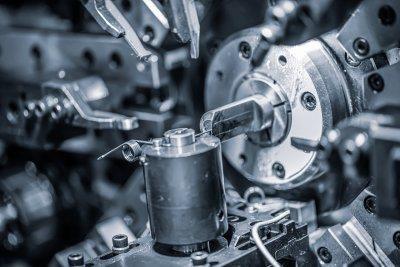
Putting the spring back into manufacturing equipment
While retrofitting sounds attractive, allowing the bulk of the machine to be reused, it is difficult to predict all of the possible challenges that will arise. Furthermore, the retrofitted version of the equipment needs to offer additional advantages, such as flexibility, speed enhancements, and an improved user interface. With around 60 spring formers spread across three manufacturing sites, one recent Delta customer faced precisely this dilemma. However, after close support from Delta’s Field Application Engineer Enric Tamarit and his team, together with a trusted system integrator with mechanical engineering expertise, the customer agreed to trial the retrofitting approach.
At its core, the new design used the AX-864E, a CODESYS-based motion controller that is ideal for such complex control applications. The compact, fan-less design, built around an Intel x86 CPU, ensured robust mounting coupled with support for EtherCAT to control the selected drives. The unit also features an HDMI display port, gigabit LAN, four USB interfaces, and a connector for RS-485/422 and a differential input motor encoder. Eight GPIOs provide NPN (sink) or PNP (source) control or input signals dependent on the model chosen. A watchdog timer, configurable through the BIOS, ensures the system automatically resets in the event of abnormal operation. Additionally, a range of security features, including BIOS passwords and Delta’s PAC Tool for restricting writes to the integrated solid-state drive, are also included. Thanks to its support for CODESYS, an industry-standard IEC 61131-3 PLC language, the control system software was rapidly iterated to optimize the implementation.
The wire forming was realized with ECMA Series servo motors. Their state-of-the-art design provides a high torque-to-size ratio, low flux loss, and delivers low cogging suited to the smooth motion control required for spring manufacture. They could also be adapted to different spring-forming equipment needs thanks to a range of shaft options and encoders. Coupled with ASDA-A2 Series servo drives, connected via high-speed EtherCAT, simultaneous control of the servo motors was ensured. The characteristics needed for the retrofitted design were easily achieved thanks to the available high precision control, with a 1 kHz frequency response and 1 ms settling times, and superlative vibration suppression. Programmable positioning modes (Pr Mode) also allow up to 64 internal position settings, supporting continuous motion control.
An essential aspect of the retrofit was an improved user interface, allowing operators to configure the desired spring from a choice of recipes. With a 7-inch color TFT display, the DOP-H07 Series provided the flexibility needed by machine operators. This IP55 rated handheld device weighs just 750 g and includes an emergency stop button together with a hook for convenient storage when no longer in use. Connected to the AX-864E via a TCP Modbus, the handheld display allows simultaneous configuration of the spring former while overseeing the actions executed by the servos. Delta’s DOPSoft configuration software enables visually appealing, clear, and easy-to-use interfaces in multiple languages, ensuring simplicity for users. Simulation of the production process was also implemented, saving time and resources before committing to manufacturing.
The retrofitted electronic CAM spring former provides a more streamlined operating experience. Switching between the manufacture of different spring types is simplified, thanks to the user-friendly, recipe-style selection offered by the human-machine interface (HMI). Furthermore, new recipes can be easily developed by extending and modifying existing designs as and when required. In operation, the upgraded solution proved to be significantly more efficient. Tooling changes to manufacture a different spring previously required a day of effort. This has been reduced to half a day with the new approach. Furthermore, productivity has been improved by 50% in most cases, while the most straightforward spring designs can now be manufactured at double the previous rate.
Although the initial retrofit has taken around a year of close cooperation and work to complete, the results have been so impressive that the customer has decided to continue upgrading further spring formers. Because a CODESYS-capable motion controller was chosen, coupled with Delta’s easy-to-integrate HMI, servo drives, and servos, this approach will continue to be a cost-effective and reliable alternative to machine replacement.
Delta Electronics (Netherlands) B.V.
Zandsteen 15
NL2132MZ Hoofddorp
Telefon: +31 (20) 8003900
Telefax: +31 (20) 8003999
http://www.delta-emea.com/
Mepax
Telefon: +34 (619) 0277-78
E-Mail: m.depablos@mepax.com
Delta EMEA
Telefon: +31 (20) 65509-06
E-Mail: jwu@deltaww.com
