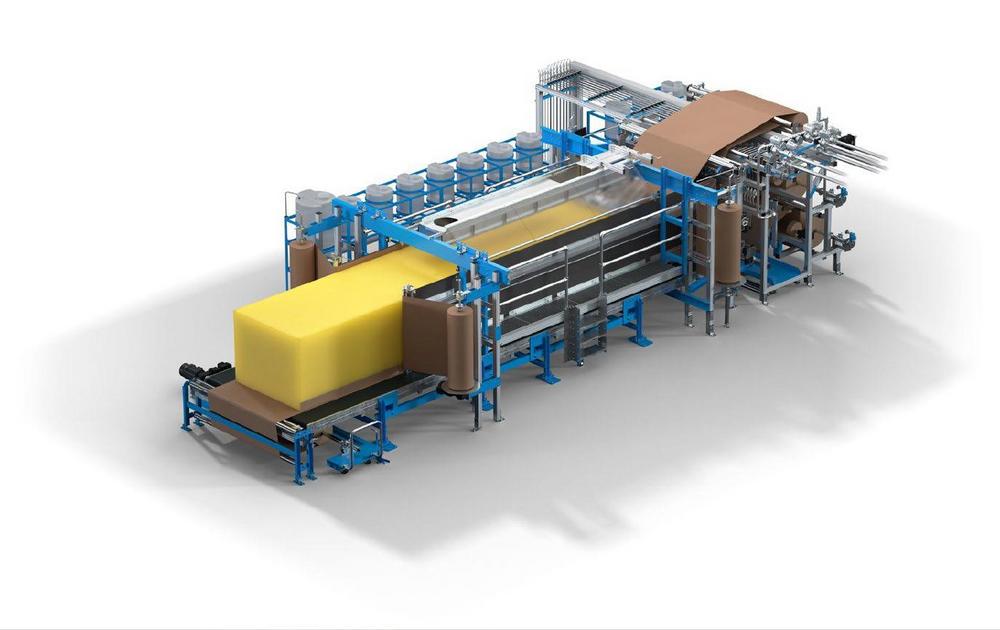
JFLEX evo: Slabstock foam production with continuously variable foam widths – more flexible, more convenient, more secure
Continuous Adjustment of the Foaming Width
A particular highlight of the JFLEX evo is the continuous adjustment of the foam width, which makes the production of a range of products highly flexible and efficient. The quick and convenient adjustment option significantly reduces the set-up time and makes the precise adjustment of the required widths between 1550 and 2300 mm possible. This significantly reduces side-trim losses and noticeably increases raw material efficiency. "We have already revolutionized the market with slow-running continuous slabstock machines with the JFLEX and its established characteristic J-Pipe retaining zone. With the JFLEX evo integrated continuous width adjustment, we now offer our customers another innovative feature so that they can react to the constantly changing market requirements with maximum flexibility and without compromising high foam quality", explains Daniel Krämer, Mechanical Engineer at Hennecke.
The FLAT-TOP system included as standard ensures evenly formed foam blocks and allows the pre-set foam widths to be adjusted in a matter of seconds. This reduces cutting losses and increases raw material efficiency, whilst simultaneously ensuring a homogenous cell structure and high-quality foams.
Increased Safety and Operating Comfort
The JFLEX evo also impresses with optional walkways along both side walls. These enable maximum seamless and secure monitoring of the production process at all times. The SMARTJECTORS included in the standard scope of delivery also offer greater process stability. These are software-controlled pneumatic valves that act as injectors for the additional components required for foam production. Using the SMARTJECTORS, it is now possible to add or exclude all additional materials found in the system metering scope fully automatically and based on software, depending on the formulation of the foaming process. This minimizes the error tolerance and increases operating safety.
Automated Process Control
The JFLEX evo is operated via the latest version of the intuitive FOAMWARE software, which is specially tailored to the requirements of slabstock foam manufacturers. The standard scope of delivery includes a range of functions, such as the display of flow charts, process charts, and calibration history, as well as other tools for an effective analysis of nominal and actual values. The clear graphic display of the "Magic Eye" facilitates seamless monitoring of all generated pressures and quick recognition of potential irregularities.
All Advantages of the Tried and Tested JFLEX Concept
The JFLEX evo is based on the successful JFLEX concept, which makes the advantage of continuous production possible for foamers with an average production volume. "We have received lots of positive feedback for the JFLEX from our customers and incorporated this into the new JFLEX evo. The further development of the system – just in time for its 10-year anniversary – is therefore also a sign of our constant gratitude for our customers", reports Karim Nabulsi, Sales Manager at Hennecke. At the heart of the system is the combination of the innovative J-Pipe retaining zone, the rise-plate, and Hennecke’s high-pressure technology. The ultra-compact system with a 54 m² footprint and a height of three meters saves valuable production space and can be used almost anywhere – a great advantage against conventional continuous slabstock machines. Thanks to the plug and play concept, the system can be built and put into operation quickly. The low conveyor speed facilitates the continuous production of high-quality slabstock foams with a total length of the system of only around twelve meters. Furthermore, it ensures the highest efficiency and production quality, reduces the duration of formulation changes and makes extremely short color transitions possible. During production, only very short start and end blocks are created, noticeably reducing waste.
Hennecke once again emphasizes its position as a leader in innovation in polyurethane processing technology with the JFLEX evo. The system offers foam manufacturers a future-proof solution that enables them to flexibly adapt their production to constant new requirements and simultaneously benefit from the advantages of continuous production. Hennecke also offers comprehensive support services to help users get the best out of the JFLEX evo.
Hennecke GmbH
Birlinghovener Straße 30
53757 Sankt Augustin
Telefon: +49 (2241) 339-0
Telefax: +49 (2241) 339-204
http://www.hennecke.com
Specialist Marketing & Communication
Telefon: +49 (2241) 339-232
E-Mail: rebecca.sinnig@hennecke.com

