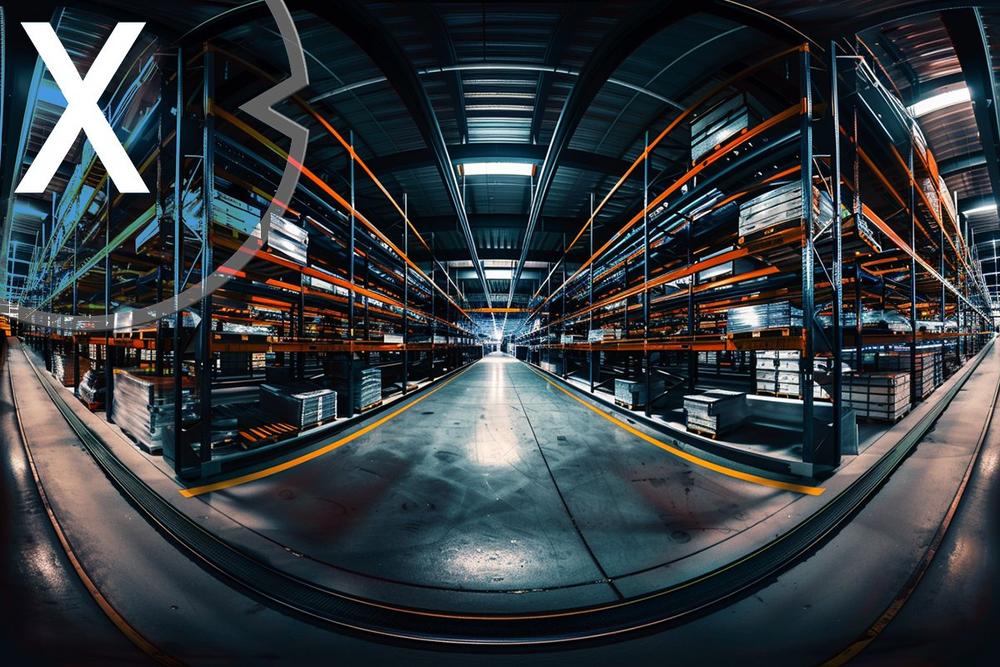
Choosing the right storage system: Whether high-bay warehouse, conventional pallet racking, automated or special types of storage
Warehousing is a central part of the supply chain and has a significant influence on the efficiency and profitability of a company. A well-designed warehouse system can not only reduce operating costs, but also increase productivity, shorten delivery times and increase customer satisfaction. However, different products and industries require specific storage solutions that are tailored to their particular properties and requirements. Various storage systems are described in detail below, each of which is particularly suitable for certain product types and storage requirements.
► Conventional pallet racks
Conventional pallet racks are the most common form of storage and are characterized by their flexibility and adaptability. They allow direct access to each individual pallet, which is particularly advantageous in warehouses with a large variety of products and a small number of pallets per item. These shelves are modular and can be adjusted in height, width and depth to suit the specific needs of the warehouse.
The advantages of these shelving systems lie in their easy installation, maintenance and expandability. They are ideal for companies with high inventory turnover and frequent changes in the product portfolio. By using accessories such as gratings, shelves or push-through protection, the shelves can be individually adapted to the goods to be stored, be it for palletized goods, boxes or unpackaged products.
► Drive-in and drive-through racks
Drive-in racks and drive-through racks are compact storage systems that enable maximum space utilization. With drive-in racks, the rack is driven into from one side and the pallets are stored one behind the other in deep channels. This system works according to the last-in-first-out principle (LIFO), as the last pallet stored is the first to be removed.
Drive-through racks, on the other hand, offer access from both sides and enable storage according to the first-in-first-out (FIFO) principle. The pallets are stored on one side and removed on the opposite side. These systems are particularly suitable for homogeneous products with a high turnover rate and a low variety of items, such as in the food or beverage industry.
The main advantages are the high storage density and the efficient use of space, as intermediate and service aisles are reduced or completely eliminated. This results in significant space savings and can increase storage capacity by up to 85%.
► Mobile shelves
Mobile shelving, also known as mobile shelving, is an innovative solution for optimizing storage space. They consist of shelves mounted on rails or movable bases that can be moved electrically or manually. By collapsing the shelves, the space required for aisles is minimized because only the required access aisle is always opened.
These systems offer direct access to all pallets and are therefore ideal for warehouses with a large variety of products and medium to low goods turnover. Mobile shelving is often used in areas where a high level of space utilization while protecting the stored goods is required, such as in archives, libraries or in the pharmaceutical industry.
Another advantage is energy efficiency, especially in cold storage. Compact storage reduces the volume to be cooled, which can result in significant cost savings. Mobile racks also help to improve work processes by shortening travel times and making it easier to organize inventory.
► Compact storage systems
Compact storage systems such as push-back racks or flow racks are designed to make optimal use of the available space while enabling a high turnover of goods. Push-back racks work according to the LIFO principle: pallets are pushed into the rack from the front, with the existing pallets being moved to the back on special trolleys or rollers. When removed, the rear pallets automatically slide forward.
Flow racks, on the other hand, work according to the FIFO principle. Pallets or boxes are placed on the loading side of the rack and move by gravity on inclined roller conveyors to the removal side. This system is particularly suitable for products with an expiration date or those where the order of withdrawal is critical, such as in the food and beverage industry.
The advantages of compact storage systems lie in the high storage density, the reduction of travel times and the improvement of the flow of goods. They enable quick and efficient picking and help optimize warehouse processes.
► Automated storage systems
Automation has become increasingly important in warehousing in recent years. Automated storage systems such as automatic small parts warehouses (AKL) or automatic high-bay warehouses (HRL) use modern technology to optimize storage and retrieval processes. They are characterized by high speeds, precision and reliability.
In an AKL, small to medium-sized items are stored in containers or boxes and are automatically stored and made available by storage and retrieval machines or shuttle systems. Automatic high-bay warehouses are designed to store pallets and can reach heights of up to 50 meters. Control is carried out via warehouse management software that monitors inventories in real time and processes orders efficiently.
The advantages of automated systems are manifold: They increase storage capacity, reduce error rates, improve safety in the warehouse and enable 24/7 operational availability. They are particularly suitable for industries with high requirements for speed, precision and traceability, such as e-commerce, the automotive industry or the pharmaceutical industry.
► Chaotic storage systems
The chaotic storage system, also known as dynamic storage, does not require fixed storage locations for items. Instead, goods are stored in any free space and powerful warehouse management software documents the exact positions. This system offers a high level of flexibility and enables optimal utilization of storage capacities.
The main advantages are the ability to quickly adapt to changing inventories and requirements. Travel times can be reduced because the software calculates the optimal storage and retrieval strategies. However, this system requires a reliable IT infrastructure and well-trained staff to ensure data integrity.
Chaotic storage systems are particularly suitable for companies with a wide range of items and varying inventory levels, such as in mail order or spare parts supply.
► High-bay warehouse
High-bay warehouses make optimal use of the vertical space and thus enable maximum storage capacity in a small footprint. They can be operated manually with special forklifts or automatically with storage and retrieval machines. With heights of up to 50 meters, they are impressive structures that enable efficient use of space.
Automated high-bay warehouses offer numerous advantages: They increase turnover speed, reduce personnel and operating costs and improve inventory accuracy. Automation also minimizes safety risks for employees. High-bay warehouses are ideal for companies with high inventory levels and a constant flow of goods, such as in production logistics or wholesale.
► Special storage types
In addition to the standardized storage systems, there are special types of storage that are tailored to specific requirements:
□ Hazardous material storage
These warehouses meet strict safety and environmental requirements for storing hazardous substances such as chemicals, flammable or toxic materials. They are equipped with special safety devices such as fire protection systems, drip trays and ventilation systems.
□ Cold storage and deep-freeze storage
Constant temperatures are crucial for temperature-sensitive products such as food or pharmaceuticals. These warehouses are energy-efficiently insulated and equipped with precise cooling systems to maintain the quality of the products.
□ Clean room storage
In industries such as electronics or pharmaceuticals, products must be stored under controlled conditions to avoid contamination. Cleanroom warehouses have special air filter systems and strict access controls.
□ Outdoor camp
Outdoor storage areas can be used for weather-resistant products such as building materials or steel. However, these warehouses require special measures in terms of theft protection and warehouse organization.
► The well-thought-out storage system
Choosing the right storage system depends on a variety of factors:
□ Product features
The size, weight, shape and sensitivity of the goods to be stored influence the choice of system.
□ Turnover rate
Products with high turnover require systems that enable quick storage and retrieval.
□ Variety of articles
A large product range requires flexible storage solutions with direct access.
□ Space capacity
The available areas and heights in the warehouse determine the possible systems.
□ Investment budget
Acquisition and operating costs must be in proportion to the benefits.
□ Future planning
The storage system should be scalable to respond to growth or changes in the market.
A well-designed storage system contributes significantly to the efficiency and competitiveness of a company. It optimizes internal processes, reduces costs and improves customer satisfaction through faster and more reliable deliveries.
► Modern developments and trends
Digitalization and automation are increasingly shaping warehousing. Technological innovations such as artificial intelligence, robotics and the Internet of Things (IoT) open up new possibilities:
□ Automated picking
Robots and driverless transport systems take over the assembly of orders, increasing speed and accuracy.
□ Real-time data analysis
Through sensors and connected systems, inventory levels can be monitored and analyzed in real time, enabling proactive planning.
□ Sustainability
Energy-efficient systems, the use of renewable energies and resource-saving materials are becoming increasingly important and can save costs and improve the company’s image.
□ Flexibility
Modular systems and scalable solutions enable companies to react quickly to market changes.
⬛ Find out more here:
► A strategic decision
Choosing the right storage system is a strategic decision that requires careful planning and analysis. By taking specific requirements into account and using modern technologies, companies can optimize their warehousing and achieve a decisive competitive advantage. An efficient storage system not only increases productivity and customer satisfaction, but also contributes to the sustainable development of the company.
This comprehensive overview shows how diverse the possibilities are in modern warehousing. The challenge is to find the system that best suits the company’s individual needs and goals. With the right choice, companies can maximize their efficiency, reduce costs and successfully prepare for the demands of the future.
Xpert.Digital ist ein Hub für die Industrie, mit den Schwerpunkten, Digitalisierung, Maschinenbau, Logistik/Intralogistik und Photovoltaik.
Mit unserer 360° Business Development Lösung unterstützen wir namhafte Unternehmen vom New Business bis After Sales.
Market Intelligence, Smarketing, Marketing Automation, Content Development, PR, Mail Campaigns, Personalized Social Media und Lead Nurturing sind ein Teil unserer digitalen Werkzeuge.
Mehr finden Sie unter: www.xpert.digital – www.xpert.solar – www.xpert.plus
Xpert.Digital – Konrad Wolfenstein
Mörikeweg 4
89160 Dornstadt
Telefon: +49 89 89 674 270
Telefax: +49 32 22 130 283 6
http://xpert.digital/
Xpert.Digital
Telefon: +49 157 30 44 9 555
Fax: +49 32 22 130 283 6
E-Mail: wolfenstein@xpert.digital
