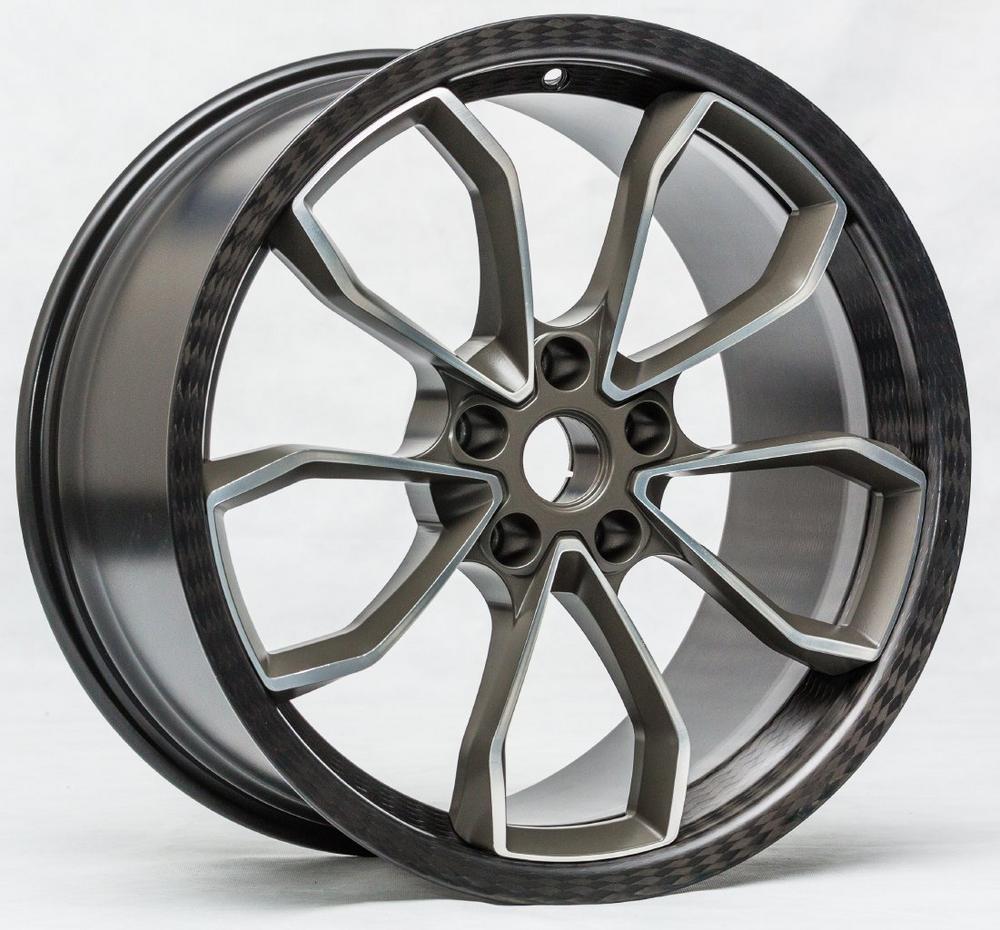
Development of a CFRP aluminium hybrid wheel – a successful cooperation of thyssenkrupp Carbon Components and the Hyundai Motor Europe Technical Center
- 19“ CFRP hybrid wheel with impressive design and significant reduction of unsprung mass
- Development program including sign-off tests completed successfully
Innovation through comprehensive research and development portrays the core of the cooperation initiated by thyssenkrupp Carbon Components and the Hyundai Motor Europe Technical Center (HMETC). The result is nothing less than fully tested 19“CFRP hybrid wheels with an outstanding design. The project was executed using thyssenkrupp’s unique and patented braiding technology when producing the rim well. It is then completed with a forged aluminium wheel centre through a newly developed, extremely robust, yet almost invisible fixing and sealing technology.
The project consisted of eight phases, covering a complete development from the design phase to the final testing on the vehicle. In order to validate the new architecture, the wheels underwent an extensive testing program. In addition to the numerous standard wheel testing procedures, a range of tests specifically addressing the raw material CFRP was executed. HMETC then verified the advantages in performance, efficiency and NVH behaviour (Noise, Vibration, Harshness) on the test rig as well as during tests with real vehicles. The prototype wheels underwent a series of real-life tests, where for example the thermal resistance was tested during a downhill passage at the Großglockner mountain pass. The performance advantages resulted in better acceleration and shorter braking distance as well as reduced tyre rolling noise, which is a clear gain of comfort for the passengers. The development of the CFRP hybrid wheels was successfully completed and HMETC validated the thyssenkrupp technology for unrestricted use for series production.
Dr Jens Werner (CEO, thyssenkrupp Carbon Components): ‘The cooperation with the Hyundai Motor Europe Technical Center has undoubtedly been a success, as we convinced another OEM of the advantages and quality of our braided CFRP wheels. The HMETC constitutes a valuable partner for us, which has validated the quality of our products through comprehensive testing. We are looking forward to the series production of those jointly developed CFRP wheels in the near future.‘
Stephane Ringenbach (Head of Engineering Design, HMETC): ‘The collaboration with thyssenkrupp Carbon Components and the development of the CFRP hybrid wheel were very successful. We fulfil all our specifications while the major weight reduction significantly increases the vehicle performance. We have experienced thyssenkrupp Carbon Components as an excellent partner for new technology development with deep knowledge of composite materials. thyssenkrupp Carbon Components is a supplier which is able to support from early design phase to final product including testing capabilities and quality standards. The direct preforming by braiding – from fibre to rim preform – enables the next level in reduction of composite manufacturing costs. We are looking forward to the next steps to bring these emotional wheels onto the road.’
thyssenkrupp Carbon Components develops and produces carbon wheels for automotive and motorcycle manufacturers and also supplies end customers with motorcycle wheels. The company in Kesselsdorf near Dresden, Germany was founded in 2012.
All carbon wheels by thyssenkrupp Carbon Components are manufactured highly automated with a patented braiding technology on the world’s largest radial braiding machine. Thus, it is possible to achieve the highest quality and lightweight requirements at the same time.
Action Composites GmbH
M
01723 Kesselsdorf
Telefon: +49 (351) 32039-504
Telefax: +49 (351) 32039-513
https://www.action-composites.com
Telefon: +49 (351) 32039530
E-Mail: marketing-carbon-components@thyssenkrupp.com
Telefon: +49 (351) 32039-530
E-Mail: marketing-carbon-components@thyssenkrupp.com

