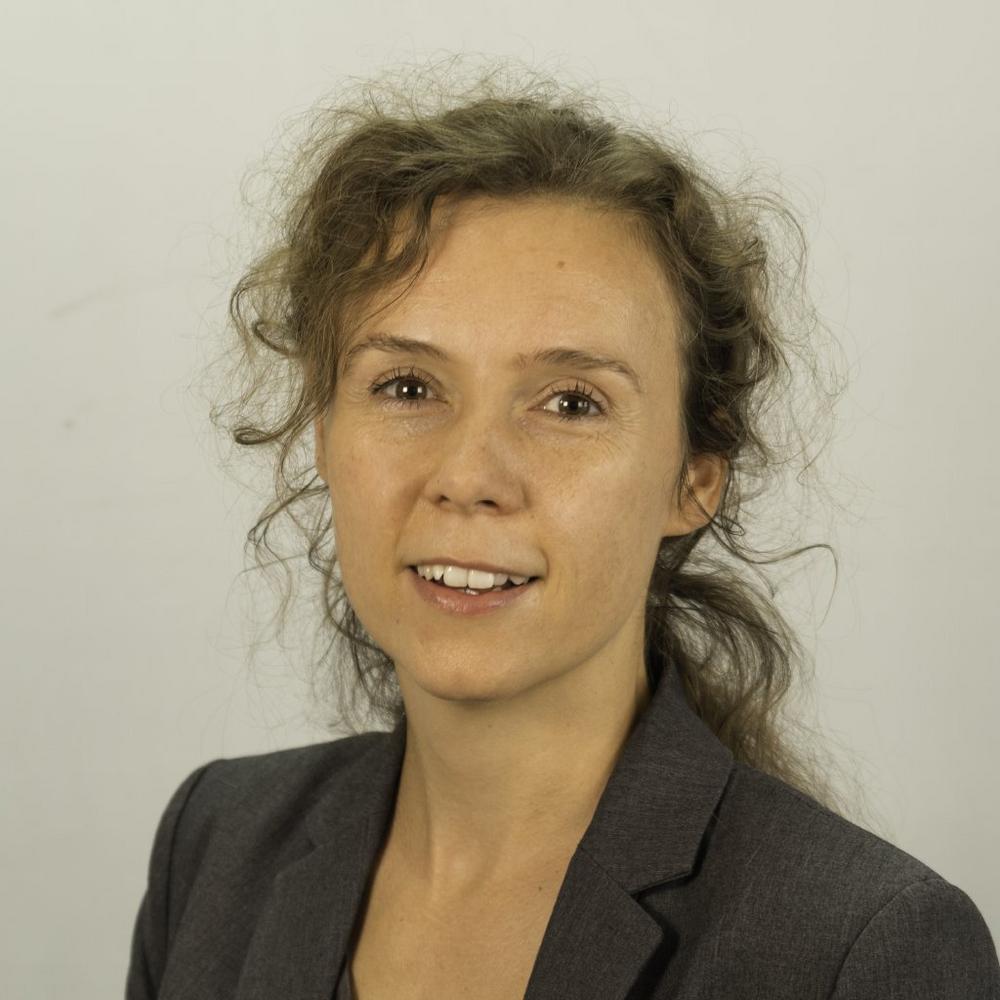
Safe and Effective Use of Warehouse Capacities
Let’s take a look at the steps required for planning a more effective use of your storage capacities, and how best to proceed:
Detailed Analysis of Warehouse Profile
First of all, you need to carry out a thorough analysis of your warehouse profile. How is the material flow laid out and how exactly are the current procedures being applied? This includes the racking configuration, the assignment/retrieval concept, incoming goods, refilling stock, stock management, packing and shipping. Don’t forget to include any seasonal fluctuations! You also need to establish the exact volumes of the incoming and outgoing flow of goods.
Consider the Building Characteristics
In the next step, you need to look at the characteristics and structure of your premises.
1. Could you optimize the ceiling height?
Is the ceiling high enough to extend your storage capacities upwards without jeopardizing warehouse safety? You may have limited floorspace, but perhaps you could create even more usable space by introducing appropriate vertical storage systems? This can make use of the full height of the space, without compromising on efficiency.
For storing pallets, it may be worth investing in some ‘very narrow aisle’ pallet racking (VNA systems), which can be up to 17 meters high. For storing smaller parts, there are modular warehouse lift systems (such as SSI LOGIMAT®), which offer heights of up to 23 m.
2. Could you maximize the depth of the racking?
Effective use of space in the warehouse is not just about the height of the racking system – the depth of the shelves also offers room for maneuver. If you need to store several pallets on each SKU (stock-keeping unit) you may want to consider investing in a pushback rack. This uses a LIFO (last in, first out) system which can expand storage capacities by up to 90% compared to selective racking systems. Once a new pallet is placed onto the rack, the pallet behind it is pushed back a space. When a pallet is removed, the opposite happens. Once the front-most pallet is taken from the rack, all the pallets behind it automatically move forward a space. Storing 2–5 product pallets in a space the width of just one pallet soon multiplies the storage density in your warehouse.
3. Could you install a raised platform?
If the structure of the floor and building will allow, one of the quickest ways to create additional storage location in your warehouse is to install a mezzanine or a raised storage platform. Introducing one, two or even three new storage levels to the warehouse quickly turns otherwise unused space into usable storage. The new level can also to be used for work procedures, such as packing or preparing goods for shipping.
4. Could you revise your current warehouse concept?
When you change the layout of the stored products and SKUs, the racking system needs to be reconfigured. If you try to use the same rack configuration that no longer fits, you will not get optimum use of your storage capacities. A whole new warehouse concept may seem like a big investment to begin with, but it will soon pay off. If you have any doubts as to how to proceed, the SSI Schaefer warehouse experts will be happy to offer you free advice: https://www.ssi-schaefer.com/en-de/1880-1880?pagelabel=de_css
5. Could you change the aisle width?
The most important factors to consider when determining the right aisle width are productivity, space utilization, flexibility, safety, and equipment. Choose an aisle width that will allow industrial trucks like forklifts to travel around the warehouse unobstructed. You may also wish to include a buffer for protruding pallets, which as it is not uncommon in a warehouse for pallets to stick out a little way over the edge of the racking. You are also going to need experienced forklift drivers. Here, you may wish to seek advice from the suppliers of your racking systems and industrial trucks.
6. Could you manage your stock inventories more efficiently?
Get to know your stock inventories in detail: Which products are stored? How large are the quantities of materials processed? How high is your stock turnover, i.e., how often are stored items sold and shipped within a certain time period? Storing unsold goods costs your company money and uses up valuable space in your warehouse. To manage your stock efficiently and avoid excess storage, speak to your customers, as well as your employees in Sales and Production, to get a better understanding of the order patterns.
7. Could you introduce demand-based processes (‘just-in-time’ principle)?
Waiting until they are needed to get the goods in (just-in-time principle) can increase your warehouse efficiency and reduce the costs associated with keeping items in stock. You may wish to discuss the possibility of using this principle with your core suppliers.
8. Could you make extra effort to ensure structured and transparent warehousing?
A tidy and well-structured warehouse is one aspect that is too often overlooked. Ensuring that everything is in the right place allows for much more efficient and productive warehousing. This also makes the work environment significantly safer, by making it easier to identify and rectify potential slipping, tripping, and falling hazards – the most common cause of accidents in the warehouse. Efficiency and safety go hand in hand. A safe work environments means fewer missed working hours, less damaged stock, and fewer machinery repairs.
As you can see, there are many options and possibilities that can be implemented in the warehouse with relatively little effort, but which offer a great deal of added value. Speak to our specialists about how to optimize your current warehouse environment. They would love to help. Contact person: https://www.ssi-schaefer.com/en-de/1880-1880?pagelabel=de_css
You will find more useful information about warehouse safety and racking inspection on our website at: https://www.ssi-schaefer.com/en-de/customer-service-support/warehouse-safety-maintenance
About the Author:
Rabea Menn is Deputy Director of the Customer Services department in Neunkirchen, Germany. The business graduate has been working in various positions in the area of automatic and forklift-served rack systems at SSI Schaefer for over 15 years. Since 2017, she has been in charge of the Customer Services division at SSI Schaefer’s Neunkirchen site and, along with her experienced team, provides all services relating to retrofitting, spare parts, and repairs, as well as inspections for all rack systems.
The SSI Schaefer Group is the world’s leading provider of modular warehousing and logistics solutions. With headquarters located in Neunkirchen (Germany), SSI Schaefer employs approximately 10,500 associates globally, along with seven domestic and international production sites, and approximately 70 worldwide operating subsidiaries. Across six continents, SSI Schaefer develops and implements innovative industry-specific answers to its customers‘ unique challenges. As a result, it plays a key role in shaping the future of materials handling.
SSI Schaefer designs, develops and manufactures systems for warehouses and industrial plants. Its portfolio includes manual and automated solutions for warehousing, conveying, picking and sorting, plus technologies for waste management and recycling. In addition, SSI Schaefer is now a leading provider of modular, regularly updated software for in-house material flows. Its software team, with a headcount in excess of 1,100, develops high-performance applications, and provides customers with in-depth advice on the intelligent combination of software with intralogistics equipment. The SSI Schaefer IT offering, including its own WAMAS® and SAP products, delivers seamless support for all warehouse and material flow management processes. Solutions from SSI Schaefer improve the productivity and efficiency of customer organizations – not least through the highly precise monitoring, visualization, and analysis of operational metrics for proactive intralogistics management.
SSI Schaefer offers highly sophisticated, turnkey systems. As an international player, it can deliver one-stop solutions to all four corners of the earth. Its comprehensive portfolio encompasses design, planning, consulting, and customer-specific aftersales services and maintenance.
SSI SCHÄFER
Fritz-Schäfer-Strasse 20
57290 Neunkirchen / Siegerland
Telefon: +49 (2735) 70-1
Telefax: +49 (2735) 70-396
http://www.ssi-schaefer.de
Marketing & Kommunikation
Telefon: +49 (2735) 70-252
Fax: +49 (2735) 70-382
E-Mail: melanie.kaempf@ssi-schaefer.de
Junior Project Manager CR & PR | Global Marketing
Telefon: +49 (2735) 70-9683
Fax: +49 (2735) 70-382
E-Mail: Annika.Nolte@ssi-schaefer.com
