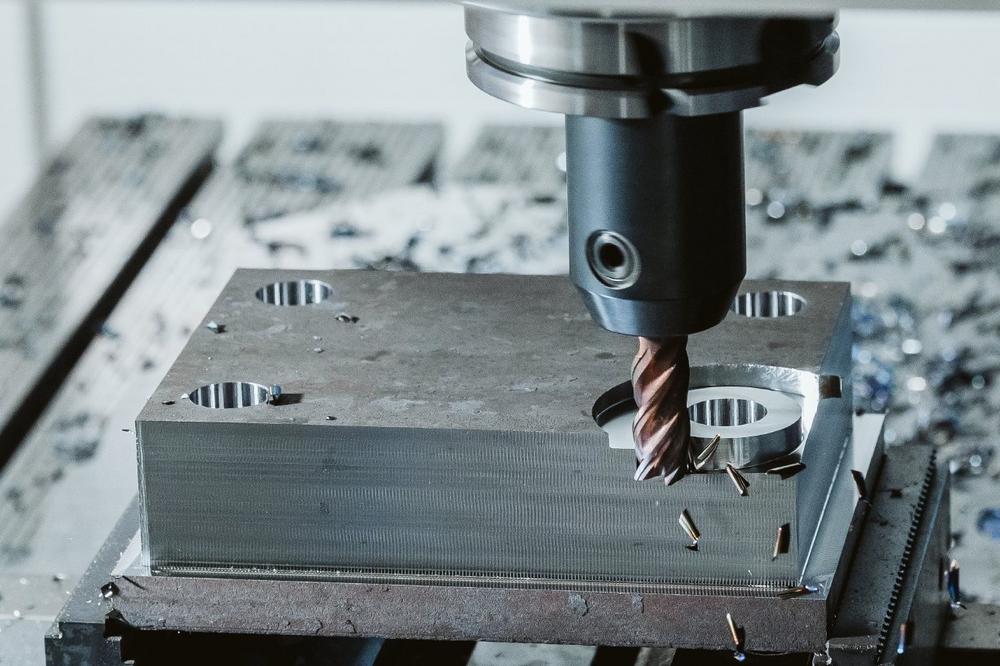
Powerful milling – with built in sustainability!
Machining a wide variety of materials means constantly adapting to new challenges. The solution takes the form of universal milling cutters that can cope with steels, stainless steels and cast materials in equal measure. Alongside the targeted process efficiency, the aspect of sustainability is increasingly growing in importance. CERATIZIT shows how the two objectives can be reconciled – with the ProACT-Mill universal solid carbide milling cutter series. The milling cutters are manufactured from a particularly sustainable carbide, which CERATIZIT calls upGRADE.
Full performance from 99% reprocessed raw material
The upGRADE CT-GS20Y grade is the ideal choice for a wide range of applications. "What’s special about it is the significantly smaller carbon footprint generated during production, compared to carbides from conventional production. We achieve this by using 99% reprocessed cutting tools as a raw material," explains Michael Wucher, Global Technical Product Manager at CERATIZIT. Customers enjoy both economic and ecological advantages, thanks to a specific product carbon footprint (PCF).
The test results of the new series underline its potential: ProACT-Mill milling cutters deliver up to 30% higher performance compared to other universal tools. The newly developed coating, which brings with it additional performance and tool life reserves, further contributes to this.
The new ProACT-Mill UNI and UNImax power milling cutters
"With the ProACT-Mill Series, we’ve developed our most powerful tool for universal milling, packed with everything that modern milling cutters need – including CT-GS20Y, our most sustainable carbide grade to date," says Michael Wucher, Global Technical Product Manager at CERATIZIT. The variable helix pitch ensures extremely quiet running and optimum chip removal. The ProACT-Mill UNI has an HB shank for perfect force transmission, while the reinforced tool core ensures even force distribution throughout the milling process.
To guarantee unbeatable cutting edge stability, the milling cutter has been given a radial clearance face. The face finishing chamfer promises top surface quality with base machining, while cutting edges with an irregular pitch specifically suppress vibrations. Ramping milling and helical milling are possible up to an angle of 30°. Thanks to the impressive milling acoustics of the ProACT-Mill UNI (even with high infeed values and full-face milling), the machine room is never too noisy.
The ProACT-Mill UNI with a cutting edge length of 3xDC is particularly suitable for series production and trochoidal machining. Innovative chip breakers in a radial design deliver the longest possible tool life and break the chips to a length of 1xD; these are then evenly and consistently removed due to the special shape of the chip space. Thanks to the minimal conical tool core, the 5-edge cutter runs very quietly even with a high lateral width of cut.
When it comes to maximum material removal rates, the ProACT-Mill UNImax is the ideal solution. A special geometry design has been selected for this purpose – and is perfectly suited for depths of cut of up to 2xDC. The tool is available with HA and HB shanks for unbeatable force transmission and balance qualities. With the variable tool core, optimum force distribution was the key focus.
Data Matrix Code has all the details
All tools in the series bear a laser-applied Data Matrix Code (DMC), which can be used to call up the data of the "digital twin". "This DMC contains all the information needed – once scanned, the tool can be correctly identified and its relevant technical data displayed. The customer can also see whether the tool is new or reconditioned, and how often it has already been sent to us for regrinding. And there is of course also a link to the online shop to make reordering quick and easy. We’ll be expanding the DMC functions in the future to deliver an even more comprehensive service," reveals Michael Wucher.
CERATIZIT – with passion and a pioneering spirit for hard materials
For more than 100 years, CERATIZIT has been a pioneer in the field of sophisticated hard material solutions for machining and protection against wear. The private company, with registered offices in Mamer, Luxembourg, develops and produces highly specialised cutting tools, indexable inserts, rods made from hard materials and wearing parts. The CERATIZIT Group is the global market leader in various application segments and successfully develops new carbide, cermet and ceramic grades, such as for wood and stone working.
With over 7,000 employees at more than 30 production facilities around the world and a sales network with over 50 branches, CERATIZIT is a global player in the carbide industry. The company’s international network includes subsidiary Stadler Metalle and joint venture CB-CERATIZIT.
CERATIZIT is a technology leader which is constantly investing in research and development and holds more than 1,000 patents. Innovative hard material solutions from CERATIZIT are used in various sectors, including mechanical engineering and toolmaking, in the automotive and aerospace industries and in the oil, gas and medical industries.
CERATIZIT Deutschland GmbH
Zeppelinstraße 12
87437 Kempten
Telefon: +49 (831) 57010-0
Telefax: +49 (831) 57010-3559
http://cuttingtools.ceratizit.com
PR Manager Cutting Tools
Telefon: +49 (831) 57010-3405
Fax: +49 (831) 57010-3678
E-Mail: norbert.stattler@ceratizit.com

