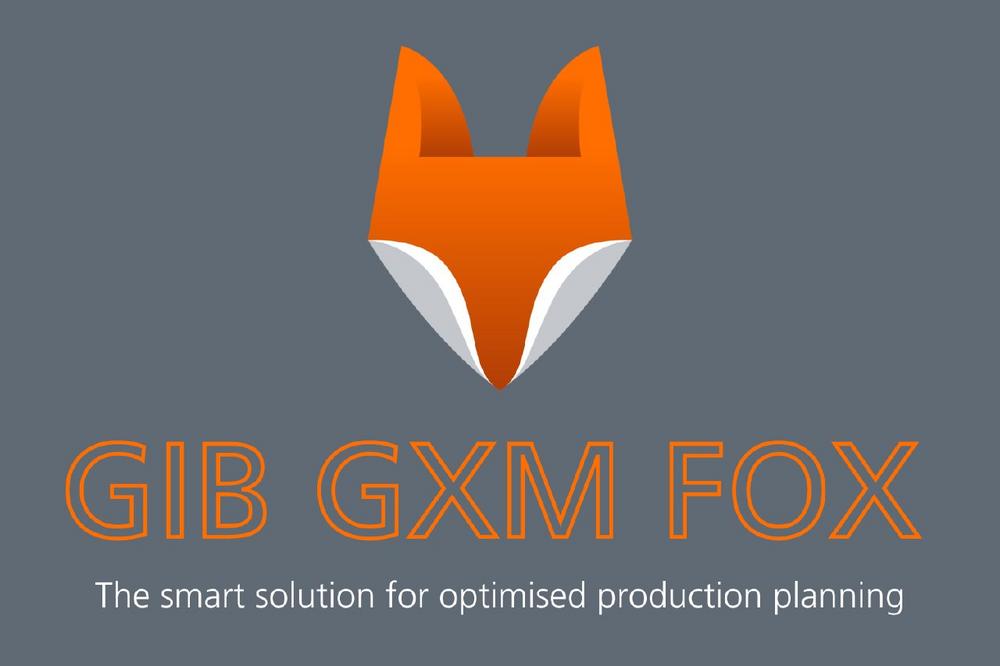
Production planning: The sequence matters
Challenging, but not impossible: multi-work centre planning in production
For practical production sequence planning, in a nutshell, you need all relevant data and an intelligent evaluation of this data. Answered in more detail: A tool is needed that determines for each order,
- which material and/or which parts are needed,
- when the material/parts have to be at which work centre,
- which manufacturing processes are upstream and downstream,
- which rest and buffer times must be observed.
And – this is what makes the task so complex – these data not only have to be collected and correlated for each individual order. Also the order dependencies among each other determine whether production runs or comes to a standstill.
Pegging as relationship manager
Pegging is used to determine complex order structures even in the case of anonymous make-to-stock production. Only this enables optimisation of the entire production across all customer orders. The task is not trivial. It requires that unstructured individual orders become logical and coherent order chains. Complex algorithms check all order dependencies and calculate feasible production sequences. The software constantly determines other possible detailed production plans, compares the quality and offers the user an optimised plan at the end.
The right tool: GIB GXM FOX
This is exactly the task that the software tool GIB GXM FOX takes over. "FOX" stands for Factory Optimisation Excellence and consists of two essential elements,
- the production planning tool with the pegging function and
- the „optimiser“, i.e. the algorithm.
With the help of an intelligent algorithm, the optimiser puts the dependency knowledge extracted from the SAP system, including all determined restrictions, into an optimised sequence. The optimised plan is then imported into the SAP system and all affected orders are rescheduled according to their new sequence. This optimisation process takes place outside the SAP system and can be operated both in the cloud and on-premises.
Conclusion: A tool with high utility value
With GIB GXM FOX, a holistic and comprehensive production sequence planning can be realised that brings high benefits for companies – in many ways. Production is accelerated, stagnations and interruptions are effectively avoided. The waste of precious resources is also prevented.
Further goals and advantages resulting from algorithm-based optimisation in production planning are:
- Ensuring adherence to delivery dates
- Continuous utilisation of existing production capacities
- Shorter lead times
- Reduction of stocks
- Permanent reduction of manufacturing costs
- Increasing the delivery readiness
- Reduction of CO2 emissions
By: Gerald Scheffels for ifm
You can find more information about GIB GXM FOX here.
Would you like to learn more about this topic? Then register now for our SCM symposium ifm SUCCESS DAYS 2023 and attend the presentation "Factory Optimisation Excellence – Optimising inside the supply chain" by Björn Knabe and Dr. Alexander Hoffmann on May 23 from 2:40 – 3:15 pm – on-site in Siegen or digitally.
Measuring, controlling and evaluating – when it comes to pioneering automation and digitalisation technology, the ifm group is the ideal partner. Since its foundation in 1969, ifm has developed, produced and sold sensors, controllers, software and systems for industrial automation and for SAP-based solutions for supply chain management and shop floor integration worldwide. As one of the pioneers of Industry 4.0, ifm develops and implements consistent solutions to digitalise the entire value chain “from sensor to ERP”. Today, the second-generation family-run ifm group has more than 8,700 employees and is one of the worldwide market leaders. The group combines the internationality and innovative strength of a growing group of companies with the flexibility and close customer contact of a medium-sized company.
ifm electronic gmbh
Martinshardt 19
57074 Siegen
Telefon: +49 (271) 23871-4000
Telefax: +49 (271) 23871-4999
http://www.ifm-business-solutions.com
Projektkoordinatorin
Telefon: 0271 238 714141
E-Mail: lena.schneider@ifm.com

