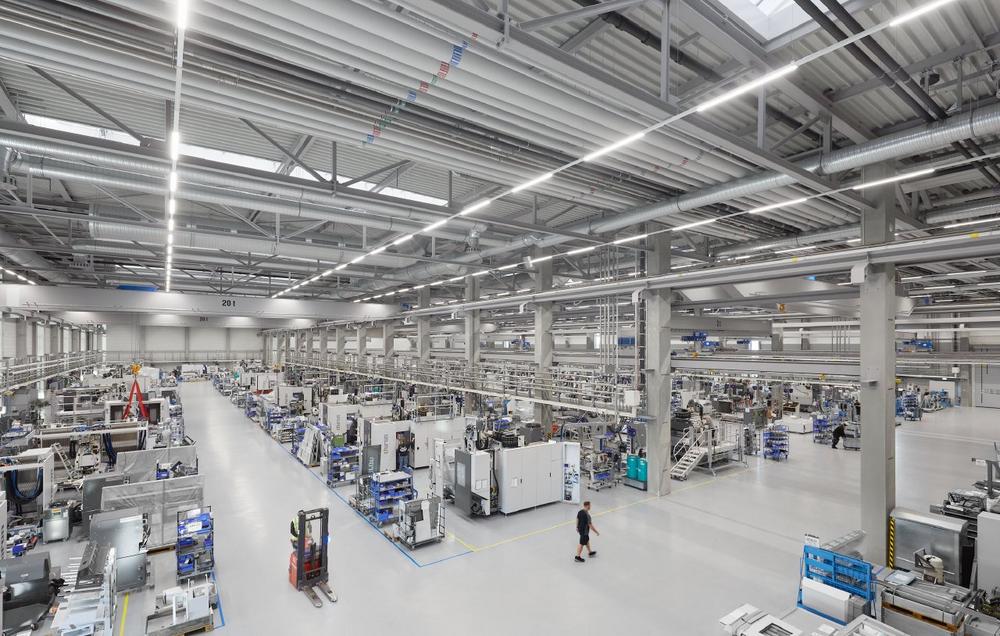
Sustainable thinking – innovative action
From manufacturing a hundred watch cases to large production runs of structural components for e-mobility: All manufacturing consumes resources and energy in proportion to the machining volumes, both in terms of manufacturing the machinery and in terms of using the machinery for production. The declared objective of the CHIRON Group sustainability strategy is to continuously improve energy efficiency at all levels: In production facilities, for products and ultimately for the process solutions that customers use for their own production processes.
Green milestone for CHIRON Group locations
With long-term investments in heat recovery and photovoltaic systems and the commitment to cover any additional electricity requirements exclusively from renewable sources, the CHIRON Group has reached a major milestone and created a sustainable basis: The company’s manufacturing and assembly processes will be overall climate-neutral by end of 2022.
Opting for good-as-new is more sustainable
Conversion and retrofitting, partial and complete refurbishments, component repair: There are many options for increasing efficiency and extending the lifecycle of a CHIRON or STAMA machining center. Regardless of the feasibility of a given renewal measure, the processes covered by the "Refurbishment" expertise are always a more sustainable alternative to purchasing a new machine. A complete machine refurbishment, for example, provides average savings of 40-50% of the total material required for a new machine.
A further component of this sustainability strategy is expanding and actively promoting this business area. The comprehensive range of services that CMS offers for all CHIRON and STAMA machining centers is unique in the industry, and demand remains stable at an encouragingly high level. Specific plans include expanding the assembly and storage area by 80%, increasing personnel to match and preparing employees appropriately for the new challenges and concepts.
Automated repair with LMD triples the service life of cutting rings
The AM Cube 3D metal printer is the only product in the range that does not remove material but instead stacks it up using laser metal deposition (LMD), with powder, wire or both in combination. Additive manufacturing for coatings, repairs and 3D printing is still a recent technology for the CHIRON Group. That said, the technology has matured further with experience and the range of applications has broadened, e.g., to include repairing forged cutting rings.
This results in triple the service life in comparison to previous repair methods. Crucial factors for achieving this include selecting the correct material, ensuring high procedure quality and an automated process. In day-to-day use, the AM Cube provides users with the ability to repair even large tools and molds by themselves. It also boasts reliable spare parts logistics and, as experience and expertise in its use grows, it enables implementation of proprietary product innovations and services – fully in line with sustainability goals.
The CHIRON Group, headquartered in Tuttlingen, Germany is a global company specializing in CNC vertical milling and mill-turn machining centers, as well as turnkey and automation solutions. Comprehensive services, digital solutions and products for additive manufacturing complete the portfolio. The Group has a global presence, with production and development sites, sales and service subsidiaries, and sales agencies worldwide. Around two thirds of machines and solutions that are sold are exported. Key customer sectors are the automotive, mechanical engineering, medicine and precision engineering, aerospace industries, as well as tool manufacturing.
The CHIRON Group is proprietor of the CHIRON, STAMA and FACTORY5 brands for new machines, as well as the automation brand GREIDENWEIS and the retrofit brand CMS. CHIRON’s machining centers are renowned for their highly dynamic design and their precision. STAMA’s focus is on stability and complete machining, while FACTORY5’s expert area is high-speed machining of micro-technical components. GREIDENWEIS is a system partner for custom, end-to-end automation solutions, and CMS provides completely overhauled machines from the Group. The final core area of expertise in the CHIRON Group is in additive manufacturing products and solutions.
CHIRON Group SE
Kreuzstraße 75
78532 Tuttlingen
Telefon: +49 (7461) 940-0
Telefax: +49 (7461) 940-53000
http://www.chiron-group.com
Telefon: +49 (7461) 940-3181
E-Mail: Matthias.Rapp@chiron-group.com

