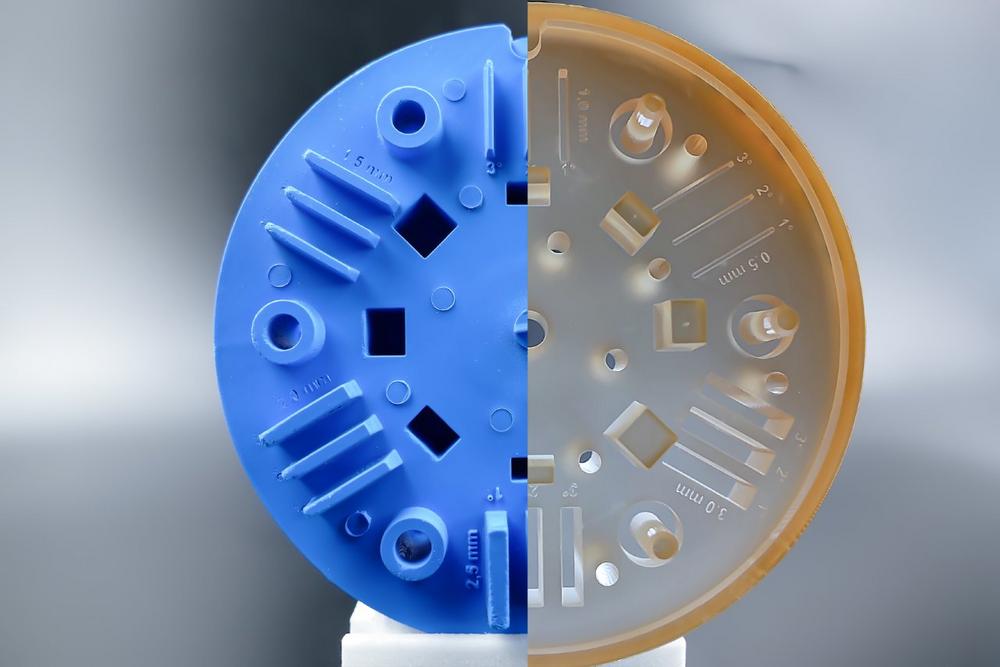
Neues Forschungsprojekt: Flüssigsilikonspritzguss mit additiv gefertigten, harzbasierten Werkzeugeinsätzen
Die Additive Fertigung, auch als 3D-Druck bekannt, ist längst fester Bestandteil der industriellen Produktion und zeigt insbesondere bei der Herstellung komplexer, individualisierter Bauteile ihre Stärken. Dabei können gerade in der Produktentwicklung von Spritzgießbauteilen oder in der Kleinserienproduktion additiv gefertigte harzbasierte Werkzeugeinsätze erhebliche Vorteile bringen. Im Vergleich zu konventionellen Metallwerkzeugen lassen sich nicht nur die Produktionszeiten signifikant verkürzen, sondern auch die Fertigungskosten drastisch senken. Durch diese effiziente Herangehensweise ist es möglich, Kleinserien an Bauteilen aus dem gewünschten Zielwerkstoff wirtschaftlich herzustellen und Produktentwicklungsprozesse mit mehreren Iterationsschleifen flexibel zu gestalten.
Bisher war der Einsatz von additiv gefertigten Werkzeugeinsätzen im Spritzguss jedoch auf Thermoplastverarbeitung beschränkt. Dies führte zu einer erheblichen Einschränkung der Anwendungsmöglichkeiten, da insbesondere Flüssigsilikone, die in vielen Industriezweigen wie der Medizintechnik, Automobilbranche oder Elektrotechnik unverzichtbar sind, nicht ohne klassische Metallwerkzeuge verarbeitet werden konnten. Hier setzt das Forschungsprojekt "ADDmold für LSR" an: Durch die Kombination von additiver Fertigung und Flüssigsilikonverarbeitung soll eine völlig neue Möglichkeit zur Herstellung von Silikonbauteilen geschaffen werden. Die Vorteile der wirtschaftlichen Kleinserienfertigung sowie verkürzte Produktentwicklungszyklen sollen damit künftig auch für LSR-Typen nutzbar sein.
Besonders für industrielle Anwender, darunter insbesondere kleine und mittlere Unternehmen (KMU), eröffnen sich durch diese Innovation weitreichende Potenziale. Durch den Einsatz von additiv gefertigten Werkzeugeinsätzen für LSR können KMU flexibler auf Kundenwünsche reagieren, Entwicklungszeiten reduzieren und sich schneller an veränderte Marktanforderungen anpassen. Dies trägt dazu bei, die Wettbewerbsfähigkeit dieser Unternehmen nachhaltig zu stärken. Zudem entstehen neue Möglichkeiten für maßgeschneiderte Produktlösungen, die bisher aus wirtschaftlichen oder technischen Gründen nicht realisierbar waren.
Dr.-Ing. Ralf-Urs Giesen, Geschäftsführer des UNIpace der Universität Kassel, betont die Bedeutung dieses Forschungsprojekts: "Durch diese völlig neue Herangehensweise an die Silikonverarbeitung können bestehende Unternehmen, die bereits mit Silikonen arbeiten, erheblich von den Vorteilen der Additiven Fertigung profitieren. Die Möglichkeit, schnell und kosteneffizient Werkzeuge zu erstellen, wird die Innovationskraft dieser Branche deutlich steigern."
Alexander Schulmann, Wissenschaftlicher Mitarbeiter Additive Fertigung am SKZ, ergänzt: "Mit diesem Projekt bauen wir unser Know-how im Bereich additiv gefertigter Werkzeuge weiter aus. Wir haben bereits umfassende Erfahrungen mit Thermoplasten gesammelt und sehen nun großes Potenzial darin, die Verarbeitung von Flüssigsilikon auf dieselbe Weise zu revolutionieren."
Interessierte Unternehmen haben die Möglichkeit, aktiv an dem Forschungsprojekt teilzunehmen. Die Projektpartner laden Unternehmen ein, sich kostenfrei am Projektausschuss zu beteiligen. Durch die Mitwirkung können Firmen nicht nur frühzeitig von den Forschungsergebnissen profitieren, sondern auch eigene Anforderungen und Anwendungsfälle in die Entwicklung einbringen.
Das SKZ ist ein Klimaschutzunternehmen und Mitglied der Zuse-Gemeinschaft. Diese ist ein Verbund unabhängiger, industrienaher Forschungseinrichtungen, die das Ziel verfolgen, die Leistungs- und Wettbewerbsfähigkeit der Industrie, insbesondere des Mittelstandes, durch Innovation und Vernetzung zu verbessern.
FSKZ e. V.
Friedrich-Bergius-Ring 22
97076 Würzburg
Telefon: +49 931 4104-0
https://www.skz.de
Presse- und Öffentlichkeitsarbeit
Telefon: +49 931 4104-197
E-Mail: p.lehnfeld@skz.de

