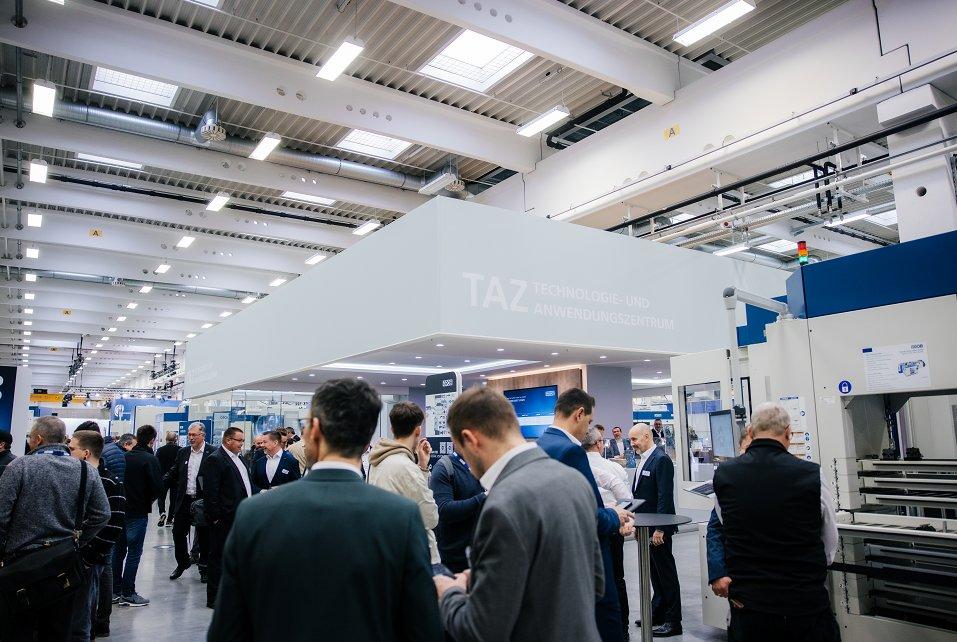
Innovation meets precision: the latest machining and automation technologies will be presented at GROB’s in-house exhibition 2025
Premiere 1: Maximum flexibility with the new Vario rotary table
An absolute highlight of the trade fair is the presentation of the new Vario rotary table on the G550, a special table solution for turbine parts as well as thin, slender parts. "With the Vario rotary table, we are setting new standards in the production of turbine blades of all kinds," explains Sebastian Schön, Head of Application Technology at GROB. "Thanks to the modular design, our customers can choose individually – from the basic module to two highly dynamic, directly driven B-axes." The independent B-axes are equipped with specialized drive configurations to release stresses during roughing and avoid component distortion during finishing. This innovation enables even greater precision in the task. In addition, the Vario rotary table has a movable counter-holder axis designed for different component sizes up to 700 mm blank length. "This allows us to process a wide range of parts flexibly and efficiently," emphasizes Sebastian Schön. Another key feature is the outstanding surface quality, which is achieved thanks to the stable machine design with horizontal spindle and optimized axis drives. "Our customers benefit from an even higher quality standard – even with the most demanding materials and geometries," continues Sebastian Schön.
Premiere 2: New standards in milling-turning tasks
In addition to the Vario rotary table, another innovation is celebrating its premiere: the new milling-turning machine with hydraulic clamping.
"Companies that require efficient production of milled and turned parts in medium to large batch sizes will find this machine the perfect solution," explains Sebastian Schön. The intelligent sensor technology, which ensures maximum process reliability, is particularly noteworthy. This makes production processes even more reliable and user-friendly. Another advantage is the permanent clamping pressure, which is also maintained during turning operations. This leads to consistently high precision and reduces the risk of clamping errors or material deformation. "Safety is our top priority," adds Sebastian Schön. This is why the milling-turning machine has redundant safety interrogations that provide optimum protection for the operator and the machine.
Premiere 3: More pallets. More possibilities. More runtime – the new PSS-R900
Another highlight of the in-house exhibition is the premiere of the new PSS-R900 rotary pallet storage system. This innovative solution was developed to significantly increase productivity and efficiency in production. "With the PSS-R900, our customers can further increase their production processes," explains Ralph Birkle, Team Leader Project Planning. "Thanks to intelligent job planning and ergonomic machine operation, we ensure continuous production with minimized downtimes."
The system has a number of convincing advantages:
• Maximum productivity through increased output and even more efficient use of machine capacities. • Cost efficiency, as unit costs are reduced through greater automation and process stability. • Optimized production processes that ensure seamless production. • Setup parallel to production to completely avoid machine downtimes.
"The flexible configurability of the PSS-R900 is particularly noteworthy," continues Ralph Birkle. Customers can choose between the integration of one or two machining centers in order to optimally adapt the efficiency of production. In addition, the system enables individual storage layouts with or without pallet tower storage (PTS), depending on the specific requirements of the production environment. The variable pallet capacity allows flexible adjustment between 15 and 32 pallet spaces, so that the system can be easily tailored to different requirements. "With the PSS-R900, our customers are ideally equipped for the challenges of modern production," summarizes Ralph Birkle.
GROB-WERKE GmbH & Co. KG
Industriestr. 4
87719 Mindelheim
Telefon: +49 (8261) 996-0
Telefax: +49 (8261) 996-268
http://www.grob.de
Marketingreferentin
Telefon: +49 (8261) 996-7414
E-Mail: katharina.strohm@grob.de
