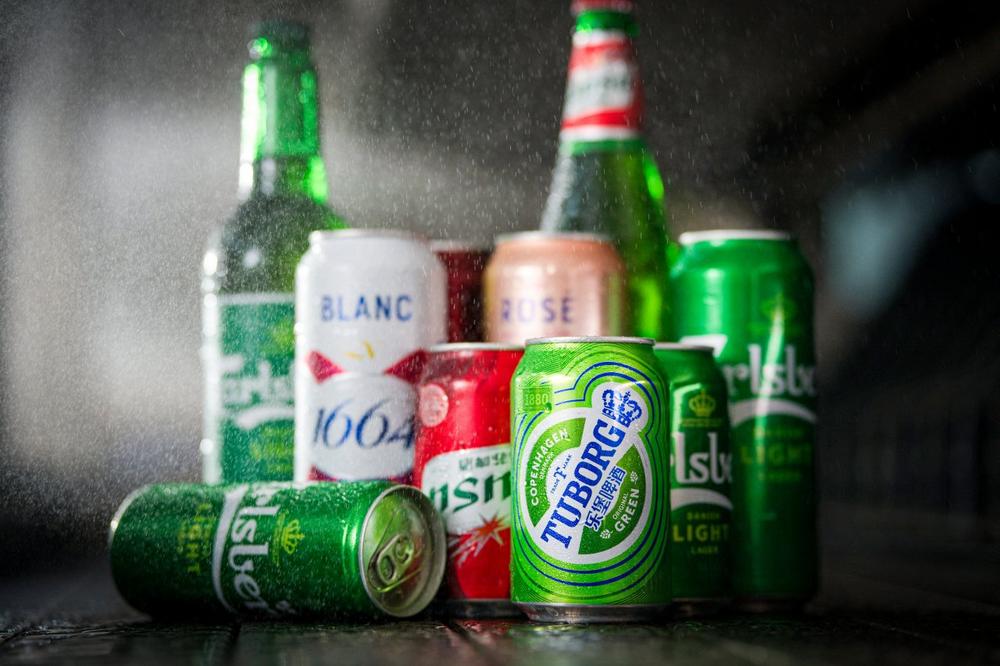
Flagship brewery
Carlsberg and KHS in Asia have been working together in partnership for a long time. Looking back on the two companies’ close and extremely productive cooperation, global key account manager Norman Gras says, “Over the past ten years, we’ve successfully managed lots of projects together, especially in China.” Most recently in 2021, KHS realized two canning lines with a respective output of up to 90,000 containers per hour in Dali (Yunnan Province) and in Yibin (Sichuan Province). The lines were installed and commissioned under the difficult conditions then imposed by the corona pandemic. Gras is thus all the prouder of the fact that the work on this project was extremely efficient and produced a very good result. “On acceptance we had a line efficiency of 99% and 100% – even before the agreed deadline.”
One team instead of customer and supplier
Paul Kime, senior assets, projects and utilities director at Carlsberg Asia, describes the companies’ recipe for success as follows: “Norman and I have worked closely together for years. The same applies to the many employees who implement our projects. This naturally builds up trust. Through our many joint projects, we’ve always been able to significantly improve on the way we work and better the processes on both sides. We all see ourselves as a team with a common goal rather than two separate companies engaged in a traditional customer/supplier relationship.”
The latest joint undertaking is also one of the biggest to date: in the South Chinese metropolis of Foshan, since 2022 Carlsberg has been working on a greenfield project with an output of five million hectoliters that’s to be expanded to a capacity of 14 million hectoliters in three construction stages. New buildings with a total area of about 80,000 square meters have been erected on a plot measuring 16 hectares. At this first phase, the group has invested €191 million to date in what’s now its 27th brewery in the People’s Republic.
Sustainability target: zero emissions by 2040
When it comes to modern, smart and green production, the new plant is a flagship. “The entire project was planned and implemented according to our extensive ESG plan, Together Towards Net Zero and Beyond,” stresses Kime. With this, Carlsberg China wants to achieve net zero emissions throughout its entire value chain by 2040. “In addition to innovative technology, we’ve thus focused primarily on measures designed to boost sustainability. This includes our concept of the ‘sponge brewery’: with this, we collect and treat the abundant amount of rainfall we get in this region in order to conserve our water resources and minimize wastewater.”
What’s more, recyclable and energy-efficient building materials are being used. This complies with the national 3-Star rating system for especially ecological construction.
The new site also generates up to 30% of the electricity it needs from a photovoltaic system on the factory roof. Finally, with the help of an intelligent monitoring and management system the brewery controls and regulates its entire energy consumption. In doing so, the company cuts its energy use and also reduces its impact on the environment.
Innovative technology
Once again, Kime is relying on KHS as his technology partner. “The high quality of KHS lines and machines and efficient project management have become key deciding factors for us over the last few years.” It’s hardly surprising, then, that the Dortmund systems provider has been charged with delivering all of the filling and packaging technology for the new brewery. This consists of four turnkey lines in total.
A keg line fills up to 90 20- to 30-liter kegs with beer per hour. These are primarily destined for export to the Special Administrative Regions of Hong Kong and Macau as well as to Southern China where there’s a particularly high number of catering outlets and bars. Besides the Innokeg CombiKeg for interior and exterior keg washing and racking, the new line also features up-to-the-minute KHS palletizing technology: the Innopal RK articulated robot not only palletizes and depalletizes but also conveys empty kegs to a decapper and full kegs to a cap applicator for the fittings. At further points accessed by the robot, product data labels are attached to these caps and the best-before date printed on the keg shoulder.
Two returnable glass lines yield an output of up to 48,000 bottles per hour apiece. One of these is configured as a combined line that also processes non-returnable bottles in a total of 13 different formats. For this reason, this line is equipped with a rinser/filler/closure block in addition to the high-performance Innoclean DM double-end bottle washing machine.
As opposed to the used returnable empties, new glass bottles are fed past the bottle washer and just given a brief blowout with sterile air in the rinser. This procedure takes up far less water and is thus in full keeping with Carlsberg’s sustainability strategy.
The KHS Innofill Glass DRS ECO filler forms the heart of the block that sets standards with its minimum oxygen pickup and low CO2 consumption. Moreover, fully-automatic probe adjustment, CIP caps and clamp grippers make for minimal setup times. Sealed with ring-pull tops or crown corks, the containers are then discharged from the block to a further highlight of the combined line: the Innopack PPZ packaging all-rounder in the high-capacity range. The change parts required for setting up the various formats are removed from the magazines and exchanged fully automatically without any operator intervention being necessary – a further module aimed at facilitating the shortest possible changeovers without involvement of personnel.
Like the machinery installed in Dali and Yibin in 2021, the KHS canning line is designed to process up to 90,000 containers per hour. In addition to the level of hygiene and degree of flexibility on the Innofill Can DVD, this filler is convincing primarily because of its highly effective oxygen control. This is the key to high-quality beer. The patented CO2 purging process is responsible for this; compared to the conventional method, this lowers oxygen pickup in the beverage can by up to 90%. This procedure also consumes far less carbon dioxide.
Benchmark for the entire brewery group
During the practical implementation of the lines, Kime was especially impressed by the speed of commissioning – such as for the canning line, for instance. “Within just eight days of actual work time, we brought the line up to a performance rate of 98.5%. This means that it’s only down for a few minutes during an eight-hour shift. There’s not yet been anything like this throughout the entire Carlsberg Group.”
For him, this success is the result of a trusting cooperation. Gras agrees. “Over the years, we’ve constantly improved our level of quality and professionalism and have set new benchmarks with respect to communication and our manner of work.”
Strong team on site
This also applies to local KHS personnel who have long managed installations fully independently, Gras is keen to point out. And Kime adds, “China’s proverbial strong work ethic runs through the entire team and binds us all together.” This makes even the most ambitious targets feasible, the manager believes.
Affluent target group
The new brewing complex on the delta of the Perl River is to supply China’s economically best-developed province of Guangdong and the entire South China region with beer. Around 150 million people live here, most of them young and with a comparatively high purchasing power. The range includes six international premium products such as Carlsberg, Tuborg and Grimbergen and six strong local brands, among them Wusu, Chongqing and Xixia.
The KHS Group is one of the world’s leading manufacturers of filling and packaging systems for the beverage and liquid food industries. Besides the parent company (KHS GmbH) the group includes various subsidiaries outside Germany, with production sites in Ahmedabad (India), Waukesha (USA), Zinacantepec (Mexico), São Paulo (Brazil) and Kunshan (China). It also operates numerous sales and service centers worldwide. KHS manufactures modern filling and packaging systems for the high-capacity range at its headquarters in Dortmund, Germany, and at its factories in Bad Kreuznach, Kleve, Worms and Hamburg. The KHS Group is a wholly owned subsidiary of the SDAX-listed Salzgitter AG corporation. In 2023 the KHS Group and its 5,400 employees achieved a turnover of around €1.517 billion.
KHS GmbH
Juchostr. 20
44143 Dortmund
Telefon: +49 (231) 569-0
Telefax: +49 (231) 569-1541
http://www.khs.com
external PR consultant
Telefon: +49 251 6255 6123
E-Mail: presse@khs.com

