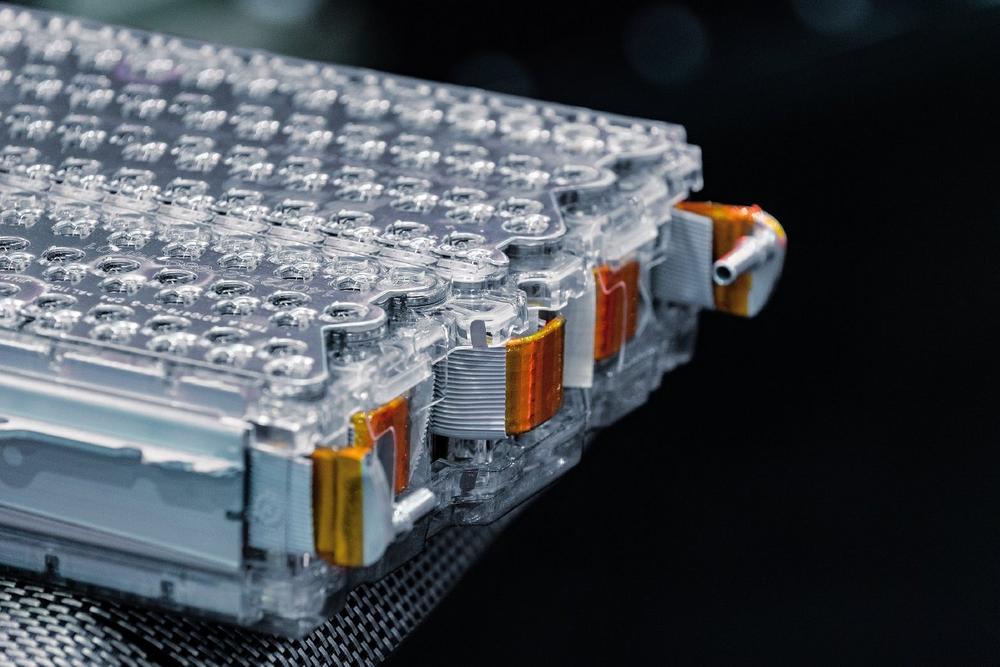
Snow jet cleaning in battery production
Whether it is an electrically powered vehicle or a stationary energy storage device, lithium-ion batteries account for a substantial part of the added value. Their manufacture has brought about a number of new and modified tasks for parts cleaning.
CO2 snow – dry, effective and climate neutral
For these tasks, at this year’s parts2clean, acp systems AG will be showcasing its quattroClean snow blasting technology, a dry, effective and comparatively inexpensive cleaning solution which is easily integrated into automated battery and fuel cell production facilities. The technology makes it possible to remove not only particulate contamination right down to the submicrometer range but also filmic-chemical contamination from partial or entire surfaces in a reliable and reproducible manner. The cleaning medium is liquid, non-corrosive carbon dioxide produced as a by-product from chemical processes and from the generation of energy from biomass and therefore climate neutral.
The process is already being used in various applications for mass producing lithium-ion batteries. These include cleaning the contact surfaces of battery cells – prismatic, cylindrical (round) or pouch cells – as well as lead frames or the bonding surfaces of printed circuit boards. Since even minimal contamination on joining surfaces can result in an inadequate contact, it is essential that particulate and filmic contamination is removed in order to ensure performance and safety.
The dry process is also used to manufacture hydrogen-atmospheric oxygen fuel cells. For example, it is implemented to clean bipolar plates made of stainless steel alloys after laser processing. This leaves spatter residues on the surfaces, which impair efficiency and must therefore be fully removed. The dry and residue-free cleaning technology is also deployed to clean particulate and filmic contamination from pre-processes such as punching.
The excellent cleaning results obtained with the quattroClean system are thanks to the special design of the wear-free dual-substance ring nozzle. Liquid carbon dioxide passes through the nozzle and expands on exiting to form fine CO2 crystals. These are then bundled by a separate jacket jet of compressed air and accelerated to supersonic speed. The jet is easy to focus on a specific area. On impinging on the cleaning surface, four effective mechanisms (thermal, mechanical, solvent and sublimation) guarantee the reliable removal of contaminants. These are blown away from the surface by the aerodynamic force of the compressed air and expelled from the cleaning module by the integrated suction system. Since the crystalline carbon dioxide sublimates completely during the cleaning step, the treated surfaces/parts are dry and can be fed straightaway to the next step in the production chain.
Flexible integration into the production process
The scalability and compact size of the quattroClean cleaning system means that it can be integrated almost anywhere in an automated battery or fuel cell production line. The process is designed and validated according to customer and application requirements through tests in acp’s technical center. To ensure uniform results, a sensor system monitors the consistency of the jet at each nozzle. The supply of compressed air and CO2 to the nozzles, as well as the blasting time, is also monitored. The values measured are stored automatically and can be transmitted via standard interfaces to a superordinate system to acquire all production data.
acp systems AG at parts2clean: Hall 4, Stand B 04, Messe Stuttgart, 5 to 7 October 2021.
Founded in Stuttgart in 1997, acp systems AG is today one of the international market and technology leaders for efficient CO2 snow jet cleaning. The company’s patented quattroClean technology enables dry, material and resource-saving removal of particulate contaminants and film-type residues from virtually all engineering materials. The dry process also opens up the opportunity to clean electronic and electromechanical components reproducibly. The scalable and Industry 4.0 capable quattroClean process can be easily adapted to different component geometries for full-surface or partial cleaning, e.g. where sealants and adhesives are applied or for welding, bonding, coating or assembly steps. Another core competence of acp is the automation of cleaning processes and their integration into linked production, assembly and coating lines.
acp systems AG
Berblingerstr. 8
71254 Ditzingen
Telefon: +49 (7156) 48014-0
Telefax: +49 (7156) 48014-10
http://www.acp-systems.com
Public Relations
Telefon: +49 (711) 854085

