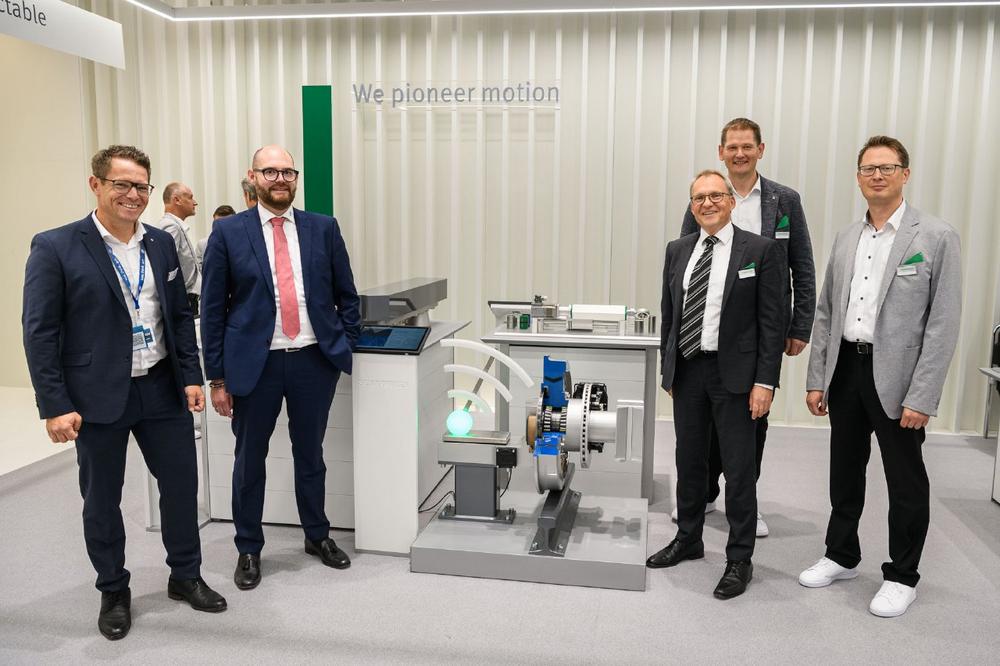
Schaeffler and ZF present results of their successful collaboration on the condition monitoring of rail bearings
- Results from the cooperation between Schaeffler and ZF launched in 2018 to be shown at InnoTrans
- Digital solutions and the monitoring of mechanical drive trains ensure more efficiency in the rail segment
- Open platform concept facilitates other partnerships in the field of continuous condition monitoring and data analysis
Digitalization is one of the most valuable tools for the further technological and economic development of rail transport. The collection of production, operating, and maintenance data creates the basis for extending maintenance intervals and improving safety and reliability. Schaeffler and ZF, two of the world’s leading automotive and industrial suppliers, had already announced their collaboration on the condition monitoring of axlebox bearings at InnoTrans in 2018. The first successful outcomes of this partnership will be presented at this year’s InnoTrans, which takes place in Berlin from September 20 to 23.
Combined expertise accelerates digitalization in rail transport
Four years ago, Schaeffler and ZF announced that they would be working together with a view to improving the condition monitoring of axlebox bearings. Since then, the jointly developed system has been undergoing field tests with several operators and has been continuously refined. Schaeffler is responsible for programming the analysis software for the roller bearings, which is necessary to evaluate the data captured. ZF provides the connect@rail platform with the Heavy Duty TAG sensors and VCU Pro Onboard Unit gateways, as well as cloud and dashboard connectivity. In the meanwhile, several thousand datasets are being analyzed each month – completely automatically. In future, ZF and Schaeffler want to include gearbox bearings in the monitoring system alongside the axlebox bearings.
“With our combined technical expertise and shared understanding of the entire rail system, we are managing to exploit the full potential of digital condition monitoring in this exceptional collaboration,” says Dr. Michael Holzapfel, Senior Vice President Business Unit Rail at Schaeffler, adding “Thanks to the ongoing development of our systems based on our mutual exchanges, we are able to permanently improve rail transport in respect of economic efficiency and reliability. We very much look forward to our continued collaboration!”
“The cooperation with Schaeffler shows that strong partnerships are the key to making the rail sector more reliable and efficient using digital solutions. In Schaeffler, we have found this strong partner – and look forward to our ongoing collaboration,” says Markus Gross, Head of Product Line Rail Drive Systems at ZF.
Extending maintenance intervals and reducing downtimes
The combined expertise of the two companies allows a Rail 4.0 solution with significant added value to be created: The mechanical drive, which is maintained as a separate unit, can be digitally monitored separately right down to its sub-systems and components using just one condition monitoring system. The objective is to allow condition-based maintenance measures to be carried out with the aid of operating data analyses and therefore lengthen maintenance intervals while reducing downtimes.
Open platform concept allows for additional partners
Both partners began tapping into the future opportunities offered by Industry 4.0 at an early stage. ZF supplies sensor-equipped rail drive systems including condition analysis, and Schaeffler enhances the system with its data analytics for axlebox bearings.
With this collaboration, the potential for Schaeffler’s solutions is far from exhausted: The connect@rail conditioning monitoring system from ZF is designed as an open platform concept that can be expanded to include additional partners, enabling other components and even complete bogies to be monitored. This means that rail operators will then no longer have to retrofit new and costly systems, but can add the condition diagnosis of rolling bearings to their existing solutions. Schaeffler and ZF are thus enabling operators not to have to install a separate condition monitoring system for each component, which creates a significant economic added value with minimal outlay.
Find out more about Schaeffler at InnoTrans 2022: Reliable, Predictable, Sustainable – Schaeffler Solutions for Innovations in Rail | Schaeffler medias
As a leading global supplier to the automotive and industrial sectors, the Schaeffler Group has been driving forward groundbreaking inventions and developments in the fields of motion and mobility for over 75 years. With innovative technologies, products, and services in the fields of electric mobility, CO₂-efficient drives, Industry 4.0, digitalization, and renewable energies, the company is a reliable partner for making motion and mobility more efficient, intelligent, and sustainable. The technology company produces precision components and systems for drive train and chassis applications as well as rolling and plain bearing solutions for a multitude of industrial applications. The Schaeffler Group generated sales of approximately EUR 13.9 billion in 2021. With around 83,000 employees, the Schaeffler Group is one of the world’s largest family companies. With more than 1,800 patent applications in 2021, Schaeffler is Germany’s third most innovative company according to the DPMA (German Patent and Trademark Office).
Schaeffler AG
Industriestraße 1-3
91074 Herzogenaurach
Telefon: +49 (9132) 82-0
Telefax: +49 (9132) 82-3584
http://www.schaeffler-group.com
Unternehmenskommunikation Future Trends
Telefon: +49 (9721) 91-5125
E-Mail: johanna.katzenberger@schaeffler.com
