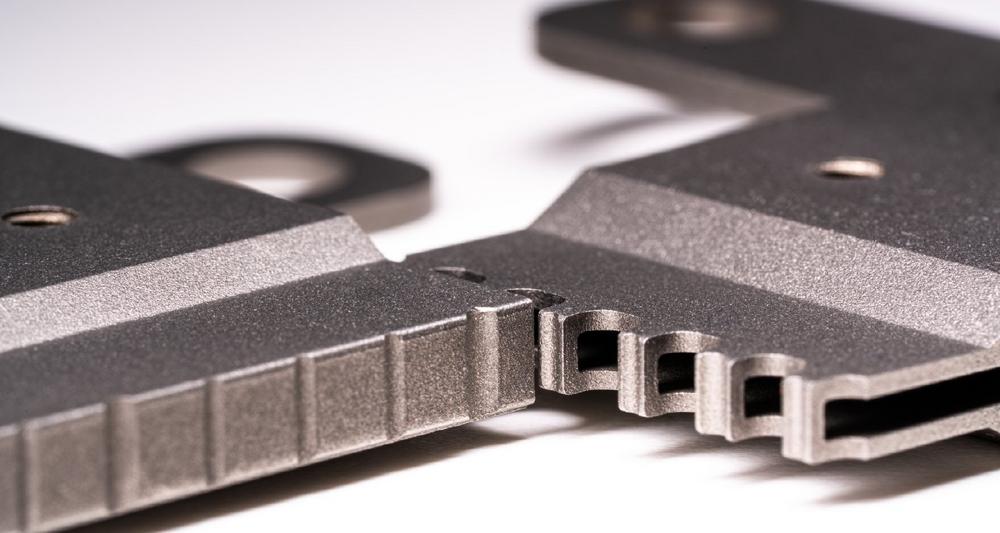
Hochpräzise Thermoden mit beliebiger Geometrie
Präzision ist das A und O beim Bügellöten
Thermoden-Lötanlagen sind in aller Regel sehr robuste Systeme, brauchen wenig Platz, löten energieeffizient und sind für lange Standzeiten bekannt. Damit eignet sich das Verfahren vor allem für Teile, die in hohen Stückzahlen automatisiert gefertigt werden. Das Problem dabei: Die Qualität der Lötstelle hängt direkt von der präzisen geometrischen Form der Thermode ab. Entsprechend liegen die üblichen Genauigkeitsanforderungen bei den seitlichen Schenkeln bei 0,5 ± 0,01 mm (Oberfläche Ra 0,2). Dies ist erforderlich, um später im Lötprozess die Einsinktiefe Mikrometergenau einstellen zu können – und damit das Anschmoren von Kabelisolierungen genauso zu verhindern, wie eine mechanische Beschädigung von Dies (ungehäusten Chips).
Werkstoffbedingte Hürden bei der Thermodenherstellung
Thermoden bestehen in aller Regel aus niedrig gekohlten Legierungen (etwa Wolfram-Kupfer-Werkstoffe), welche sich bei den üblichen Löttemperaturen um die 300 °C nicht verformen und damit – außer der Wärme – auch die erforderlichen Presskräfte (zum Beispiel 60 N auf wenigen Quadratmillimeter Fläche) übertragen können. Das Material ist sehr korrosionsbeständig und verschleißfest. Letzteres ist allerdings ein entscheidender Nachteil für die mechanische Bearbeitung, denn es ist zäh und gleichzeitig ziemlich abrasiv. Der Span nimmt die beim Fräsen entstehende Wärme nicht auf. Bedingt durch diese Materialeigenschaften gibt es folglich immer wieder Friktionsprobleme an den Schneiden der Werkzeuge. Auch mit sehr geringem Vorschub ist es kaum möglich, dem Werkstück eine hochpräzise, wiederholbare Kontur zu geben.
Daher fertigt Sauter nur die Rohlinge mittels CNC-Zerspanung. Um die für das Thermodenlöten erforderlichen hohen Genauigkeiten zu erreichen, wird der Rohling anschließend per Funkenerosion bearbeitet. Die bestehenden Materialeigenschaften führen dabei zu vergleichsweise kurzen Erodierzeiten, was hochkonzentriertes Arbeiten erfordert.
Thermodenlöten – ein Reflow-Verfahren
Das Bügellöten zählt zu den Reflow-Verfahren, bei denen die in einem früheren Prozessschritt aufgebrachte Lotpaste wieder aufgeschmolzen wird, um eine dauerhafte elektrisch leitfähige Verbindung herzustellen. Dazu wird die Thermode aufgeheizt und auf die Lötstelle gedrückt, bis das Lot schmilzt. Anschließend wird die Heizung abgeschaltet. Der Stempel verbleibt aber auf der Lötstelle, bis das Lot erstarrt ist. Erst danach wird der Stempel abgehoben. Daher lassen sich mit diesem Verfahren auch federnde Teile prozesssicher verlöten. Das Thermodenlöten eignet sich auch gut zum Weichlöten von Serienteilen ohne Leiterplatten, wie sie beispielsweise beim Anbringen von Kabeln an Batterieclips vorkommen.
Die Sauter GmbH mit Sitz im schwäbischen Hirrlingen, 15 km südwestlich von Tübingen, wurde 1948 als Gravieranstalt gegründet. Dieses angestammte Geschäftsfeld bedient das Unternehmen noch heute und ist ein in der Region gefragter Hersteller von Schildern und Frontplatten sowie kundenspezifischer Gravuren auf Metall.
Längst aber hat sich der Handwerksbetrieb zum Technologiecenter für Werkzeug- und Formenbau, Funkenerosion und Graviertechnik weiterentwickelt. Das familiengeführte Unternehmen bearbeitet gehärtete Metalle – die sich kaum zerspanen lassen – mikrometergenau mittels Funkenerosion, fertigt Präzisionsteile nach Kundenzeichnung, stellt hochpräzise Kunststoff- Spritzgussformen sowie Umformwerkezuge her. Durch seine hohe Fertigungstiefe kann das Familienunternehmen flexibel auf die Bedarfe und Terminschienen seiner Kunden reagieren. So entsteht schnell der entscheidende Mehrwert.
Weitere Informationen unter: www.formenbau-sauter.de
Sauter GmbH
Weberstraße 17
72145 Hirrlingen
Telefon: +49 (7478) 92790-0
Telefax: +49 (7478) 92790-29
http://www.formenbau-sauter.de/
Telefon: 07478927900
E-Mail: mehrwert@formenbau-sauter.de

