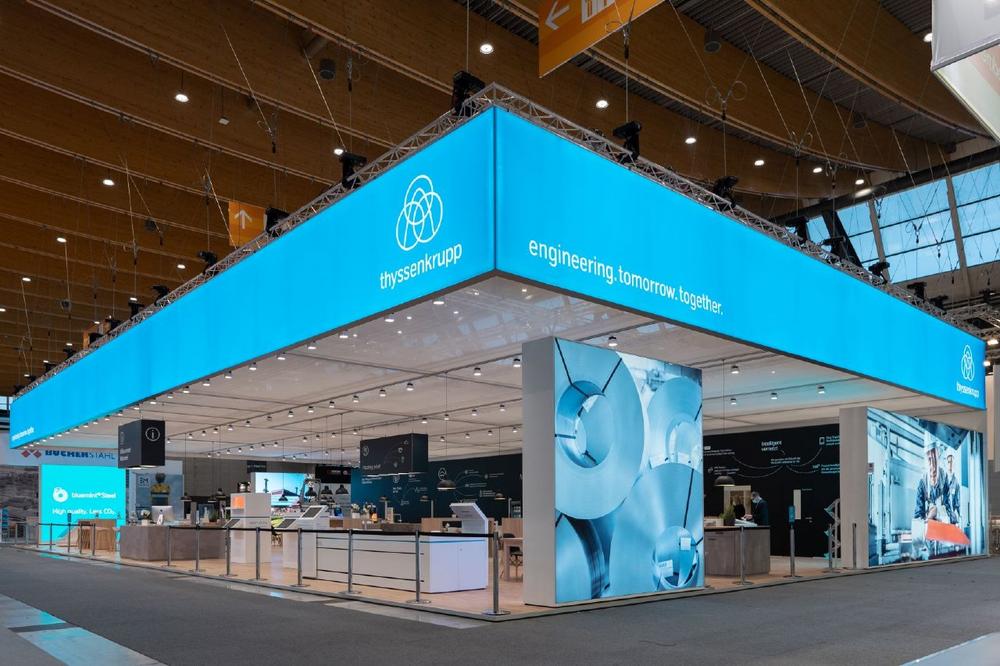
Material of Mobility: thyssenkrupp Steel presents a wide variety of materials solutions for the automotive industry of mobility at Blechexpo 2021
Making sure the voltage is right: Innovative steel solutions for e-mobility
Robust and safe battery housings and car body and chassis components must ensure that electric cars at least match the safety standards of conventional vehicles. A long-standing partner to the automotive industry, thyssenkrupp Steel understands these requirements and offers comprehensive custom materials and technology expertise for modern lightweight design of all crash-relevant structural parts. For example in the form of DP-K® cold-rolled high-strength dual-phase steels, CP-K® cold-rolled complex-phase steels or MBW® high-strength hot forming steels.
Just as important: With more efficient electric motors, the stored energy must be converted into greater range. Non grain oriented electrical steel powercore® Traction is an indispensable core material here. The special steels that control the magnetic flux form the basis for every electric motor.
In the stators and rotors, electrical steel has a decisive impact on the efficiency of the motor: the more it minimizes the core losses, the greater the efficiency of the motor – and thus the range of the vehicle. The alloy has a particular influence on magnetic performance. That’s why the highly pure magnetically soft iron-silicon alloy from thyssenkrupp Steel has a roughly one fifth higher silicon content than for standard applications. Core losses of thyssenkrupp Steel’s powercore® electrical steel are almost 30% lower than those of conventional grades.
Steel is the go-to material for chassis
With the use of proven and new steel grades for modern chassis designs, thyssenkrupp Steel ensures the right material can always be used in the right place – trade visitors are welcome to discover them at Blechexpo 2021. Depending on use and requirements, for pressed chassis parts thyssenkrupp Steel offers two general material groups which will be presented at the trade fair: Hot-rolled multi-phase steels and highly ductile microalloyed steels. For tube applications, e. g. in stabilizers, manganese-boron steels are also available.
Multi-phase steels are ideal for demanding shapes such as those required in chassis applications. This is because the steel displays excellent local forming properties despite its high strength. The most recent new development is the bainitic steel CH-W® 660Y760T. This grade is ideal for cold-formed parts with high hole expansion requirements such as control arms. High-ductility microalloyed fine-grain steels from precidur® hot-rolled precision steel strip produced in Hohenlimburg are also used for demanding chassis parts. Premium materials such as precidur® HSM 700 HD are particularly suitable for the manufacture of parts with complex forming geometries and open up new design options for automotive lightweighting.
With a view to the specific requirements of the automotive industry, Blechexpo 2021 shows that thyssenkrupp Steel drives developments in high-performance steel materials. Examples include perform® 500 HD. This is the first material in the new perform® HD product family aimed specifically at chassis parts or parts with complex shapes. This grade is characterized by guaranteed close mechanical tolerances and good hole expansion characteristics. At the same time, a new alloying concept ensures that forming properties are uniformly improved over the whole coil length. For processors this means lower production costs as a result of lower scrap and reduced downtimes for tool setting during the production process.
A perfect fit: Lightweight design meets safety and comfort
Modern car seat has to be a true all-rounder: it has to be lightweight yet crash-proof, take up very little installation space, be inexpensive to produce – and all of this, of course, without compromising comfort. At this year’s Blechexpo, thyssenkrupp Steel will show how steel helps to meet these diverse requirements. Take the issue of weight, for example: Today, each seat weighs on average around 12.5 kilograms – and that’s just the load-bearing steel seat structures. Together, then, the front and rear seat structures of a car can easily weigh in at around 50 kilos. Cost-effective steel lightweight design has a noticeable positive impact here and helps reduce weight by up to 15 percent – at no extra cost.
Seat structures are a complex system in which every single structural component is important. Take safety: The front seatback is stressed by the passenger in the event of a rear-end crash and by whatever’s on the rear seat or possibly in the trunk in a frontal collision. Accordingly, different crash load cases must be considered for the backrest side member, cushion side member, and seat shell. A task made for our robust uncoated steel DP-K® 440Y780T. This cold-rolled dual-phase steel is not only extremely strong but also easy to form, making it perfect for difficult-to-form structural components that are exposed in the event of a crash, such as the backrest side member.
The possible solutions for front and rear seats offered by innovative steel materials made by thyssenkrupp Steel are as varied and different as customer requirements. Depending on the shape of the component in question, DP-K® 700Y980T or perform® 500 HD can be used, e.g., for the cushion side member – HD stands for “high ductility“ and has particularly good forming properties. The case-hardening and tempered steels and the highly ductile micro-alloyed fine-grain structural steels of the precidur® family, for example, offer hot-rolled precision strip with extremely tight thickness and profile tolerances that is ideally suited to making functional components such as seat back adjusters. In addition, microalloyed, high-strength steels from precision strip in particular are ideally suited for classic cold rolling processes and seat rail applications. Finally, the steel producer offers cold-rolled complex-phase steel CP-K® 780Y980T, another novel high-performance material in the 1,000 MPa strength class that features excellent forming properties and meets the highest thickness tolerance requirements – and not only for seat rails.
thyssenkrupp is looking forward to meeting and discussing in person with customers and business partners at Blechexpo 2021. See us in hall 10, stand 10407, from October 26 through 29, 2021.
thyssenkrupp Steel Europe AG
Kaiser-Wilhelm-Str. 100
47166 Duisburg
Telefon: +49 (203) 52-0
Telefax: +49 (203) 52-25102
http://www.thyssenkrupp-steel-europe.com
External Communications
Telefon: +49 (203) 52-47270
E-Mail: christine.launert@thyssenkrupp.com

