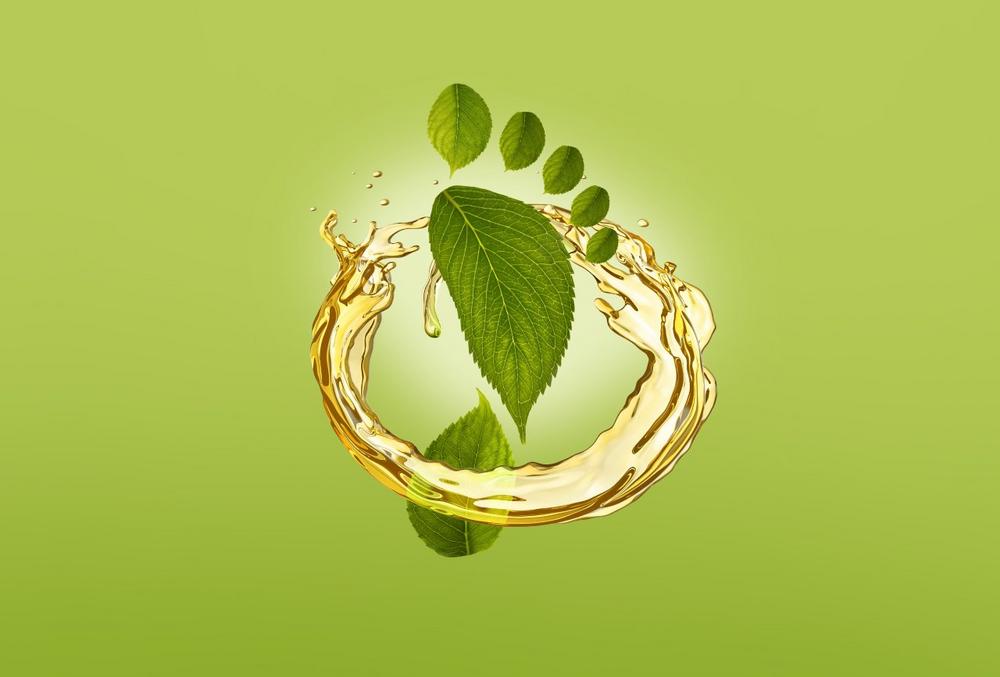
Committed to sustainability: artimelt launches new hot melts
artimelt has a long history of focusing on sustainable production and the careful selection of raw materials. Hot melts can always be regarded as sustainable because they are 100% systems, meaning that the product consists entirely of the adhesive itself. They are solvent-free, with the result that no carrier liquids (which would otherwise increase the volume of the adhesive significantly) need to be transported and dried.
Recyclable hot melts and hot melts that support recycling
Some of artimelt’s adhesive solutions enable and promote recycling processes.
Wash-off: hot melts that can be removed with water
artimeltwashoff forms temporary bonds with good initial adhesion. However, when the adhesive is exposed to alkaline solutions and elevated temperatures, it loses much of its adhesion. It remains on the label without leaving any residue, either on the product that is going to be recycled/reused or in the water.
PET bottles are a typical application for artimeltwashoff adhesives: these are shredded during recycling, allowing the label residues to be subsequently separated from the PET pieces in the sink-float process. During this process, the PET flakes sink to the bottom and the label fragments containing the adhesive float on top, allowing for a clean separation. The recovered PET flakes can then be recycled. As a result, the quality of the recyclate is not affected by the presence of the adhesive and there is no intensification of any downcycling.
Wash-off properties are just as important in the context of reusable glass bottles. In this case, all the bottles are washed and refilled. In reuse processes such as this one, it is absolutely essential to remove the label and adhesive without leaving any residue behind.
Recyclable: recyclable hot melts
Under the name “artimeltrecyclable”, artimelt develops recyclable hot melt adhesives for a wide range of industries based on customer specifications. Some of these hot melts are made from raw materials that are as similar as possible to the actual recyclable product, meaning that they can be co-recycled in the same process. Others are made from harmless raw materials, with the result that they do not interfere with the recycling process. Consequently, the adhesive does not impair the quality of the recyclate. Creating a truly recyclable hot melt – in the sense of one that could actually be recovered as an adhesive – remains, by contrast, a remote prospect.
Possible areas of application include packaging and traditional adhesive tapes. However, these kinds of hot melts are also of particular interest in the label production industry. As the adhesives from the artimeltrecyclable series are based on polyolefins, their chemical compatibility makes them ideal for plastic bottle labels that are made from materials in the same polymer group, such as polyethylene (PE) and polypropylene (PP). Examples of use include detergent bottles, soap dispensers and food/cosmetic tins. In light of the above, this is known as the “mono-material approach”.
Other benefits
At appropriate recycling temperatures, polyolefin-based adhesives fuse with the packaging and label material. The fact that olefin packaging and polyolefin-based adhesives can be recycled jointly also makes it possible to reduce the costs of the entire process. Finally, the total amount of energy consumed during recycling can also be lowered, as no additional separation processes are required.
Biobased: it’s all about the raw materials
It is now possible for products to be thoroughly sustainable even when adhesive is involved. Thanks to its artimeltbiobased series, artimelt is able to offer adhesive solutions that set new benchmarks for the industry. Up to 95% of the adhesive consists of genuine biobased raw materials that have undergone the ASTM 8666–22 standard test procedure.
Biobased hot melts
When developing biobased hot melts, the aim is to reduce the proportion of petrochemical raw materials to an absolute minimum. In addition to the existing Ecoline series – an outstanding range of solutions where biobased raw materials already account for up to 95% of the adhesive – artimelt is currently developing hot melt adhesives for further applications. The aim here is to offer a biobased raw material content of 50–70% across the board.
These solutions rely on renewable raw materials which are not in competition with food production: Wood, molasses, certain vegetable oils, etc. The targeted use of renewable raw materials reduces the ecological footprint of these adhesives. And it significantly decreases dependence on fossil raw materials.
artimeltbiobased products offer a level of adhesion comparable to that of conventional adhesives. Areas of application for custom pressure-sensitive or laminating adhesives are found primarily in the labeling and packaging markets. Hot melts from this product line are suitable for paper and film labels; for labeling pouches, bags and packaging solutions made from sustainable materials; and for adding self-adhesive features to plastic products derived from renewable sources.
Solutions for direct or indirect food contact are available; medical applications are another possibility.
Compostability: striding confidently into the future
Thanks to its constant research and innovation, artimelt is already offering biodegradable hot melt adhesives. But the aim is to develop hot melts that can even be composted.
Biodegradable vs. compostable
The distinction between “biodegradable” and “compostable” is often blurred in everyday life. Although both cases involve microorganisms that biodegrade the product concerned, the environments where this happens can vary significantly. A home garden compost container, ordinary soil, fresh or salt water and industrial composting plants all provide completely different conditions in terms of temperature, humidity and oxygen – and therefore also with regard to the microorganisms involved. Therefore, a product that is easily broken down in an industrial composting plant may not be suitable for a garden compost container. And, of course, it should never simply be dumped in the environment.
Current biodegradable hot melt adhesives consist of substances that decompose in an industrial composting environment. The focus here is on reducing waste and the environmental impact of a product featuring this kind of adhesive.
artimelt has already unveiled a laminating adhesive marketed under the name “artimeltdegradable” after subjecting it to a series of successful application tests. In the area of pressure-sensitive adhesives (PSA), artimelt is driving development forward at full speed.
Biodegradable hot melt adhesive solutions are primarily used in the production of environmentally friendly packaging materials, but are also used for labels and food packaging.
With its new sustainable hot melts, artimelt is once again gaining prominence as a pioneer of environmentally friendly corporate governance.
Sustainability at artimelt
The pursuit of sustainable product development encompasses a wide range of aspects, from the selection of the raw materials and the actual production process right through to the application phase and the question of what happens to a product at the end of its life cycle. Since a supplier such as artimelt has no control over the actual application phase of its products, the boundaries of the life cycle assessment (LCA) system must be narrowly defined: the “cradle-to-gate” approach assesses the environmental impact of a product from when the raw materials are extracted up to the point of reaching the factory gate. CO2 equivalents are the key unit of measurement (into which other greenhouse gases are also converted) and the most commonly used metric for this kind of assessment is the product carbon footprint (PCF). In this regard, artimelt has compiled some initial figures for selected products.
The measures implemented by artimelt
- Selection of raw materials: renewable raw materials are prioritized and the proportion of petrochemical substances is being consistently reduced.
- Material procurement: artimelt requests PCF data from its suppliers to be able to formulate products with a low CO2 footprint.
- Social aspects: as you would expect, artimelt consistently ensures that there is no child labor or similar practices in its procurement supply chains.
- Energy consumption: artimelt sources all of its electricity from sustainable Swiss hydropower. By participating in the program operated by the Energy Agency of the Swiss Private Sector, artimelt is also actively reducing CO2 emissions and optimizing energy efficiency.
- Waste management: waste generated during the manufacturing process is returned to the cycle, reused (in some applications) or disposed of properly.
- Certificate: artimelt is ISO 14001 certified. This standard defines globally recognized requirements for an environmental management system.
- Bronze medal: the assessment by EcoVadis – an independent platform – covers a wide range of criteria, including environmental protection, social responsibility, fair business practices and ethical standards.
- Logistics: artimelt supports its logistics partners as it seeks to make its transport operations CO2 neutral by 2050.
- Processing: artimelt hot melt adhesives are always solvent-free, which means that there is no need to dispose of or recover such substances.
- PCF: it is possible to calculate the footprint of any artimelt adhesive that a customer wants to buy.
The hotmelt specialists.
Active on the market since 1981, since 2016 as an independent company, artimelt has established, continuously expanded and consolidated its position as one of the leading hotmelt specialists. Today, we are a pure hotmelt manufacturer with great development power and have concentrated, in-depth knowledge. Our pronounced development strength and our range of customer-specific solutions in particular enable unprecedented medical and industrial applications.
Our customers rely on the uncompromising quality that is our trademark.
artimelt AG
Wassermatte 1
CH6210 Sursee
Telefon: +41 (41) 92605-00
Telefax: +41 (41) 92605-29
http://artimelt.com
Project Manager R&D
E-Mail: geoffrey.pockay@artimelt.com