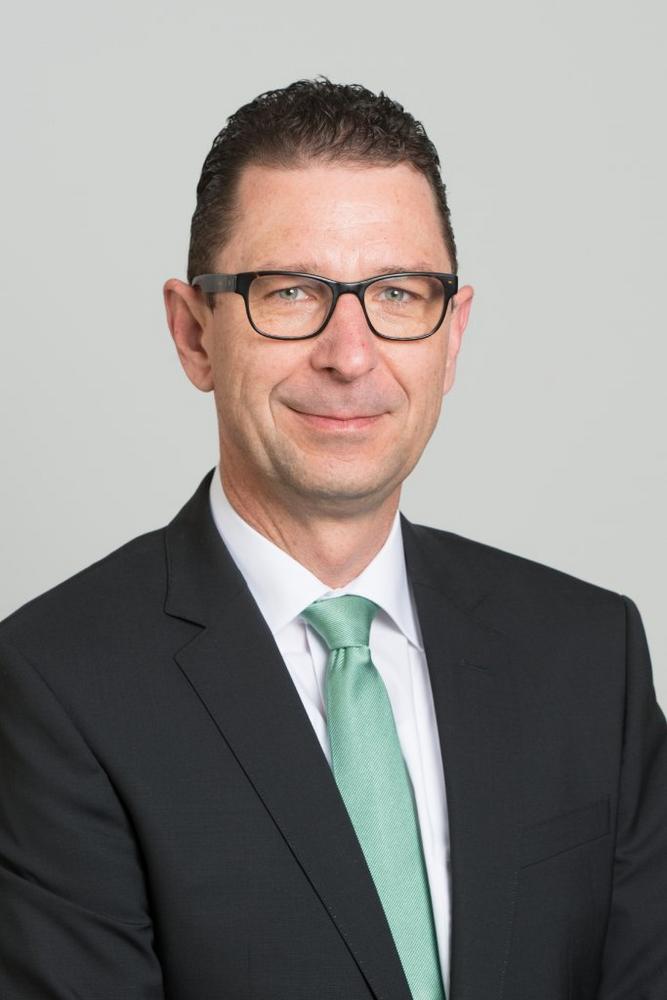
Schaeffler technology improves machine tool efficiency and precision
- Automation is driving demand for integrated system solutions
- Users are increasingly moving to machine tools that integrate multiple machining technologies
- Digitalization improves machine uptime and boosts the efficiency of production processes
Global automotive and industrial supplier Schaeffler will be showcasing its latest innovations for the machine tool manufacturing industry at EMO 2021. There is a lot happening in the industry, as Marcus Eisenhuth, head of Industrial, Europe, explains. “There are currently two key trends affecting users and manufacturers of machine tools and metal machining centers: the growing use of ancillary automation solutions to enhance machine tool efficiency, and the increasing integration of multiple production processes within machine tools themselves. Schaeffler is constantly developing and refining its portfolio of products and services for machine tools so as to offer its customers optimized solutions as they engage with these trends.”
Growth of automation solutions for machine toolsAutomation solutions can help to dramatically reduce the time taken for machine setup and auxiliary processes. Examples of this include the trend towards larger machine tools and the use of handling systems to link multiple independent machines. Manufacturers are also increasingly using articulated-arm robots, which can be mounted on linear axes to perform tasks such as loading and unloading magazines and machine tools. “This market is growing steadily and driving increasing demand for rolling bearings, linear guideways and integrated systems and services. Schaeffler has state-of-the-art products to meet this demand,” said Ralf Moseberg, head of Industrial Automation at Schaeffler.
Combination turning and milling machines are another steady growth area. For the rotary tables used in these highly dynamic machining centers, Schaeffler offers one of the best-performing ranges of bearings available, including variants with integrated angle measuring systems and direct drives. Schaeffler rotary table bearings differ from competitor brands in several respects, most notably their much higher tilting rigidity (up to 30 percent) and very low friction values. For machine manufacturers, this increases rotary table rigidity and speed and reduces thermal influences. End users of these machines benefit from enhanced machining performance, faster cycle times, and improved accuracy and surface finishes.
Growing use of multi-function machine tools
Machine tools that comprise multiple functions or machining technologies are a highly attractive proposition from a TCO standpoint, but they present greater challenges in terms of the rolling bearings needed for spindles, feed drives and linear axes. “They require rolling bearings that are resistant to contamination by hard particles and have reliable, low-friction sealing systems that can be adapted for the various machining processes involved,” said Moseberg. “At EMO 2021, Schaeffler will be presenting its latest solutions to these challenges, including products that incorporate our RUE-F next-generation linear recirculating roller bearing and guideway assemblies.”
The RUE-F assemblies have been engineered to use significantly less lubricant, which lowers their operating costs as well as protecting the environment. This in turn reduces the costs associated with lubricant contamination, particularly in machines that use cooling lubricants. In addition, the improved kinematics of the return geometry in these assemblies enables the machine tool to produce much better surface finishes.
Digitalization for machine monitoring and increased uptime
Schaeffler offers a range of products that are significantly less complex and less expensive than conventional machine tool monitoring solutions. Schaeffler SpindleSense, for example, is a system that measures main spindle displacement, allowing main spindles to be operated safely at maximum load. Schaeffler DuraSense, a monitoring solution for feed axes, ensures precise lubrication according to actual requirements and enables analysis of machine states, thereby preventing unscheduled downtime and increasing plant availability.
Users can retrofit their existing machinery with DuraSense functionality simply by installing DuraSense sensors on the carriage in the monorail guidance system. This is an ideal, low-cost way to digitalize existing plant and machinery so as to benefit from increased uptime and productivity.
Schaeffler also offers an extensive portfolio of condition monitoring and relubrication systems that provide operators of machines and entire manufacturing facilities with a reliable and cost-effective means of monitoring and automatically relubricating standard machines and drives as well as machine tools. Schaeffler itself uses these kinds of solutions in its own manufacturing processes, for example to monitor high-load grinding spindles in grinding machines.
Here you can find all press releases from Schaeffler on the occasion of EMO 2021:
EMO 2021 Presskit
Schaeffler Group – We pioneer motion
As a leading global supplier to the automotive and industrial sectors, the Schaeffler Group has been driving forward groundbreaking developments in the fields of motion and mobility for more than 70 years. With innovative technologies, products and services for CO₂-efficient drives, electric mobility, Industry 4.0, digitalization, and renewable energies, the company is a reliable partner for making motion and mobility more efficient, intelligent, and sustainable. The technology company manufactures high-precision components and systems for powertrain and chassis applications as well as rolling and plain bearing solutions for a large number of industrial applications. The Schaeffler Group generated sales of approximately EUR 12.6 billion in 2020. With around 83,900 employees, Schaeffler is one of the world’s largest family companies. With more than 1,900 patent applications in 2020, Schaeffler is Germany’s second most innovative company according to the DPMA (German Patent and Trademark Office).
Schaeffler AG
Industriestraße 1-3
91074 Herzogenaurach
Telefon: +49 (9132) 82-0
Telefax: +49 (9132) 82-3584
http://www.schaeffler-group.com
Head of Communications Industrial
Telefon: +49 (9721) 91-3934
E-Mail: bulutyrs@schaeffler.com
Unternehmenskommunikation Future Trends
Telefon: +49 (9721) 91-5125
E-Mail: johanna.katzenberger@schaeffler.com

