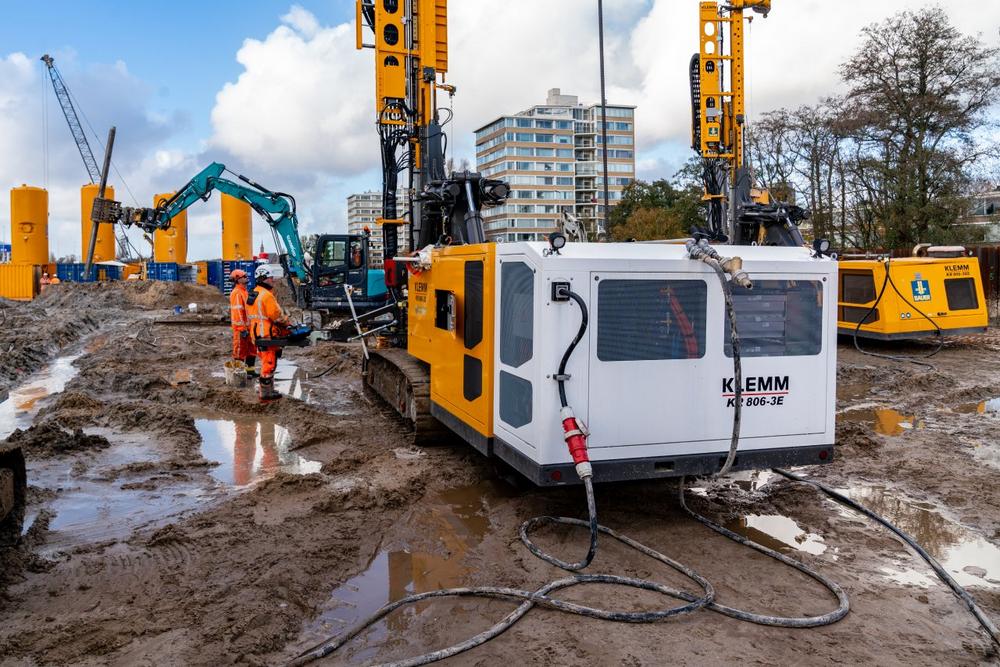
The Electrification of a Construction Machine
Background
The European Union has introduced the European Green Deal as a comprehensive strategy to combat climate change. The aim is to decarbonize the EU economy by 2050. As part of the European Climate Law, the EU has committed to reducing its greenhouse gas emissions by at least 55% of 1990 levels by 2030. As in other industrial sectors, this increases the pressure on the construction machinery industry to develop more environmentally friendly machines.
Some EU member states are stimulating these efforts through subsidy programs for the acquisition and use of electric construction machinery, among other things. Grants, tax breaks or favorable loans are intended to reduce investment costs and facilitate the switch to more sustainable technologies.
The administrations of some metropolitan areas that have joined the "C40 Cities" network have been relying on regulations and bans for urban construction projects since 2021. This is driving the use of electric construction machinery. Such cities include Barcelona, Helsinki, Stockholm, Copenhagen, Munich and Oslo [1]. Stockholm and Oslo have announced that all construction sites are to be emission-free or climate-neutral by 2030. This makes the use of conventional, diesel-powered construction machinery practically impossible.
Essentially, the following drive technologies are currently accepted as CO2 emission-free replacements for diesel engines:
- Electric drives that use electric motors, often in combination with an electric battery storage system.
- Fuel cell units that use hydrogen as a fuel to generate electricity. Water is produced as an emission product. This technology is still the subject of research in the construction machinery sector [2].
- Hydrogen internal combustion engines in which hydrogen is injected into the combustion chamber and mixed with air. Combustion produces water and heat as by-products. However, converting a combustion engine to hydrogen requires significant modifications. Series production of such motors is planned for stationary power generators, for example [3].
The EU requirements on noise reduction for mobile machinery (2000/14/EC) and the planned tightening of the Air Quality Directive (2008/50/EC) must also be taken into account. Electric drives can make a significant contribution here.
Theory and practice
The potential CO2 savings during operation can be roughly measured for an anchor drilling rig. With emissions of appoximately 2.65 CO2 kilogram per liter of diesel fuel, one can calculate, based on 2000 working hours per year, and an average consumption of 10.4 l/h, with a yearly overall release of 55 t of carbon dioxide. To completely reduce this volume, the diesel-based drive system must be fundamentally changed.
The drive concepts for e-mobility have now been essentially developed and are well known. Nevertheless, the functional principles of battery electric vehicles (BEV) cannot simply be transferred to mobile construction machinery, and this applies especially to an anchor drilling rig. The main differences lie in the number and characteristics of the numerous main and auxiliary consumers, the high powered engines, the high-level energy conversion and the constant availability on the construction site.
Mobile construction machinery also differs in terms of the proportion of continuous or intermittent power requirements and the possibility of recuperation. The operating environments which are extreme at times pose a further challenge.
For this reason, how the respective construction machine will be used must be very precisely known when designing a new type of drive. It has also become clear that any existing electric drive concepts cannot be simply transferred from one type of construction machine to another. This even applies within a single category of construction machinery if they differ greatly in terms of engine output, for example.
Supplying a mobile machine with electrical or regenerative energy on the construction site is a further challenge, not only for high electrical outputs, but also in terms of the hydrogen supply.
Tests on Kelly pile drilling rigs have shown, as anticipated, that the efficiency of the electric drivetrain is significantly better than that of the diesel drivetrain. However, the uptime in pure battery operation ("off-grid") is restricted due to various factors. Longer recharging times during which the drill cannot be used must be taken into account [4].
Concept
Several requirements were placed on the electrification of the KLEMM KR 806-3E anchor drilling rig. The drilling rig was to be on a par with its conventional counterpart, the KLEMM KR 806-3GS, in terms of drilling performance and scope of application. Operation was to be as simple as possible for the drill operator so the entire operating concept (radio remote control) could be maintained. It also needed to be possible to use a construction site power supply with a connection of max. 125 A / 400 V AC, which is easy for a construction site to obtain. To safeguard against development risks, the decision was made to retain the familiar hydraulic part of the drivetrain in the initial step, including the load-sensing hydraulic circuits and the hydraulic consumers (cylinders, hydraulic motors, etc.). This is why it is called an electro-hydraulic drivetrain. It gives the user the ability of continuing to use existing drilling systems and components such as rotary drives etc.
In order to calculate the energy supply, the operating data of a larger number of anchor drilling rigs with the same output were first evaluated. Telemetry (KLEMM Datalink AIR) proved to be extremely useful for this purpose. It was found that the power demand for anchor drilling machines in the 160- to 175- kilowatt power range is a maximum of 35% on average. This is due to the typical intermittent mode of operation with interruptions due to rod changes, anchor installation, etc. Over a longer period of time, the power requirement is therefore around 56 kilowatts.
A 400 VAC / 125 A connection can deliver an electrical output of approximately 86 kilowatts. It, therefore, made sense to use a battery to cover the machine’s remaining power requirements during power peaks. This battery is automatically charged when the power requirement falls below 86 kilowatts.
To scale the capacity of this battery, real power profiles of different operating phases were superimposed in a simulation with the calculated discharging and charging capacities of different battery sizes and different power connections (125 A, 63 A, 32 A), see Figure 1.
With a gross battery capacity of 140 kWh and a 125 A connection, the objective was for continuous use of the machine to be possible without any problems under normal conditions, plus an off-grid usage time of approx. 2 to 3 hours. As the discharge capacity of the battery is sufficiently high, all drilling functions are available at maximum power in off-grid mode, not just loading, driving and maneuvering operations alone, albeit for a limited time.
The machine can also be operated using a 63 A and even a 32 A connection in combination with a battery with correspondingly longer charging times. The drivetrain can also be configured without a battery, but in this case a connection option with a nominal 250 A is required.
The on-board electrical system was designed as an 800 V DC system for the permanently excited synchronous machine. When using the battery, an isolating transformer, an insulation monitor and corresponding software ensure that the correct electrical network configuration (IT, TN-S) is maintained in addition to galvanic isolation. The rig has no onboard charger, which prevents a permanent high current flow through the battery, providing more protection for the battery.
Cooling and heating systems for the battery, the electric motor and the power electronics (inverter, line filter, etc.) are available or can be retrofitted if required.
Developing the software for battery and energy management was another comprehensive task. The software was a completely new development by KLEMM, as was the actual machine control system.
Prototype
The first step was to ensure that the personnel involved were qualified to work on vehicles with high-voltage systems. In Germany, for example, this is regulated by DGUV 209-093 (German Social Accident Insurance).
The battery, the isolating transformer and part of the thermal management system were arranged in a "backpack" at the rear of the machine. This makes them very easily accessible, see Figure 2.
The prototype of the KR 806-3E was exhibited to the public for the first time at the BAUMA 2022 trade fair and later demonstrated to an international audience of experts, see Figure 3. Further tests were then undertaken at the KLEMM plant; this included tests on inverter and filter characteristics, the cooling behavior, noise emissions and battery management. The time required for these tests and adjustments was longer than initially assumed.
Use on construction sites
After extensive training of the operating personnel, the drilling rig was used for several weeks from the end of October 2023 by BAUER Funderingstechniek on a construction site in the Netherlands, see Figure 4. Here, micropiles (diameter 152 mm, maximum depth 42 m) were installed over a length of 1.6 km for the widening of the A9 highway near Rotterdam. Right from the start, the KR 806-3E drilling rig could be used without any problems. A further eight KLEMM anchor drilling rigs with diesel drive were used on the construction site, some of them with the Datalink AIR telemetry system. This meant that the machine functions, energy management, battery status, etc. could be tracked virtually online and compared with the pre-calculated values.
As a temporary solution for the power supply while testing the KR 806-3E, the contractor had opted for a 200-kilowatt power generator instead of an on-site power connection. The evaluation of the energy flows showed perfect characteristics when charging and discharging the battery, exactly as predicted, both in wired and off-grid operation. Off-grid drilling work at full power was possible for two hours at a time.
The average consumption of electrical energy per operating hour was 32 kilowatt-hours for the KR 806-3E. On the same construction site, the diesel energy consumption of a KR 806-3GS was 93 kilowatt-hours, see Figure 5. With the same drilling performance, the energy consumption, reduced by a factor of 2.9, was even better than anticipated, as the efficiency of all components was not precisely known when the predictions were made. The construction site personnel found the noticeably lower noise emissions of the drilling rig very pleasant.
Since June 2024, the rig has been in continuous use at another site in The Hague, where micropiles are also being drilled. Here, the rig is powered via an on-site power connection. The average consumption of electrical energy per operating hour is 32.6 kilowatt-hours. The operation is running smoothly.
Conclusion and outlook
Following customer orders for further KR 806-3E anchor drilling rigs, the drive concept is currently under revision. Firstly, some electrical components have been discontinued or improved in the meantime and secondly, we have been able to incorporate our own experience. The next generation of the KR 806-3E will be less complex, but more compact and even more powerful.
The road to electrification is long and rocky. KLEMM has taken the first step. It was important to recognize who would help us move ahead and where we were going astray. At the moment, we cannot foresee complete wireless operation under real construction site conditions. Nevertheless, we have come a step closer to our goal of "zero emissions", which for KLEMM translates to reducing carbon dioxide emissions by 55 t per drilling rig annually.
References
[1] Keegan, M. (2021, June 23). The Scandinavian way to zero-carbon construction. BBC. https://www.bbc.com/…
[2] Bauer AG (2024, January 31). Kick-off für zukunftsweisendes Forschungsprojekt zur Entwicklung eines klimaneutralen Antriebs für Spezialtiefbaumaschinen auf Basis eines Brennstoffzellensystems. [Press release of Bauer AG. https://www.bauer.de/…
[3] Wermke, I. (2023, November 10). Deutz AG baut Wasserstoffmotoren für China. Handelsblatt. https://www.handelsblatt.com/…
[4] Borama Drilling Equipment (2023, May). Battery-powered vs. diesel-powered. Piling Canada, issue 3, 2023, 6-13.
Further information, videos and technical data on the KLEMM KR 806-3E can be found here: KLEMM KR 806-3E_Product Information
Author
Dr. Carl B. Hagemeyer
Managing Director
KLEMM Bohrtechnik GmbH
Germany
KLEMM Bohrtechnik is a world-leading specialist for the development of exceptionally high-quality and powerful drilling rigs with total weights of up to 32 tonnes. The special feature: world-leading technologies which make KLEMM drills unrelenting.
As a market pioneer, KLEMM has had a decisive influence on the development of anchor drilling technology over the last five decades. This has lead to a technological advantage from which customers around the world benefit. This is because KLEMM offers a broad range of products and services (drilling devices, hydraulic hammers, rotary drives and drilling equipment) as well as individual solutions so that customers can carry out drilling tasks as best as possible with regard to time required, efficiency, reliability and safety.
KLEMM Bohrtechnik GmbH
Wintersohler Str. 5
57489 Drolshagen
Telefon: +49 (2761) 705-0
https://www.klemm.de
Marketing / PR
Telefon: +49 (2761) 705-101
E-Mail: jutta.clemens@klemm.de

