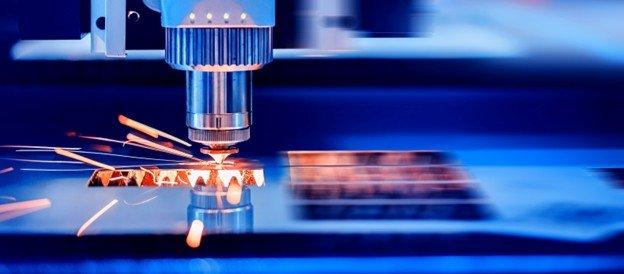
AI-Powered Welding Inspection: Lead Intelligent Equipment Enhances Battery Quality with Precision
About the Customer
The customer is a leading enterprise in new energy, recognized for its robust technical capabilities, large-scale production facilities, extensive customer network, and significant industry influence. Specializing in the R&D, manufacturing, and sales of polymer battery cells for consumer electronics (3C), the customer holds a dominant position domestically and maintains extensive partnerships with internationally recognized brands.
Challenges in Battery Welding Inspection
Ultrasonic welding is a critical technology in battery manufacturing. With increasing demands for diverse battery specifications, manufacturers must quickly adapt welding parameters to meet customer requirements. However, existing inspection methods, primarily relying on In-Process Quality Control (IPQC) spot checks combined with 3σ algorithms, present notable limitations:
- Low Reliability: IPQC inherently carries missed detection risks, leading to unseen traceability and inspection costs.
- High False Alarm Rate: Current 3σ algorithm models are rigid, lack adaptability, and are prone to errors, causing discrepancies in welding quality across different equipment.
LEAD’s AI Welding Inspection Solution and Value
LEAD introduced an AI-driven welding inspection and early warning solution explicitly designed to enhance accuracy, significantly reducing false alarms and missed detections. After extensive trials—five rounds of customer-side pilot verifications covering approximately 150,000 data points—the solution consistently demonstrated superior detection capabilities.
Recognizing the technology’s transformative potential, the customer integrated LEAD’s AI system as an essential component of their production lines, aiming to reduce missed detections completely and lower false alarms to less than 1 ppm.
- Minimal Production Impact: LEAD implemented a customized data acquisition strategy, gathering extensive samples onsite and rigorously analyzing data. Algorithms and models were tailored based on existing customer infrastructure, validated offline, refined through live trials, and seamlessly deployed across the production line.
- Cost Reduction: Following AI deployment, the customer reported 138 fewer false alarms for cathode products on a single line within just 11 days, saving approximately 7.93€ per day. Factoring in a manual inspection time of 10 minutes per product, this equates to a notable 26% reduction in labor costs per line.
- Long-term Capacity Enhancement: The integration of LEAD’s AI welding inspection significantly improved overall production efficiency, reduced manual quality checks, and eased production capacity constraints. The solution demonstrated sustained economic benefits and productivity gains.
The deployment exceeded expectations, achieving a 90% reduction in false alarms and completely eliminating missed detections. The customer praised LEAD’s solution, stating, "The deployment significantly enhanced our production line’s welding inspection quality and efficiency, greatly reducing maintenance downtimes, easing internal pressures, and significantly improving team collaboration and morale."
AI’s effectiveness relies not only on powerful algorithms but also on deep insights into manufacturing processes. LEAD combines extensive industry experience with cutting-edge technologies—including IoT, big data, AI, and edge computing—to deliver precise, efficient, and flexible manufacturing solutions. With over 50 industry-specific applications developed, LEAD continues to empower customers to achieve excellence in lithium battery production through its comprehensive LEADACE Intelligent Platform.
Lead Intelligent Equipment (LEAD) is a leader in intelligent manufacturing, delivering innovative solutions to major players in the automotive, renewable energy, and technology industries. LEAD specializes in eight key areas: lithium-ion EV batteries, EV module and pack equipment, solar PV panels, 3C equipment, hydrogen fuel cells, laser precision processing, connected factories, and smart logistics. LEAD provides customized equipment solutions that integrate seamlessly into clients‘ production processes, reducing costs, maximizing productivity, and enhancing efficiency, quality, and sustainability. With more than 20,000 employees worldwide, 6 manufacturing facilities spanning 1 million m², and over 6,000 R&D engineers across Europe, the USA, and Asia, LEAD is at the forefront of innovation, empowering the energy transition for a sustainable future.
For more information, visit: www.leadintelligent.com/en/
Lead Intelligent Equipment (Deutschland) GmbH
Nordostpark 82
90411 Nürnberg
Telefon: +491621765803
http://www.leadintelligent.com
Marketing Assistant
E-Mail: angeles.haefner@leadintelligent.com