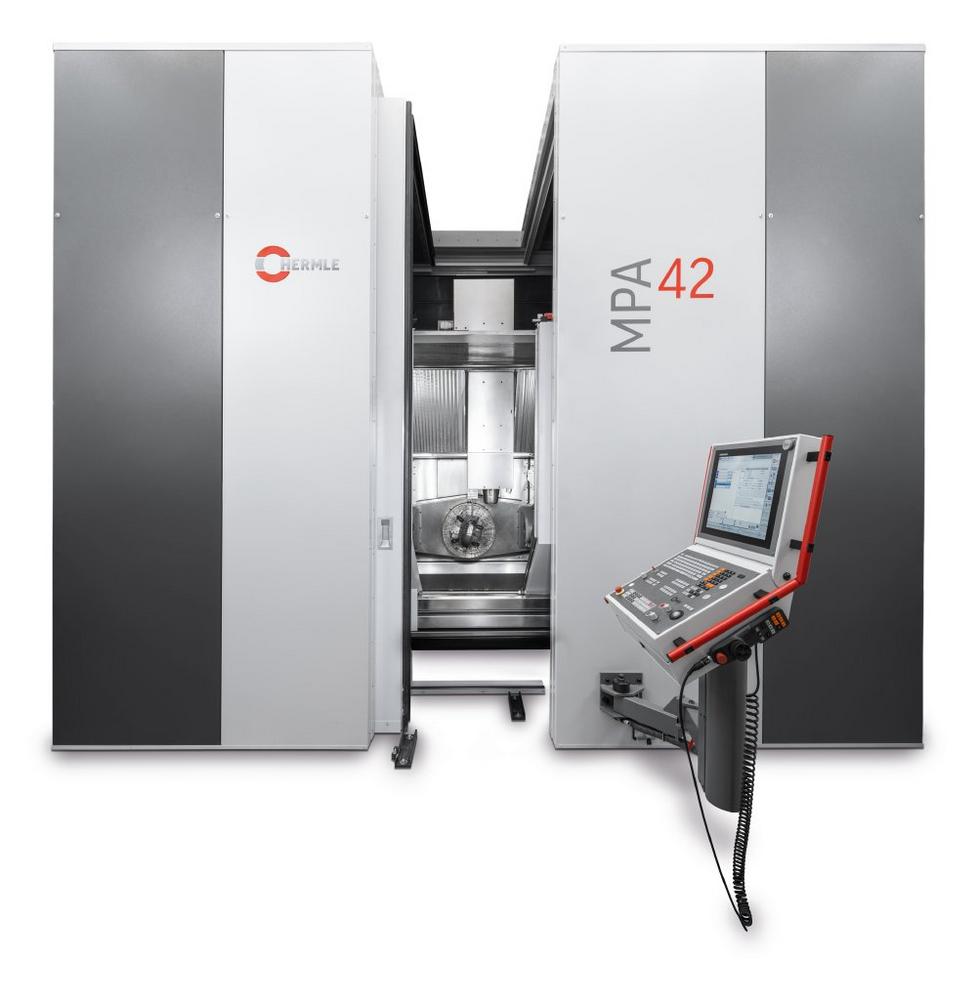
Additiv mit Überschall
Was die neue MPA 42 von Hermle zustande bringt, klingt paradox: Statt mit weniger verlassen die Rohlinge den Arbeitsraum der Zerspanungsmaschine mit deutlich mehr Masse. Wie das funktioniert, verrät das Kürzel „MPA“: Es steht für das Metall-Pulver-Auftrag-Verfahren, welches Hermle vor rund sieben Jahren zur Marktreife gebracht hat. Mit der neuen Maschinengeneration gewinnt der generative Fertigungsprozess deutlich an Präzision und Schnelligkeit.
Die neue MPA 42 steht bei der Hermle Maschinenbau GmbH (HMG) in Ottobrunn. Das hundertprozentige Tochterunternehmen der Maschinenfabrik Berthold Hermle AG agiert seit 2009 vom bayerischen Außenposten aus und hat sich mit den Jahren zu einem Dienstleister für die additive Fertigung entwickelt. Geschäftsführer Rudolf Derntl öffnet die Türen der Schallschutzumhausung der MPA 42, hinter der sich ein stark modifiziertes 5-Achs-Bearbeitungszentrum vom Typ C 42 U versteckt. Neben der Spindel ragt eine Düse in den Arbeitsraum, eine Sprüheinheit für Kühlschmiermittel fehlt dagegen. „Die Lavaldüse beschleunigt das Pulver und schießt es gezielt auf den aufgespannten Metallrohling“, erklärt Derntl.
Überhitzter Wasserdampf und Stickstoff spielen eine ebenso wichtige Rolle wie die Düsengeometrie, damit das Pulver Überschallgeschwindigkeit erreicht und sich durch die Deformation beim Aufprall verbindet. Ein Dampferzeuger und fünf Pulverförderer finden im hinteren Teil der Anlage Platz. Allen Auftragsmaterialien und Rohlingen gleich ist ihre Duktilität: „Es funktionieren sehr viele Metalle, da der Auftrag auf plastischer Verformung basiert. Demnach muss auch die Oberfläche der Halbzeuge duktil sein“, ergänzt der Geschäftsführer. Zum Einsatz kommen in der Regel neben im Werkzeugbau üblichen Warm- und Kaltarbeitsstählen mit hohem Kohlenstoffanteil auch Kupfer und Ampcoloy.
Materialmix für Spritzgussformen
Kupfer leitet die Wärme deutlich schneller ab als die verarbeiteten Werkzeugstähle. Für die Konstruktion von Spritzgussformen hat daher die Materialkombination aus Stahl und Kupfer einen entscheidenden Vorteil: „Mit der additiven Fertigung bringen wir Kupfer an die Stellen des Werkzeuges ein, die für Kühlkanäle keinen Platz haben. Der Kupferkern leitet beim Spritzgießen die Wärme an den nächst gelegenen Kühlkanal deutlich schneller ab als Stahl. Der Anwender spart dadurch wertvolle Sekunden bei der Kühlzeit und die Oberflächenqualität der Kunststoffteile verbessert sich“, führt Derntl aus.
Die fünf Achsen des Bearbeitungszentrums erlauben eine nahezu beliebige Ausrichtung des Pulverstrahls zum Bauteil und sorgen dabei für eine maximale Gestaltungsfreiheit. Kühlkanäle können damit direkt auf den gekrümmten Oberflächen eines Rohlings aufgebaut werden. So erhalten auch größere Spritzgussformen eine konturnahe Kühlung, ohne das gesamte Bauteil additiv aufzubauen. Grenzen setzt lediglich der Arbeitsraum der C 42 U. „Je nach Geometrie liegt das Größenlimit für den additiven Prozess bei je 600 Millimetern in der Länge und Breite. In der Regel sind die Bauteile jedoch kleiner“, erläutert Derntl. Besonders eignet sich die Maschine auch zur Herstellung zylindrischer oder konischer Bauteile wie zum Beispiel gekühlte Vorkammerbuchsen. Durch Materialauftrag bei rotierendem Bauteil werden Taschen und Kanäle effizient gefüllt und mit Werkzeugstahl eingeschlossen.
Neben der Realisierung effizienter Kühlungen bietet das MPA-Verfahren noch weitere interessante Anwendungsmöglichkeiten. Viele Materialien verdichten sich durch den Auftrag derart, dass sich die Bauteiloberflächen problemlos auf Hochglanz polieren lassen. Damit genügt die HMG bei Spritzgussformen selbst höchsten Ansprüchen.
Mit dem MPA-Verfahren können auch Funktionselemente wie Heizdrähte oder Sensoren zur Temperaturüberwachung der Kavität in Stahl oder Kupfer eingebettet und damit in das Werkzeug integriert werden – ideal für eine variotherme Temperaturführung. Doch auch jenseits des Spritzgießens zahlen sich die Möglichkeiten der MPA-Technologie aus. „Bei einer mit integrierten Heizelementen ausgestatteten Leimdüse behalten beispielsweise Klebstoffe über die gesamte Düsenbreite die ideale Verarbeitungstemperatur. Der Sensor im Werkzeug ermöglicht eine echte Regelung“, verdeutlicht Rudolf Derntl.
Das Wissen, wo Materialkombinationen Sinn ergeben, wie Kühlkanäle und Funktionselemente am besten angelegt werden und die Möglichkeit, Formwerkzeuge einteilig zu bauen, ist die Stärke der HMG. „Wir verkaufen keine Maschinen, sondern Know-how“, erklärt der Geschäftsführer. Das Team aus Ottobrunn berät Konstrukteure von Spritzgusswerkzeugen, greift 3D-Modelle auf und optimiert durch Kühlkanal, Funktionselement oder Multimaterial-Kombination die später mit diesem Werkzeug gefertigten Spritzgussteile. „Es geht um reduzierte Taktzeiten und höhere Bauteilqualitäten, die mit anderen Technologien sonst nur schwer zu erreichen sind“, betont Derntl.
Software für Auf- und Abtrag
Mit einer eigenen CAM-Software generieren die Anwendungstechniker den Code für die Maschinensteuerung. Dies beinhaltet nicht nur die Bahnbewegungen, sondern auch die Pulvermengen, bestimmte Temperaturen und den Wechsel zwischen Materialaufbau und Fräsen. „Da kein CAD/CAM-Hersteller den besonderen, alternierenden Prozess – fräsen, auftragen, fräsen – abbilden konnte, haben wir die Software selber geschrieben. Dadurch können wir jederzeit auch auf besondere Kundenwünsche eingehen“, ergänzt der Geschäftsführer. Die Experten sitzen quasi Tür an Tür.
Ist die Vorarbeit abgeschlossen, schickt der Kunde seinen Rohling an die HMG. „Zu 95 Prozent bauen wir auf einem Halbzeug auf, das der Kunde selbst auf seiner Fräsmaschine vorbereiten kann“, erklärt Kundenberater Oliver Müller. So kommt das Bauteil schon mit gefrästen Kühlkanälen oder Taschen für den Kupferauftrag nach Ottobrunn. Hier prüft das HMG-Team den Rohling auf Maßhaltigkeit und schaut, ob die Konstruktionsvorgaben eingehalten wurden. „Zum Beispiel dürfen keine Fasen an den Taschen sein. Für den Pulverauftrag brauchen wir scharfe Kanten“, erklärt Müller.
Nun wird’s heiß
Vor Prozessbeginn kommt das Bauteil in die Heizstation und wird auf circa 300 Grad Celsius gebracht. Denn auch wenn das Material nicht aufgeschweißt wird, geht es nicht ganz ohne Temperatur: sowohl Substrat als auch das Metallpulver müssen für eine bessere Duktilität erhitzt werden. Die Energie zur Beschleunigung des Pulvers kommt aus dem Wasserdampf. Beim Durchgang beider Komponenten durch die Düse erreicht das Pulver die notwendige Überschallgeschwindigkeit. Damit auch während der Bearbeitung die Temperatur konstant bleibt, beheizt die MPA 42 das Bauteil bis zum letzten Spanabtrag. „Wir verhindern so Temperaturgradienten, die Spannungen, Risse oder Verzug bedeuten“, verdeutlicht Rudolf Derntl.
Im Fertigungsprozess wird abwechselnd Material aufgetragen und zerspant. Nach dem Pulverauftrag werden Details wie feine Rippen in das neue Material gefräst, Kühlkanäle werden mit einem wasserlöslichen, metallenen Material gefüllt und per MPA-Auftrag wieder mit einer Stahlschicht verschlossen. „Das Füllmaterial können wir später im Wasserbad ausspülen und erhalten so die gewünschten Hohlräume“, erklärt Müller. Mit dem Pulverstrahl werden Aufbauraten von 200 bis 400 Kubikzentimeter pro Stunde erreicht, bei Kupfer sind nahezu 1.000 Kubikzentimeter möglich.
„Mit der neuen Maschine sind wir up to date und heben unsere MPA-Technologie auf eine neue Leistungsstufe. Sie ist das Herz unseres Dienstleistungsangebots“, betont der Geschäftsführer. Ihm ist es wichtig, alle Prozesse inhouse abzubilden – von der Beratung, Optimierung und Machbarkeitsprüfung über die Werkstoff-Untersuchung bis hin zum finalen Qualitätscheck. „Damit sind wir agil und schützen unser Know-how und das unserer Kunden.“
Die Hermle Maschinenbau GmbH am Standort Ottobrunn bei München ist ein Tochterunternehmen der Maschinenfabrik Berthold Hermle AG. Der Unternehmensschwerpunkt: Grundlagenforschung und Entwicklung von neuen Technologien auf dem Gebiet der generativen Fertigung. Seit mehreren Jahren bieten wir zudem umfangreiche Fertigungskapazitäten an, mit denen wir die Herstellung großvolumiger Bauteile im patentierten MPA-Verfahren exklusiv für Hermle Kunden realisieren.
Die Hermle Maschinenbau GmbH am Standort Ottobrunn bei München ist ein Tochterunternehmen der Maschinenfabrik Berthold Hermle AG. Der Unternehmensschwerpunkt: Grundlagenforschung und Entwicklung von neuen Technologien auf dem Gebiet der generativen Fertigung. Seit mehreren Jahren bieten wir zudem umfangreiche Fertigungskapazitäten an, mit denen wir die Herstellung großvolumiger Bauteile im patentierten MPA-Verfahren exklusiv für Hermle Kunden realisieren.
Maschinenfabrik Berthold HERMLE AG
Industriestraße 8-12
78559 Gosheim
Telefon: +49 (7426) 95-0
http://www.hermle.de
Marketingleiter
Telefon: +49 (7426) 95-0
Fax: +49 (7426) 95-6110
E-Mail: marketing@hermle.de
