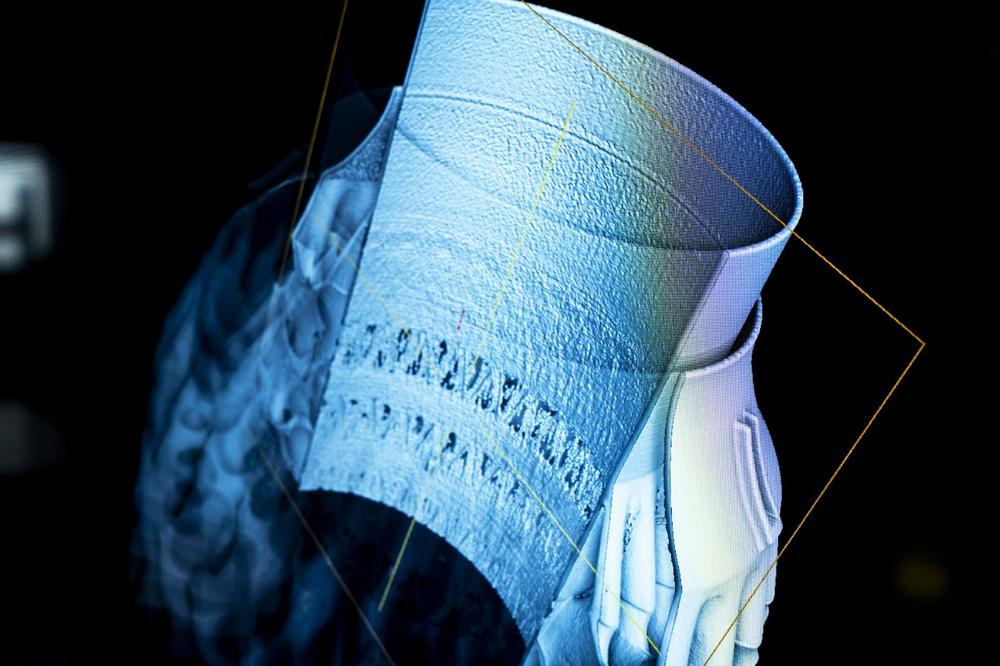
thyssenkrupp Rasselstein is a first mover—using energy-saving technology nominated for the prestigious Deutscher Zukunftspreis
- Use of innovative recuperators in continuous annealing lines
- More efficient preheating of the air means lower energy consumption
- thyssenkrupp Rasselstein—the first worldwide to use the new technology
- Company congratulates Kueppers Solutions for being nominated for the Deutscher Zukunftspreis
An innovative technology for saving energy in industry has been nominated for the Deutscher Zukunftspreis (Award for Innovation in Science and Technology). The new type of recuperators, for which the mechanical engineering company Kueppers Solutions was nominated, have already been installed in one of the heating zones of a continuous annealing furnace of thyssenkrupp Rasselstein—Germany’s only tinplate manufacturer. Plans are already being made to replace other recuperators. This makes thyssenkrupp Rasselstein the first company in the world to use the innovative recuperators in its production and has resulted in energy savings and accompanying reductions in CO2 emissions. The Deutscher Zukunftspreis, which will be awarded by Federal President Frank-Walter Steinmeier in Berlin on November 22, is considered very prestigious and carries a prize money of 250,000 euro.
Innovative recuperators mean lower energy consumption
“Recuperators are heat exchangers that use warm exhaust gas to preheat the air for the combustion of natural gas in order to achieve greater efficiency. Last November, we started replacing plug-in recuperators in our continuous annealing line 3 with the innovative components,” explains Oliver Hoffmann, CTO of thyssenkrupp Rasselstein GmbH. “The recuperators for our plant were produced by Kueppers Solutions in an industrial 3D printer. Thanks to their Triple Periodic Minimal Surface (TPMS) structure, they have a larger surface area than the previous parts, enabling them to preheat the air more efficiently.” The more air is heated, the less gas is needed to reach the required temperature in the continuous annealing furnace. “Our plan is to gradually replace more recuperators in this continuous annealing furnace and in a second one in order to achieve even higher energy savings,” states Oliver Hoffmann.
In tinplate production, the strip must be annealed to make it malleable again after cold rolling. There are two methods for this: The batch annealing process and the continuous annealing process. In the latter, the strip is drawn quickly and continuously through an annealing furnace under protective gas. Temperatures of 670 to 750 degrees Celsius are constantly maintained in the line.
Installation of recuperators is part of the decarbonization strategy
Installation of more efficient recuperators is part of the comprehensive, long-term decarbonization strategy of thyssenkrupp Steel, which affects not only iron and steel production, but also all downstream production processes. It is based on thyssenkrupp Steel’s target of being completely climate neutral by 2045 at the latest.
Projects such as installing the innovative recuperators from Kueppers Solutions in the continuous annealing lines are a key component of the sustainability strategy at the Andernach site of Germany’s only tinplate manufacturer: By 2045, the company aims to save around 400,000 tons of CO2 emissions there each year. This is roughly equivalent to the emissions generated within two years by the private natural gas consumers in the surrounding district of Mayen-Koblenz with its 215,000 inhabitants.
“We would like to congratulate Kueppers Solutions on its nomination for the Deutscher Zukunftspreis and the recognition of its innovative technology,” remarks Oliver Hoffmann. “The efficient use of fossil energy sources with the perspective of a transition to sustainable energy sources such as hydrogen are right at the top of thyssenkrupp Rasselstein’s agenda. Which is why we’re even more delighted to be the first company in the world to install this innovative technology from Kueppers Solutions in our production facilities.”
thyssenkrupp Steel Europe AG
Kaiser-Wilhelm-Str. 100
47166 Duisburg
Telefon: +49 (203) 52-0
Telefax: +49 (203) 52-25102
http://www.thyssenkrupp-steel-europe.com
Communications + Market Development
Telefon: +49 (2632) 3097-2265
Fax: +49 (2632) 3097-152265
E-Mail: Nicole.Korb@thyssenkrupp.com

