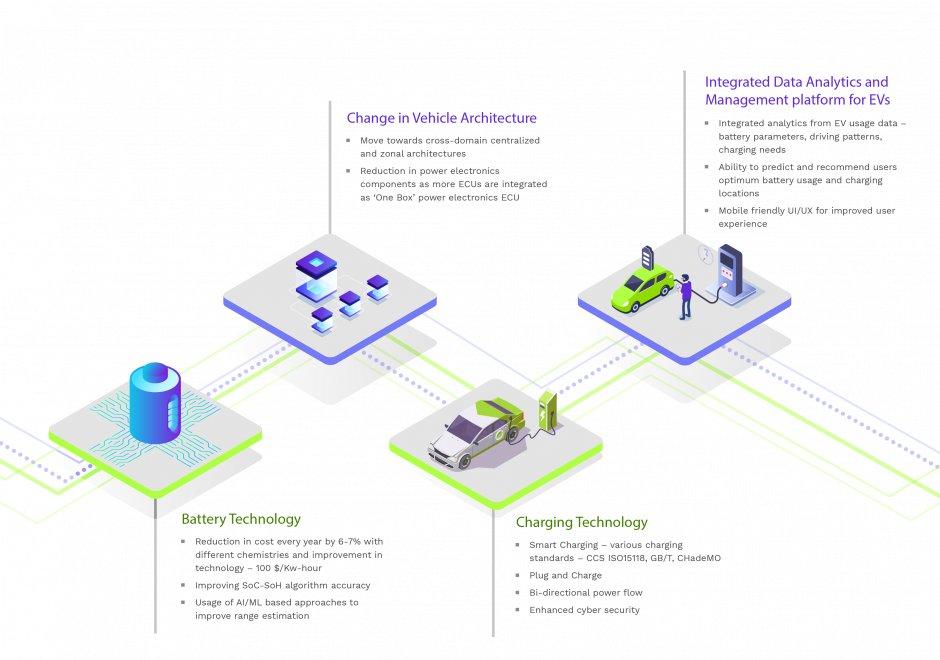
Electrification: Transforming Mobility of the Future
Such statistics are driven as much by exogenous factors – climate change, stringent global CO2 regulations, fast-depleting fossil fuels, and shifting demand for more sustainable products – as by innovations in Battery and Charging Technologies, integration of Power Electronics, along with the emergence of Data Analytics. Here’s how.
Technology drivers for electrification
Figure 1 above depicts major technology trends indicating a possible increase in adoption:
- Battery technology: Batteries today are the most prohibitive component of EVs. But efficient and intuitive Battery Management System (BMS) solutions with AI and advanced estimation methods to ensure accurate and reliable data on the battery state for an enhanced BMS performance may help reduce overall costs of the batteries and improve the performance of the electric vehicles.
- Charging technology: Intelligent charging platforms can go a long way in reducing project costs and adopting EVs with increased customer satisfaction. The vehicle can act as an energy provider in remote locations where regular electricity is not available, use cases like Vehicle to Home (V2H) enabling bi-directional power flow.
- Change in vehicle architecture: A big challenge for EV architects is to reduce the number and complexity of interfaces to a minimum. That’s where integration of EV components is the key. Every OEM is focusing on the domain controller and would move to zonal controller-based architecture to minimize the interfaces and separate hardware from software.
- Integrated data analytics and management platform for EVs: Data collation and analyses are rampant across sectors, including automotive. Data enables more accurate predictive maintenance, especially for the state of health (SoH) and state of charge (SoC) of the battery, driving insights into buyers’ profiles and customizing and enhancing services for them. It also indicates the life of the vehicle, its usage patterns, suggests optimal locations for installing charging stations and OEMs, and improves understanding of how to derive maximum value from vehicles and drive-up revenues.
But this is easier said than done unless technologies are leveraged optimally as below:
Innovations in battery technology for enhanced performance
Enhance range estimation (AI/ML-based): While EV registrations had grown 43% y- o-y in 2020, range anxiety and high charging time have proved as dampeners. Seeing how lithium-ion batteries in EVs charge slowly, many charging methods are employed to zero in on options. Predictive analytics and data intelligence enable to improve the performance of battery packs by predicting battery life, identifying potential degradation/breakdown and their causes and, fixing delays/errors even before they arise. Such intelligent gathering and monitoring of extensive data on battery life, performance, state-of-charge, temperature, number of charge cycles, etc., stored on the cloud drive innovation.
Enable cloud-based predictive analytics: Electrification-driven transport highlights why an efficient BMS which ensures maximum performance, safe operation, and an optimal life span under diverse charge conditions is required. Accurate and precise SoC/SoH estimations help evaluate the reliability of the battery while providing critical information, remaining energy, and Remaining Useful Time (RUL). AI-enabled predictions are more accurate, and the benefits are automatically incorporated in the decision-making.
Move towards integrated power electronics ‘one-box’ for energy efficiency and lowered BOM overheads
Millions of lines of code will power vehicles of the future. Complex components derived from multiple players — OEMs, Tier1s, Tier2s, software stack suppliers, and Semicon chip providers – will drive the Battery Management System, Traction inverter motor control, charger, and the VCU. Integrating and validating them before SoP will become more crucial as challenges, such as having the optimal architecture, multi-core optimization, hardware- software compatibility, compliance to AUTOSAR, and functional safety (ISO26262), come to the fore.
A rethink towards an integrated design is required.
Figure 2 above illustrates how different industry players are exploring possibilities for integrating the power electronics within the EV components to improve the overall energy efficiency and reduce BOM cost and supplier interfaces. The Hybrid and EV powertrains house the battery, DC/DC converters, onboard charger, and traction inverter in separate enclosures. Advances in analog and embedded computing technologies will enable designers to integrate all these using one domain controller and power stage to enhance efficiency and reliability while reducing costs yet meeting functional safety standards.
Such integration will also involve deep-diving into the design to eliminate excess packaging material while making some hardware redundant and lowering the weight and volume of the system. This will ensure EVs stay super-efficient over long distances on a full electric charge. These are placed into the already optimized space to manage higher power density. Apart from the advantages cited an integrated powertrain architecture with fewer parts that can break also resolves the critical issue of safety on the road and offers a more reliable alternative.
Factors favoring integrated one-box control unit
Focus on centralized architecture: Even as new vehicle architecture emerges to ensure the complexity of future-ready transportation stays manageable, there is a clear shift from the current domain-specific E/E architecture toward cross-domain, centralized E/E architectures. This would eliminate individual control units and uses Zone ECUs to connect vehicle computers to the embedded control units and sensors and actuators. Such a design eases system complexity, costs, and ups security. Centralization of data streams enables the zonal ECUs to transmit faster, more securely, and efficiently to the connected vehicle computers and the cloud.
Ensure adoption of multi-core architecture with efficient core partitioning: Embedded system performance is a crucial challenge for EV components, e.g., motor needs to run at 15KHZ frequency with ASIL D compliant software, use of multiple cores efficiently to achieve functional safety compliance and performance target is essential. In addition, integration of multiple EV components into one single ECU will increase performance challenges; scheduling the tasks on multiple cores needs careful analysis, system thinking, and understanding.
Increased savings and efficiencies with integrated power electronics through:
- Efficient single mechanical housing
- Economic single HV input connector & cable
- Sharing common communication channel, integrated shared magnetics to lower BOM overheads
- Adopting a modular approach with power electronics to achieve multiple functionalities of EV components such as common H-bridge control, PFC control, etc
- Optimizing similar design for voltage ranges from 400V to 800 V
- Achieving functional safety compliance with better design
- Using common cybersecurity strategy for multiple components and
- Reducing validation effort for improved efficiencies
Update-able architecture with OTA: To enable EVs to be update-able with new functions when they’re on the road necessitates that a particular buffer of computing power is designed into the in-vehicle server. Updateable over-the-air (OTA) is helpful. One of the in-vehicle servers in the car will act as a central gateway to all incoming and outgoing data and cater to security via the intrusion detection and verification of software certificates features. Transmitting and installing software patches and security updates in a safe and coordinated manner while providing software services to functions in the car is possible.
Seeing the unseen and discovering the insights with Analytics
In developing the vehicles of tomorrow, the automotive industry will face several challenges. One way to translate these into opportunities is to harness the power of Analytics to gain a significant competitive edge. The ability — to use the data to drive sales and retain customers, apply statistical models, and determine market spends, focus on the chinks, and take timely countermeasures and forecast efficiency, operations, and performance – can only drive profitability, enhance market share, and reduce risk. In this context, EV analytics and data management platforms are coming to the fore today.
KPIT has built an intelligent integrated EV analytics and data management platform with features that enable EV manufacturers to improve the consumer experience.
- Simple UI to search, plot & analyze battery data
- Shares charts, plots & insights
- Integrates test labs data to a central data farm
- Pre-builds battery-focused analytics
- Customizes analytics
- Extends integration of test & field vehicle data and data from connected vehicle system to future needs
- Mobile-friendly UX for specific features
Leveraging the data analytics platform to estimate RUL for batteries
A considerable advantage of optimizing data analytics capabilities lies in accurately estimating the Remaining Useful Life (RUL) for batteries. Estimating the State of Charge and the State of Health of the battery offers excellent insight into the status of battery health and energy. KPIT has developed a hybrid approach intelligently combining a physics-based cell model with data-driven machine learning to predict the SOC accurately. The SOC determined is then used for accurate SOH prediction and further extended to predict the Remaining Useful Life of the battery. It has also been successfully combined with a supervised learning neural network to predict the Remaining Useful Life (RUL) of the battery as a measure of cycles, thereby augmenting prognostics capability.
Smart charging solutions
The electric mobility dream is hugely dependent on the availability of ample charging infrastructure. Vehicle manufacturers and suppliers must ensure that the future EVs will be compliant with various global/regional charging standards, e.g., ISO/IEC 15118, GB/T 27930 and CHAdeMO etc. Consumers expect easy-to-use apps and notifications about EV range, availability of nearest charging station, hassle-free payments, and dashboard of the health of their vehicle. A holistic approach towards charging is needed, considering all the vehicle’s technical parameters like EVCC stack, communication gateway, robust charging control ECU. The approach should factor in the interactions of the vehicle/charger with the outside world to locate the nearest charging station, predictive maintenance, SOTA/FOTA, and others. KPIT offers a full suite of EVCC solutions, including ready-to-use software stacks, accelerators, integration, comprehensive testing suite, cyber security, asset management, and predictive maintenance platform.
Summary
The future belongs to electric mobility is a given. How soon would that future arrive might surprise all of us and depends on how fast some of the technologies discussed above come into the mainstream. The automotive and mobility industry and the ecosystem must collaborate to realize a greener and cleaner future.
A software development and integration partner like KPIT, brings global expertise and ready-to-use software platforms and accelerators for electrification components like charger, inverter, BMS, and VCU. It helps OEMs and Tier1s reduce time to market by partnering for prototype to production addressing embedded system challenges.
KPIT Technologies GmbH
Frankfurter Ring 105b
80807 München
Telefon: +49 (89) 3229966-0
Telefax: +49 (89) 3229966-99
http://www.kpit.com
Head of Marketing Germany
Telefon: +49 (89) 3229966-140
Fax: +49 (89) 3229966-999
E-Mail: stefanie.koehler@kpit.com
